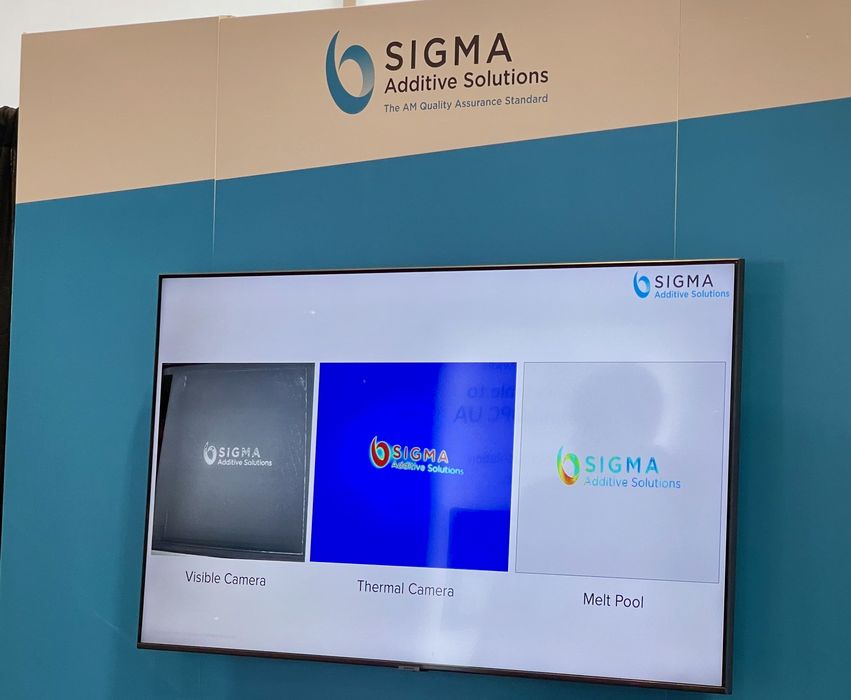
We caught up with Sigma Additive Solutions to find out their latest developments.
You may not have heard of the New Mexico-based company. They don’t build 3D printers, but instead they build software that makes additive manufacturing operations better.
The company’s prime product is Print Rite. It’s a modular software tool that provides deep insight into 3D printing process as they take place. Currently Print Rite has three modules:
- Machine Health: Focusing on the 3D printer itself
- Process Health: Focusing on the process of building parts
- Part Health: Focusing on the quality of the parts produced
How is this done? It starts with collecting data from sensor readings provided by the 3D printers, which are “fused” together and then analyzed by Print Rite’s algorithms. The concept is that the sum of all the data can yield better information than just looking at one or two factors separately.
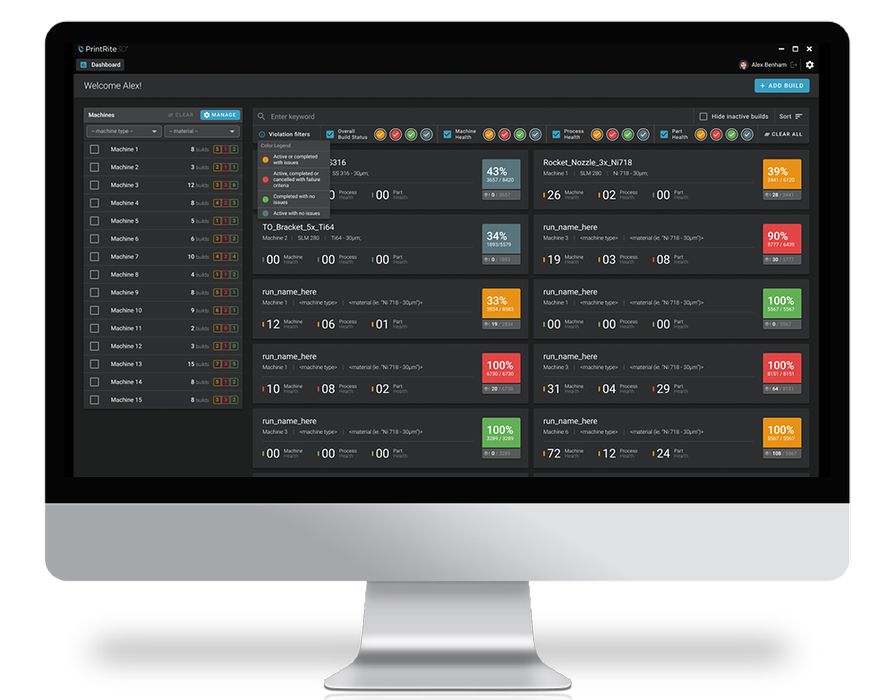
The goal of Print Rite is to identify deviations from “normals”, which can lead to part defects. This information can then be transformed into a “go or no go” question for printer operators. In some cases, this can save considerable expense and time that would otherwise be wasted producing incorrectly formed parts.
The detection of defects can also greatly assist in the development of root cause analysis reports, which are in turn used to correct the problem and avoid it going forward through mitigation strategies.
We were told the latest addition is a new vision module, which is easily added to Print Rite due to its modular design. The new module is able to detect gross defects, spatters, and other effects on LPBF systems.
Recently they’ve joined EOS’ partner program, and they are working with the company to integrate sensor data collected from that company’s equipment. This will allow more seamless use of Print Rite on EOS equipment.
Sigma Additive Solutions is also able to collect data from fleets of machines, which can provide additional insights. Consider an example where there are multiple instances of a particular 3D printer: deviations in operation between them could indicate slight or upcoming issues with a specific machine.
All of this is funneled into Print Rite’s single interface, where these data and insights can be easily processed by an operator.
This all sounds very good, and clearly would be beneficial to those operating fleets of industrial 3D printers, but even so, Sigma Additive Solutions tells us there are many who don’t use their software.
Instead they find some crusty old operators still using spreadsheets to somehow manage their equipment. It is the 21st century, and I believe these organizations should consider moving into more intelligent methods of manning their additive manufacturing operations.