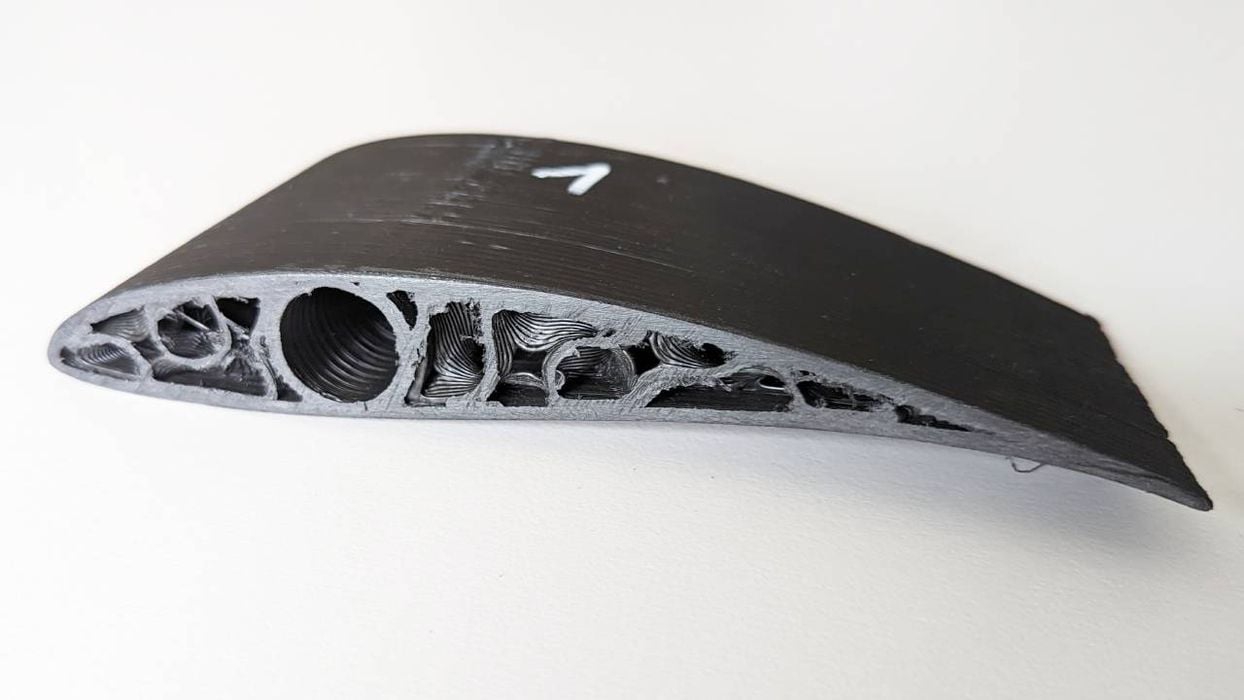
Researchers at TU Berlin used 3D printing in unique ways to rapidly develop a new wind turbine blade design.
A report from BigRep explains how the researchers were able to use the large-format devices to prototype highly advanced blade designs. These designs were 3D printed and then directly tested to evaluate their properties.
Wind turbines are enormous, and it’s impossible to print full blades, at least not yet. However, by printing smaller scaled versions of a design it is still possible to measure performance and determine whether it may work when scaled up. In this case the researchers chose to print 1m length blades for testing.
The benefit of 3D printing is that it is trivial to transform a digital design to a physical representation. This is far less effort and effective than using other making techniques. The researchers used BigRep’s ONE system, and, ironically, BigRep’s BLADE software, along with the company’s PRO HT material.
While the surface design of the blade model is the purview of the researchers, the interior of the print is in the 3D print realm. Experiments involved changing the number of perimeters and testing various infill structures. They eventually decided on gyroid structures, as that geometry provides more or less equal strength in all directions: turbine blades rotate fully when operational. This also makes the blade lightweight, and turn more easily in the wind.
Testing involved a series of mechanical tests that revealed where major stress occurred. This allowed the researchers to tune up both the design and the print parameters to gradually evolve towards an optimal configuration.
They also performed wind tunnel tests to determine the wind catching efficiency. Their findings were quite interesting:
“The wind turbine blades were designed to work best at a certain speed, but when they tested it, the researchers realized it worked better at a higher speed than what they had initially planned. Its maximum efficiency was at 5.4 times the speed of the wind, rather than the 4 times it was designed for. This was because the turbine was engineered based on natural wind flow, not the conditions inside the wind tunnel where it was tested.”
Finally, the project did not involve applying coatings to the blade, which is quite surprising given the presence of layer lines created by the printing process. These might have interfered with the aerodynamic flow, but apparently not.
The lack of coatings meant that the blades produced were of “pure” 3D print material, and thus able to be recycled for reuse. If this concept transforms to large scale implementations, it could be quite helpful to the environment.
The research project not only showed that it is entirely possible to develop efficient wind turbine blade designs through iterative 3D printing, but also that this type of exploratory project is very feasible with 3D printing.
Via BigRep