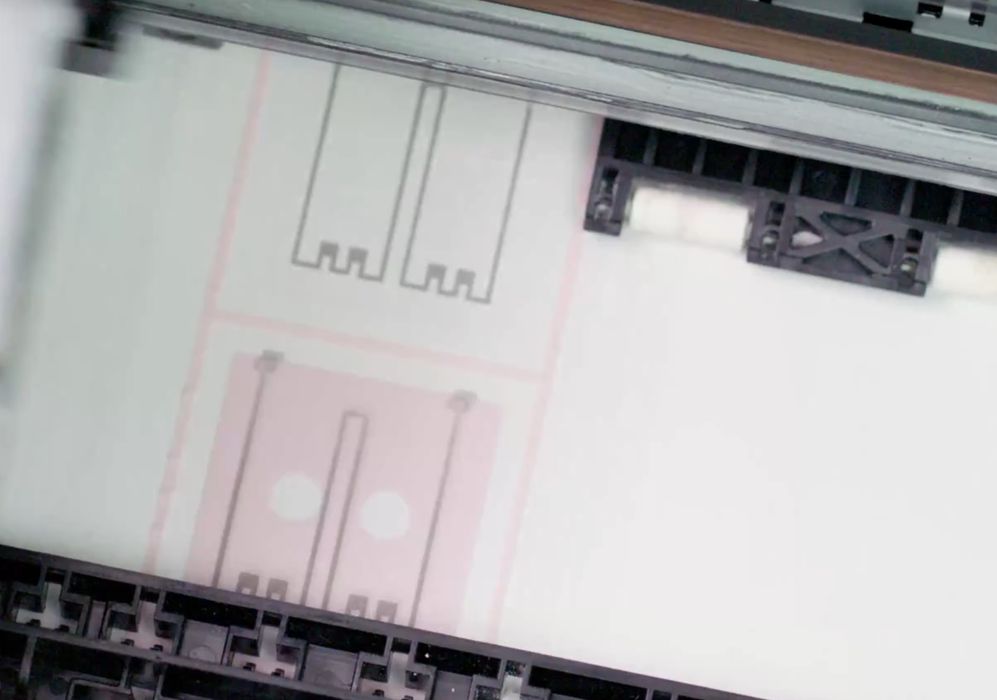
I spoke with Sakuú’s VP of Marketing and Business development, David Pederson, to find out more about this mysterious 3D print startup.
Sakuú is one of many stealth 3D print startups, and we wouldn’t know anything about them except that they’re gradually becoming visible.
We’ve published two prior stories on this 50-person company, one speculating about their mysterious 3D print process based on the few crumbs we could find online, and a second discussing three intriguing patents the company was recently assigned.
Now we’ve been able to speak directly with their representatives and ask some questions about their process and what they intend on doing with it.
Sakuú Background
It seems that Sakuú began as a collision between technologies. Many of the Sakuú founders came from the semiconductor industry, who were familiar with additive manufacturing and thought there were better ways to solve key problems using this knowledge.
Aside: I’ve heard this story before — Essentium was founded by folks also from the semiconductor industry, where they were able to build an extremely fast industrial 3D printer. Could Sakuú be doing something similar?
Sakuú envisioned a new kind of 3D printing process that was actually a blend of multiple processes. In fact, their process is literally multiple processes.
Sakuú 3D Printing
This is the magic part: each layer is produced separately by independent 3D printing processes, and then joined together. This is quite different from the “deposit in place” approach of all current 3D printing processes. Instead, Sakuú can have multiple processes work on layers that are then bound into a full object.
Here is a short video from Sakuú showing some hints of how the mechanics of the system will work:
They have already been able to 3D print conductive wiring in 3D prints using their process, creating an ability to produce electrically powered objects. However, at this point they have not yet established a pick-and-place style system for advanced electronic components.
One of the issues they’ve worked on is cross-contamination between different print units. This is a problem not seen in other 3D print processes for obvious reasons.
I asked how Sakuú is able to bind layers together, as this could be a complex issue. The response was that they have developed a propriety technique that uses mechanics and material chemistry to accomplish that task. One of their materials, Poralyte, is used to create voids and support structures.
While they are initially focusing on use of ceramics and metals for producing batteries, apparently there is nothing stopping the process from eventually using other 3D printing processes. For example, PBF, binder jetting and SLA approaches could be integrated, which could potentially create a universal 3D printer of sorts.
However, as a startup they are obligated to focus on a single market to get established, and that’s the solid state battery market. After success there, they may then consider using the flexible process elsewhere for other applications.
Sakuú Implications
There are several huge implications that come with this unusual 3D printing process.
First, it means that you could potentially have different 3D printing processes working on the same object simultaneously. For example, you could produce objects with ceramic, metal and polymer — and Sakuú says this can be done on the same layer using their process.
The second implication is that it would be possible to scale up the system. Imagine, for example, that one process type takes 2X longer to produce a layer than another process. You would then have two print units working the slower process to keep up with the faster process unit. That is how the Sakuú process could integrate processes of differing speeds.
Another implication is scalability. By adding more print units, one could make the overall process have much more throughput. Pederson describes the system as “very, very scalable!” Large implementations of the system could produce “hundreds of thousands of batteries per month”.
The result should be a system that can very rapidly produce objects in high volumes.
Sakuú 3D Printed Batteries
But what application could you use this process for?
Sakuú selected battery production, where the batteries are a combination of ceramic and metal. Their initial market would be the “two wheel” electric vehicle market, which includes scooters, e-bikes, etc.
3D printed batteries are not a new thing; there are many parties working on the problems and several have actually produced 3D printed batteries with differing approaches. However, none has developed a process that’s capable of making such batteries at scale.
Sakuú feels that their expertise in the semiconductor industry, where millions of parts are produced with advanced equipment, enables them to produce equipment capable of 3D printing massive quantities of solid state batteries.
The company is so focused on this market that the company’s original name was “Keracell”. However, with the realization that their flexible 3D printing process could have many more applications, they changed their name to “Sakuú”.
Why “Sakuú”? The word means “Platform” in Farsi, and “Bloom” or “Coming out” in Japanese. This is very appropriate recognizing the flexibility of the Sakuú process. It is indeed a platform.
Sakuú Availability
The system is being tested quietly today by a few friendly beta testers, and it’s expected Sakuú will deliver an “alpha” version of the system by the end of 2021, with an industrial platform by the end of 2022. They are also in the process of setting up a pilot line in San Jose, California for client exposure and teaching.
Based on their research with potential clients, they expect to offer the platform on a subscription basis, rather than selling equipment directly.
The company today is in the midst of a Series B investment raise, so it’s clear there are many who believe in the concept and are willing to invest large sums.
There’s much more to know about the Sakuú process, but we’ll have to wait a bit longer to find out. In the meantime it’s exciting to speculate about where this technology could go in the future: a 3D printing platform that can integrate all processes and, in theory, make nearly anything.
Via Sakuú