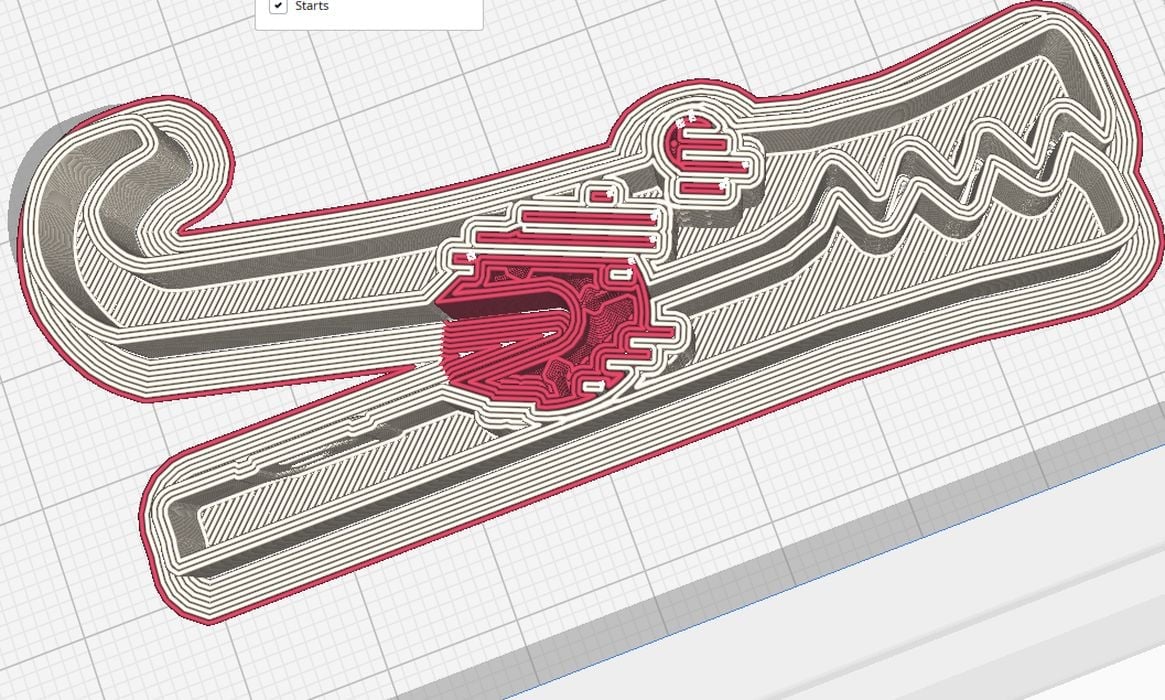
UltiMaker released a new version of UltiMaker Cura earlier this month, and there is a very surprising feature included.
UltiMaker regularly updates their industry-famous job preparation software, which is used not only by UltiMaker for their own equipment, but also for countless other machines in the industry due to the open source nature of the tool.
New releasees typically include tweaks to the GCODE generation, new interface assists and always default settings for additional 3D printers.
This release, 5.3.0, includes something called “material interlocking”, and it’s a bit confusing at first. Let me explain.
When 3D printing with dual extrusion it is possible to print with more than one color. It is also possible to print with a model material and a soluble support material. Those are the typical scenarios for dual extrusion.
But there is another approach that is far more rarely used: mixing different material types. Imagine printing an object with PLA and ABS, for example, or PETG and TPU.
The reason this is rarely done is because it is very tricky to get the materials to interface properly. That’s because the chemistry of the materials differs significantly: ABS does not bond to PLA. If you were to print the two together, they would simply fall apart.
That said, some have done so, and it usually requires special design features to “lock” one type of material to another using hooks, clips, locks or other shapes to mechanically capture what otherwise would be a loose portion of the print.
The difficulty in doing so tends to push people away from using this approach.
Now that could change as Ultimaker Cura 5.3.0 includes material interlocking.
This feature detects the presence of two unlike, unbondable materials and generates a mechanical interlocking structure. As you can see in the image at top, it is much like overlaying two different infill patterns.
This provides an incredibly easy way to process unlike materials within the same print job.
I suspect a very common use case for this feature will be to add flexible TPU material to prints. Normally TPU components are printed separately and then bolted on to a rigid print, but now it can be easily done in a single print job: no assembly!
UltiMaker explains:
”That interesting pattern around the hinge and eye was not designed into this part. Instead, it was automatically generated by enabling the new ‘Generate Interlocking Structure’ setting added to this version of Cura. Note: this setting is only available when using advanced and expert setting presets. Or if enabled via the preferences menu.
This alternating overlapping pattern physically ‘locks’ the two materials together so that the strength of the bond between them is no longer dependent on how compatible they are, but is instead only limited by the strength of the weakest of the two materials.”
How easy is this feature to use? UltiMaker explains:
“You also don’t have to worry about using workarounds such as designing parts that use joints, clips, or fancy print-in-place tricks. You no longer need to print a part in multiple pieces and assemble them using adhesives or fasteners. Instead, just load any part designed for multiple material printing into Cura and slice it with the new ‘Generate Interlocking Structure’ setting enabled.”
The concept for this amazing new feature was developed initially by former UltiMaker staffer Tim Kuiper, who also wrote a research paper on the new approach, “Interlaced Topologically Interlocking Lattice for continuous dual-material extrusion”.
While material interlocking is of no value for those with single extrusion 3D printers, it will be incredibly useful for anyone with a dual (or more) configuration.
Via UltiMaker