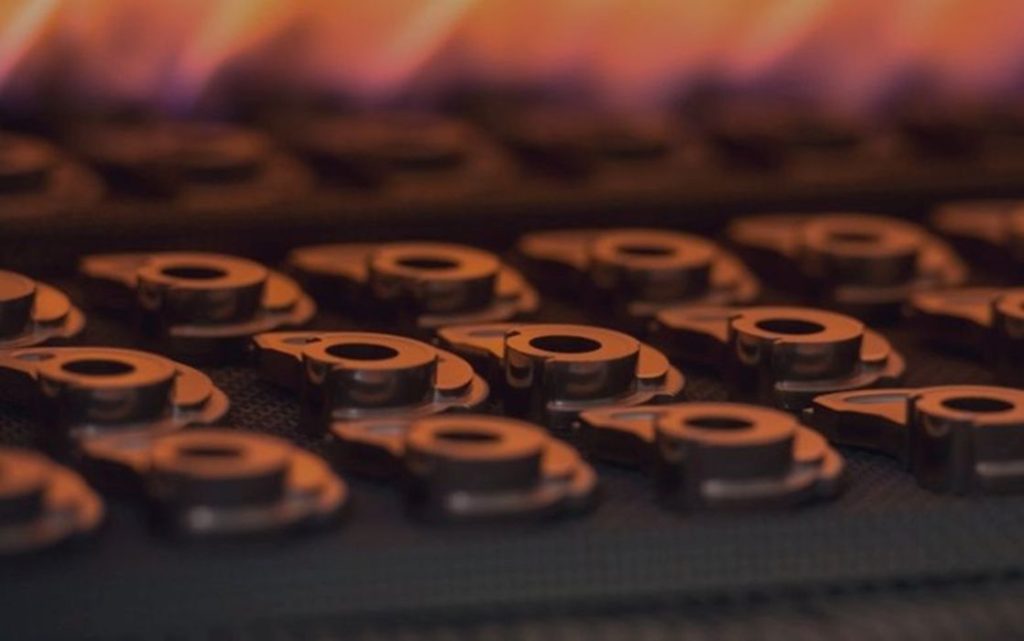
Charles R. Goulding and Preeti Sulibhavi examine a partnership between AM and industry.
HP has disrupted the 3D printing industry once again. Combining forces with GKN Additive and Schneider Electric, the combination has simplified 3D printing while speeding up the process as well. In what is referred to as a giant leap in helping to scale 3D metals to mass production, HP’s new Metal Jet S100 Solution in collaboration with GKN Additive has helped to create Schneider Electric’s new filter used on Schneider Electric’s NSX breaker.
This could not have been achieved with conventional industrial manufacturing capabilities due primarily to shape and material complexity. HP Metal Jet technology not only facilitated the design of new power filters shapes that reduce gas, pressure, and heat impact in a more limited space, it also resulted in significant productivity gains and environmental benefits.
HP, Inc.
HP is a leader in the 3D printing industry. With a wide range of printers available, HP helps make 3D printing production ready and reliable. The HP Multi Jet Fusion works by controlling voxels. In 3D design and printing, a voxel represents a value on a regular grid in a three-dimensional space. By controlling the properties of each individual voxel through agents, HP Multi Jet Fusion can produce parts that can’t be made by other methods.
Schneider Electric
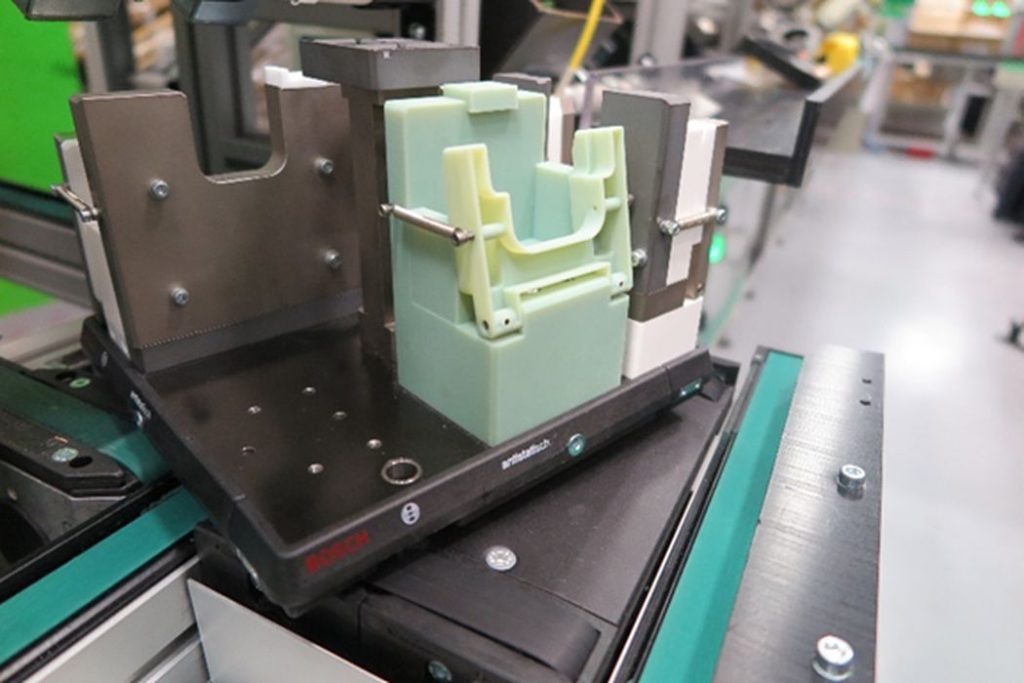
Schneider is an indisputable leader in the energy management and automation industry. Industrial giant Schneider Electric has now partnered with 3D printing firm Stratasys to employ additive manufacturing in its Industry 4.0 implementation.
Yann Rageul, Director Manufacturing Solutions EMEA at Stratasys, said,
“As we work our way through the global pandemic, we’ve seen clear indications that additive manufacturing can play a key role in enhancing the traditional supply chain and conventional production lines…we expect to see an increase in company’s adopting the technology at a strategic level such as Schneider Electric, who continue to successfully drive digital transformation across the business.
Not only does additive manufacturing enable them to increase flexibility within production and reduce dependency on suppliers, but it also opens up the ability to make significant operational efficiencies across product development.”
GKN Additive
GKN is the world-leader in developing atomized metal powders for various 3D printing applications. A leader in the global scale additive solutions for automotive and industrial verticals, GKN is working to provide disruptive technologies and flexible AM. GKN powders allow for 3D printing with more complex geometries and higher densities with improved dynamic qualities.
The Research & Development Tax Credit
The now permanent Research and Development (R&D) Tax Credit is available for companies developing new or improved products, processes and/or software.
3D printing can help boost a company’s R&D Tax Credits. Wages for technical employees creating, testing and revising 3D printed prototypes can be included as a percentage of eligible time spent for the R&D Tax Credit. Similarly, when used as a method of improving a process, time spent integrating 3D printing hardware and software counts as an eligible activity. Lastly, when used for modeling and preproduction, the costs of filaments consumed during the development process may also be recovered.
Whether it is used for creating and testing prototypes or for final production, 3D printing is a great indicator that R&D Credit eligible activities are taking place. Companies implementing this technology at any point should consider taking advantage of R&D Tax Credits.
Conclusion
There is no room for error when producing at scale. That is why the HP/Schneider/GKN partnership is so strategic for the 3D printing industry to expand in industry and operations. We see this partnership as a sign of good things to come for the industry.