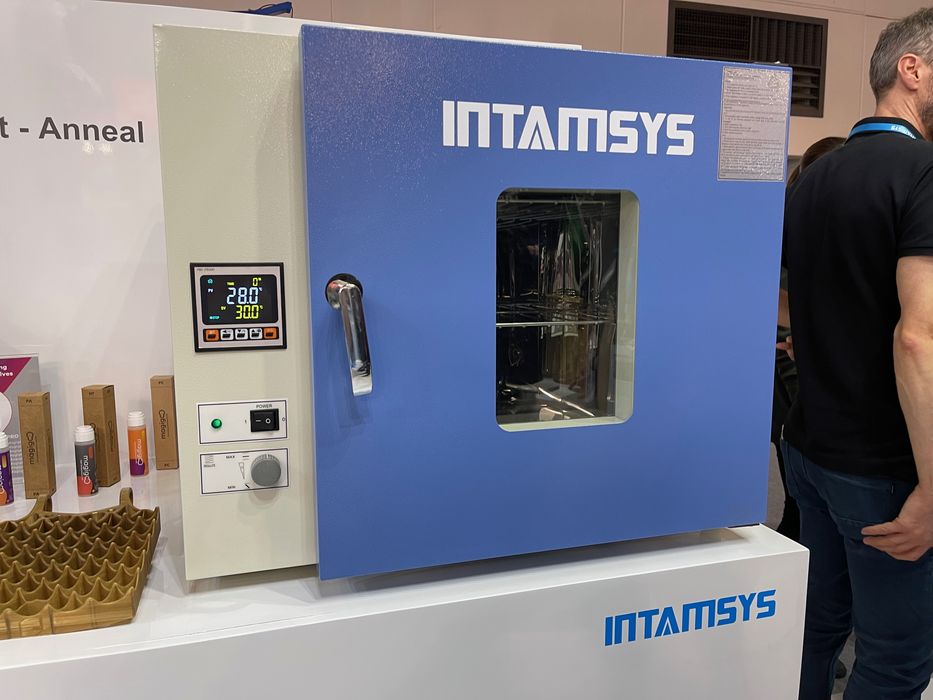
Intamsys has a new post processing oven, and a very unique application for high temperature materials.
In a recent chat with the company we learned the company is developing a specialized oven for their product line.
Why does one need an oven? Aren’t Intamsys’ high temperature 3D printers already hot enough? The answer lies in post processing. It turns out that some high temperature materials can be made even stronger by an application of heat after the print completes, called annealing. The heating is done through a specific thermal profile for the material to achieve the desired part strength.
The oven would accompany Intamsys 3D printers to add another step to the production process, but produce better parts.
We also had a look at a very unique application of high temperature 3D printed parts by Intamsys.
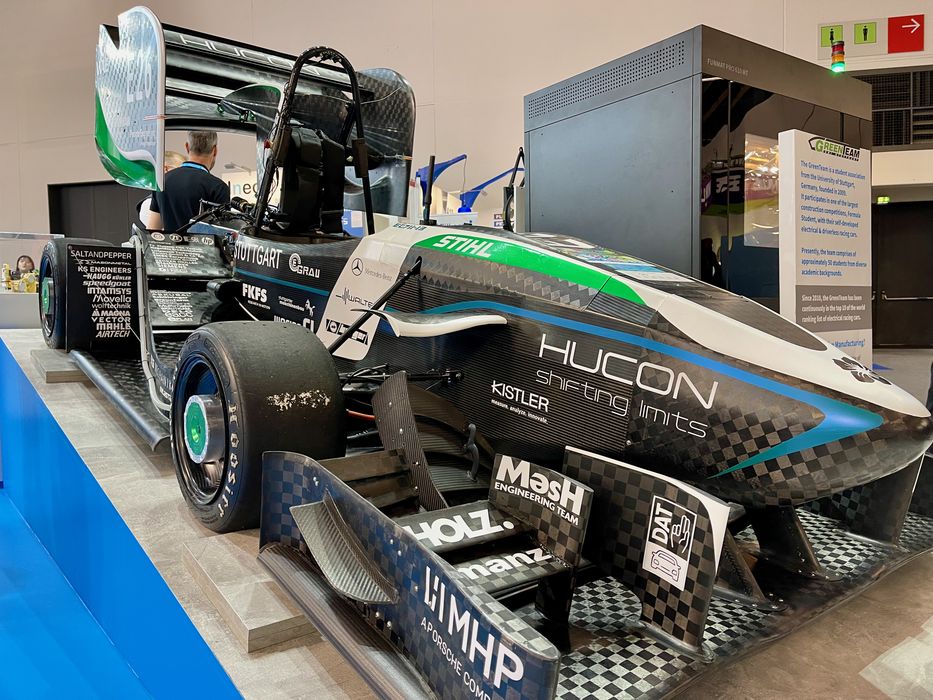
They partnered with a racing car company to help produce parts for the above vehicle. While most of the car are clearly not 3D printed, there are quite a few that were.
