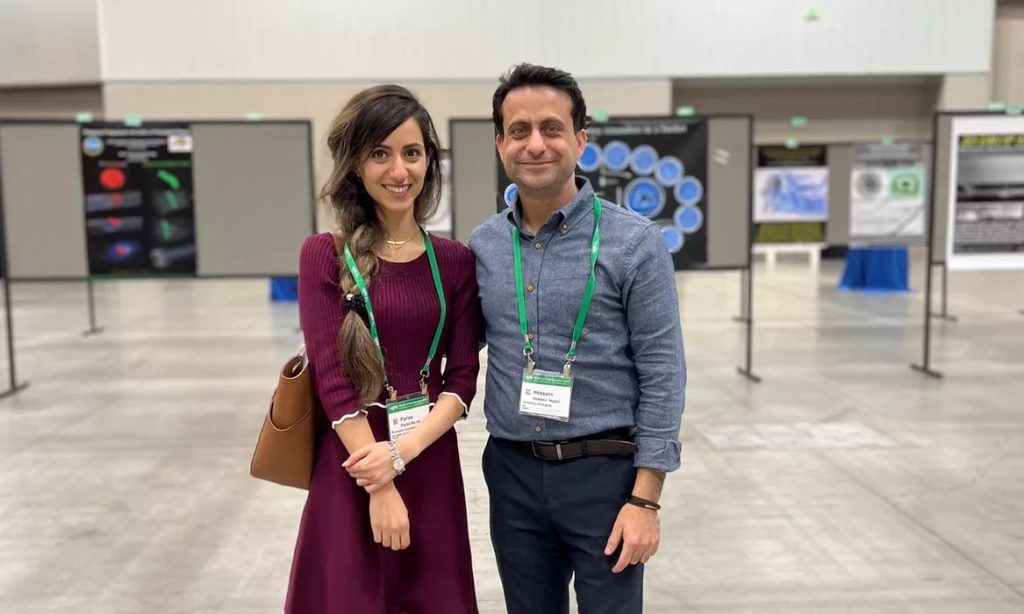
Researchers from the University of Calgary have developed a “liquid in liquid” 3D printing material.
This may be one of the most unusual approaches to 3D printing I’ve yet seen: printing liquids inside of a liquid medium. You may initially think this is impossible, as the liquids would mix and disperse immediately, and that would be the normal case.
There have been methods developed previously to “print” drops. Imagine a syringe moving to a position inside a liquid chamber, and issuing a single drop. That works, but you cannot print continuously.
However, here we have a new material that can maintain its structure and can thus be positioned in 3D space within a liquid and apparently printed continuously.
The approached used to develop the material was quite straightforward, and involved creating an “emulsion zone” using oil, water, silica nanoparticles and other materials. They explain:
“We describe a new approach to print liquids in a liquid medium by the formation of an emulsion zone at the oil-water interface. Silica nanoparticles are incorporated into spontaneous emulsification systems of sorbitan monooleate (Span 80) micellar solutions. Upon contacting an oleic micellar solution with the aqueous silica dispersion, tiny droplets nucleate inside the micellar solution close to the oil–water interface, forming an emulsion phase. The rapid expansion of the interfacial area due to the low oil-water interfacial tension creates interconnected structures of oil and emulsion phases. The spontaneous formation of an emulsion phase at the oil-water interface and its further penetration inside the bulk stabilizes liquid filaments with walls made of submicrometer emulsion droplets that can be used as inks for liquid-in-liquid printing.”
Here is what they achieved:
“We experimentally demonstrate the printed aqueous phase is emulsified in-situ; consequently, a 3D structure is achieved with flexible walls consisting of layered emulsions. The tube-like printed features have a spongy texture resembling miniaturized versions of “tube sponges” found in the oceans. A scaling analysis based on the interplay between hydrodynamics and emulsification kinetics reveals that filaments are formed when emulsions are generated and remain at the interface during the printing period. Stabilized filaments are utilized for printing liquid-based fluidic channels.”
Why create such a material? It turns out there a number of medical and industrial applications. The research paper explains further:
“Printing a structured network of functionalized droplets in a liquid medium enables engineering collectives of living cells for functional purposes and promises enormous applications in processes ranging from energy storage to tissue engineering.”
This technology may not be for everyone, but it is certainly fascinating and, like many entirely new technologies, may open up new avenues for 3D printed applications.
Via University of Calgary and Nature