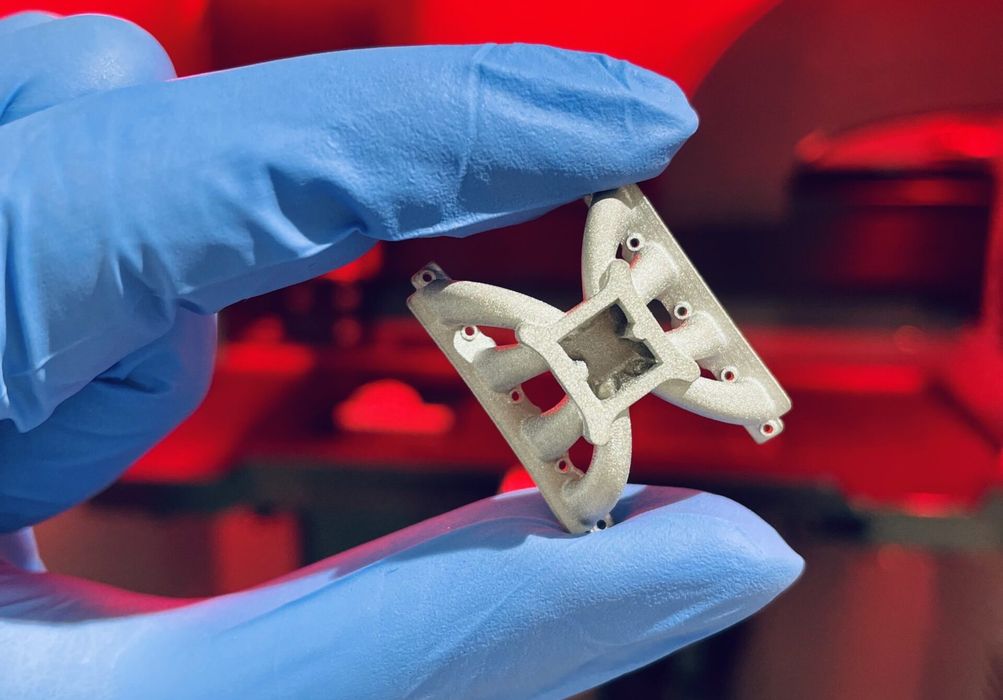
Incus has completed a project that verified the possibility of 3D printing metal objects from scraps on the Moon.
That’s a bit of a statement, so let’s take this apart.
Incus developed the Lithography Metal Manufacturing (LMM) process, which is a bit different from the typical LPBF metal 3D printing process. While LMM still uses metal powder, it’s mixed in with a photopolymer resin.
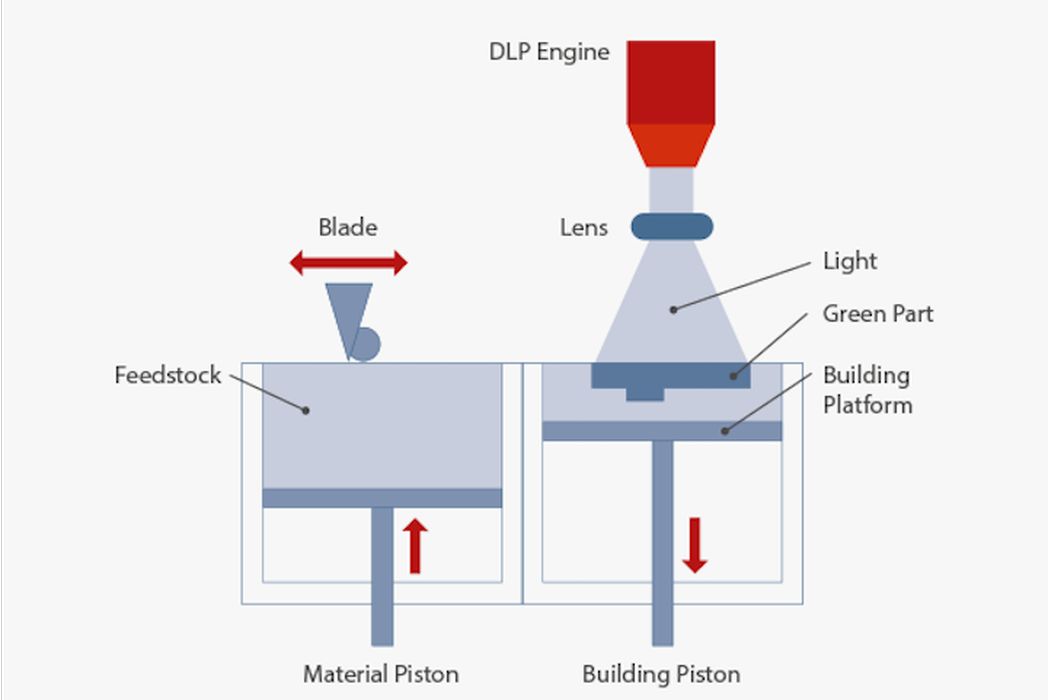
The resin is spread out on a layer with a blade, and then selectively cured in a manner similar to SLA systems. This process repeats, layer-by-layer, until the object is complete.