Which parts are they? It is quite hard to tell by eye. I couldn’t find them myself, as I was looking for the giveaway layer lines or other surface disturbances that are typical of 3D prints.
I could not find any.
It was then pointed out that several of the airfoils are 3D printed. But they didn’t look at all like 3D printed parts; instead they appeared to be standard carbon fiber sheet layups.
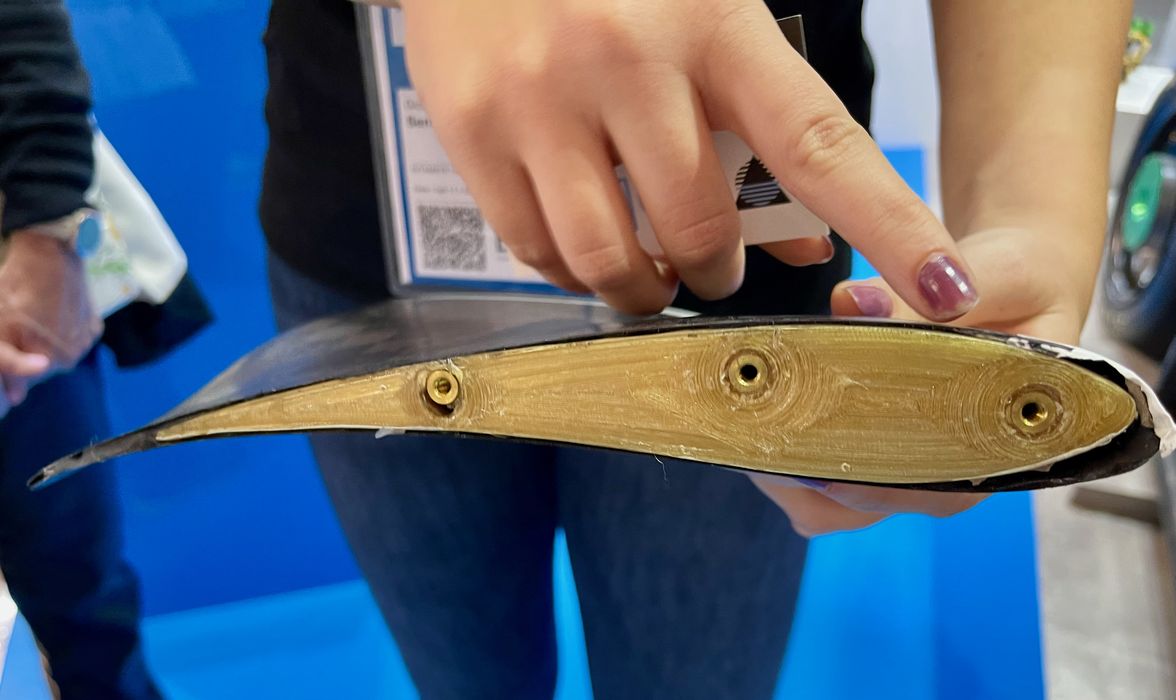
Then I was shown this, which tells what’s actually going on. The interior of the airfoil is 3D printed in a high temperature, lightweight material, such as ULTEM. Then carbon fiber sheets are laid on top of the print, which controls the precise geometry of the airfoil.
The result is a very lightweight airfoil with a very smooth surface. It’s also extremely strong due to the carbon fiber.
This is a very interesting hybrid approach for leveraging 3D printing in a way that I hadn’t seen previously. There are very likely thousands of ways to apply this approach in other applications.
Via Intamsys