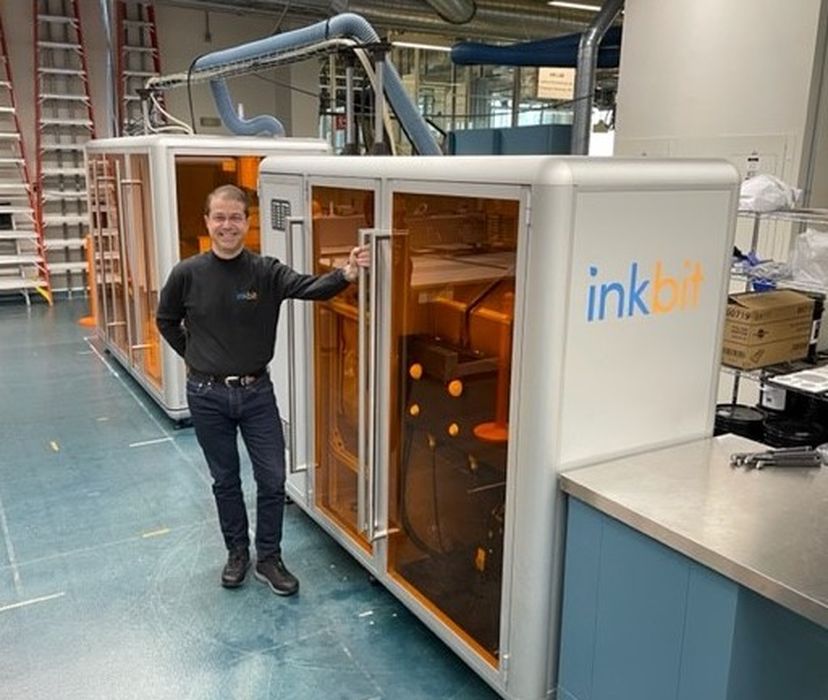
We were able to take a closer look at Inkbit’s new 3D print production system.
The Boston-based company made news last year when they revealed their unusual VCJ (Vision Controlled Jetting) 3D printing process. VCJ involves uses high resolution inkjets to selectively deposit up to four different materials, layer by layer.
That might seem typical among material jetting processes, but VCJ adds some sophistication. The process involves use of vision-based AI tools to monitor the progress of each layer. Should something be amiss, for example a stuck jet or material movement, the system can take action immediately to recover the print and continue successfully.
The Vista VCJ system prints within a large 500 x 250 x 200 mm build chamber, suitable for low volume production runs.
One very interesting aspect of VCJ is that one of the materials could be used for support. Inkbit has been using a wax material for this purpose, as you can see in this image.
For this job, the Vista took around 12-13 hours to complete printing. VCJ is pretty fast, reaching speeds as high as 16mm per hour.
The post processing of a VCJ print is interesting. The first step is to melt the wax support material away, which occurs at only 60C. Inkbit representatives told us this process can take up to 24 hours to complete.
After that stage the loose parts are rinsed for 30 minutes, followed by sintering to form solid parts.
Unlike some other production 3D printing processes, Inkbit’s VCJ does not have a warm up or cool down period that can occupy a significant chunk of the workflow. This could be a notable factor for companies choosing a production AM system.
Perhaps the most interesting aspect of Inkbit’s system is that it is able to produce volumes of multimaterial parts efficiently. Above we see a complex component that is made from two different materials.
The company has also developed a series of resin materials for use with VCJ, including an interesting elastomer. This stuff has a shore hardness as low as 25A, which is extremely soft. This part was made from the material, and it was large (30cm across), heavy and quite floppy. There are applications that require highly flexible materials of this type.
Inkbit also offers a high impact material that’s resistant to UV exposure, as well as high temperature materials that can be used in thermally stressed applications, up to 120C.
Inkbit has taken a number of steps to make their system more compatible with production environments. For example, the resin tanks are huge, containing 80L of resin, allowing for long production runs. The resin tanks are also safety oriented, as they have quick-connects that prevent spills and exposure to toxins by operators.
We were told they’ve also begun development of automation systems to simplify the work required to handle post processing using a conveyor belt approach. While this has yet to be completed, the idea is quite complementary to their focus on production applications.
Their first machine install at a customer began a couple of weeks ago, and this week they announced the system is now operational. Inkbit said:
“Inkbit announced today that the first of its kind Vista production additive manufacturing system is now operational at the Saint-Gobain Research Cross-Business R&D Center, a multidisciplinary research site developing processes and products for global businesses across numerous industries.”
My thought is that Inkbit’s unusual VCJ process and materials offer manufacturers a good option for low volume production. The combination of high throughput, quality controlled results and automation could be irresistible.
Via Inkbit