A 15-minuted “de-caking” process removes material to reveal a green part, which then undergoes a debinding process to remove the polymer, and finally a sintering process to fuse the metal particles together.
LMM can be used with a wide variety of metals, as they are simply mixed in with the resin. Incus said LMM can work with “316L stainless steel to titanium, copper, tungsten, precious metals, carbides and many more.”
The news is that they’ve completed a project with the European Space Agency (ESA) to test the possibility of using their process at a future lunar base.
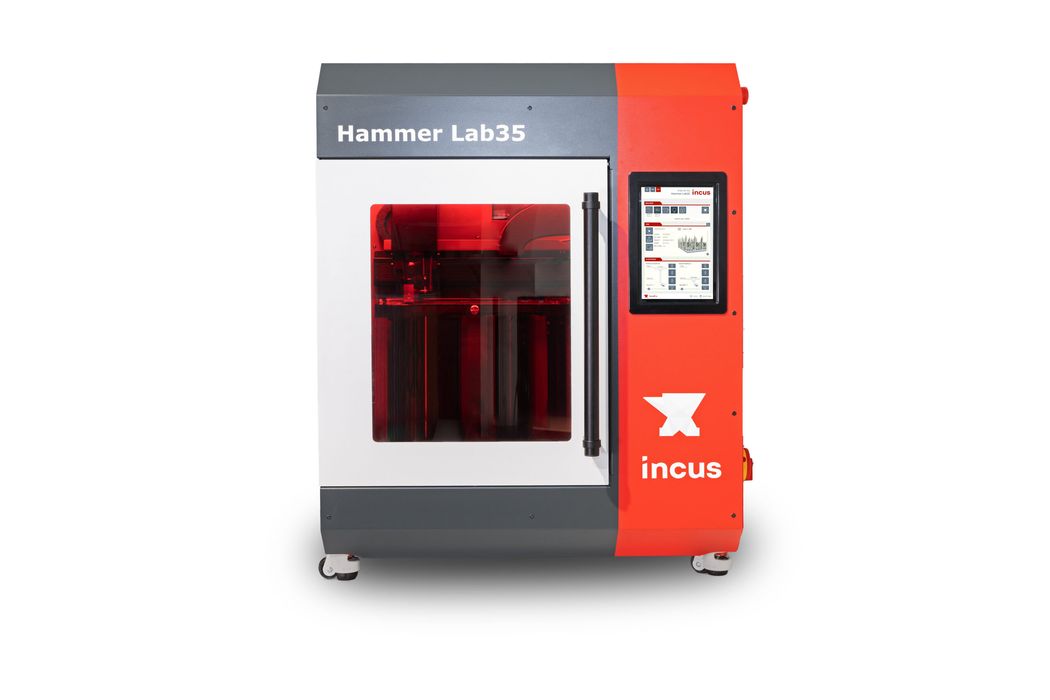
The idea is to recycle scrap metals at the site to produce new metal objects using LMM. Recycling materials would be sourced from scrap equipment sent from Earth to the Moon that is no longer required, or even from crashed vehicles. Recycling approaches would be extraordinarily valuable on the Moon, because the cost of shipping new metal from Earth is prohibitively high.
Incus explains:
“The project’s goal was to develop a sustainable process that uses lunar resources and recycled scrap metals, eventually contaminated by lunar dust, to produce spare parts on-site which could help and enhance human settlement on the Moon. The successful use of lunar resources and recycling of scrap metals is vital to the creation of a sustainable Moon base. Lithography-based Metal Manufacturing was selected for its ability to print from recycled metal waste and its ease and safety during printing and post-processing.”
This isn’t as simple as installing a LMM device on the Moon and operating it. The lunar environment includes a series of technical challenges, including extreme temperature variations, vacuum, contamination from lunar dust and a lower level of gravity.
Was the experiment successful? They explain:
“The biggest challenge for lunar additive manufacturing is the harsh lunar environment, including the atmosphere, gravity, temperature, radiation, and the potential contamination of moon dust. However, the Incus 3D printing solution, Hammer Lab35, was able to print recycled Titanium powder while maintaining proper part quality. The produced parts demonstrated a high level of strength, comparable to Metal Injection Molded Titanium parts standards (1000-1050 MPa).”
They verified that no major changes to the equipment would be required, although it would be placed within a human-rated habitat environment.
It’s important to note, however, that the printing would be only one step in the recycling process. Preparation of suitable powder, for example, would require locating suitable scrap materials, transporting them to a recycling center, and transforming them into printable powder. That may seem like a lot of effort, but with the cost of lunar shipments, it just might be worthwhile.
Via Incus