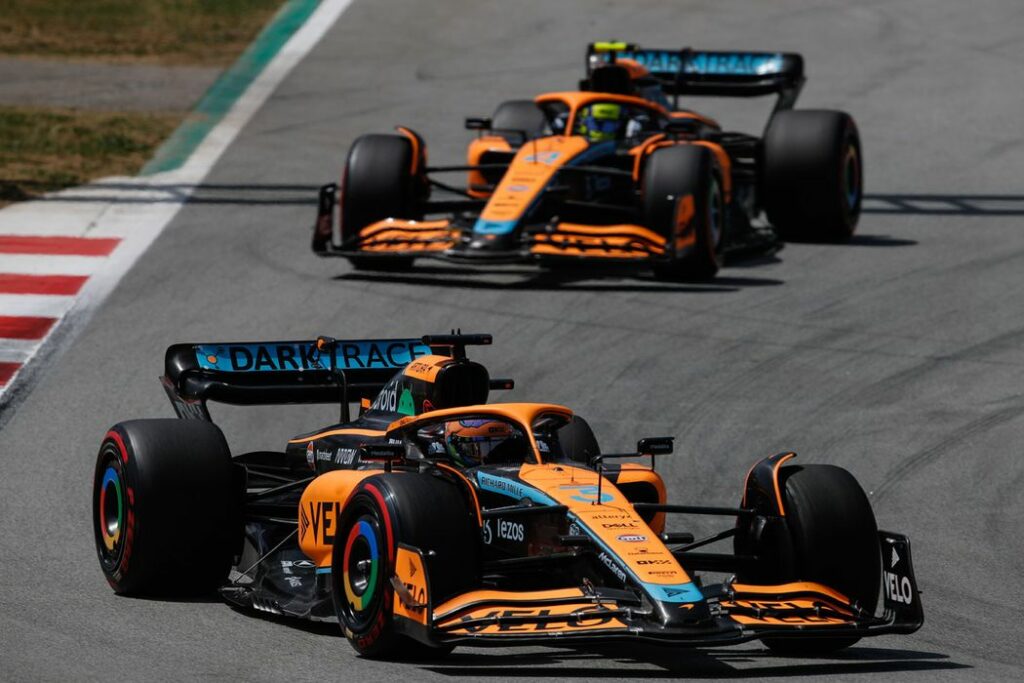
Stratasys revealed some of the ways that 3D printing is used by at least one F1 team.
The secretive world of F1 design doesn’t often reveal exactly how things are made due to the competitive nature of motorsport, but a release by Stratasys shows some interesting techniques being used by the McLaren F1 team.
The team, based near London in Woking, operates a “fleet of in-house printers” that they use to print “all aerodynamic parts”.
That’s a surprise to me, as I thought the technology was still being used for prototyping. This is not the case, according to McLaren Racing’s head of Additive Manufacturing, Tim Chapman, who said:
“Stereolithography technology and the materials have evolved – changing the way we use it. We do not just manufacture prototypes anymore; we now produce many full-scale components and full-size tooling.”
This is quite advantageous for McLaren, who would otherwise be using time-consuming and lengthy traditional making processes for such items. Complicating the matter further is that the team isn’t making millions of parts on which they can defray tooling costs; instead they make much smaller quantities of parts.
With a fleet of 3D printers on site, they can very quickly produce parts of new designs without issue: no tooling delays occur. For an operation known to be constantly changing designs, additive approaches are essential.
One very interesting approach used by McLaren Racing is for miniatures, which is something you might not expect. Apparently the team produces small versions of their newly designed vehicles for aerodynamic testing in wind tunnels.
This is an application that requires a very stiff material to withstand the wind forces, particularly for miniaturized features, and also extremely fine resolution to enable smooth surface finishes.
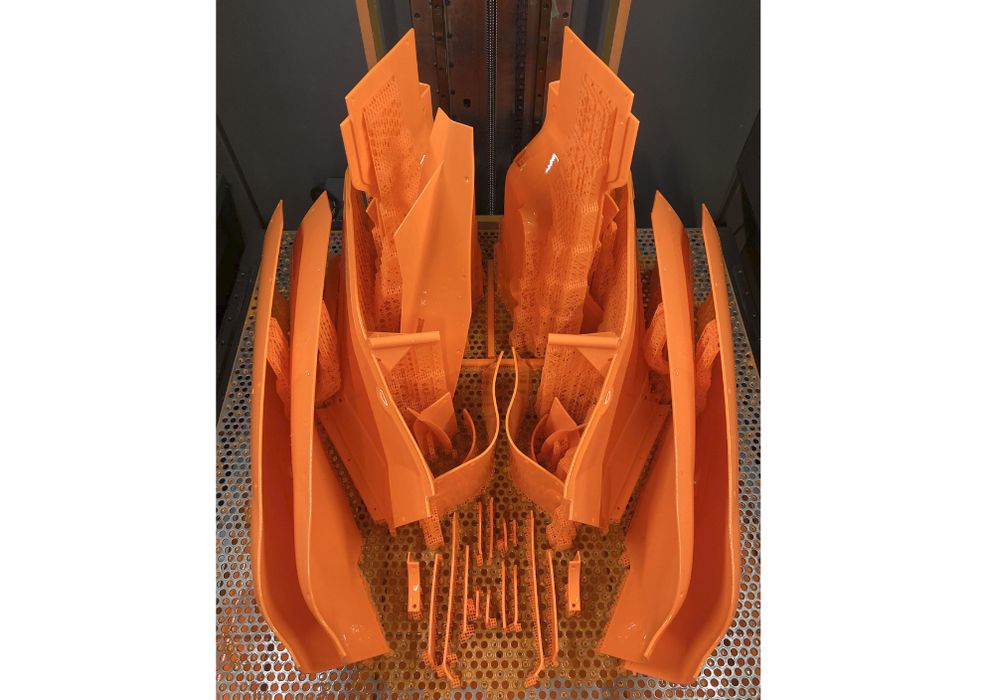
McLaren has been using Stratasys’ Neo 800 SLA 3D printer for this purpose, with Somos PerFORM Reflect resin. Chapman explains how this works:
“We find the high-definition components from our Neo machines require minimal hand finishing, which allows much faster throughput to the wind tunnel. In addition to speed, we can now produce wind tunnel parts with supreme accuracy, detail and surface finish, which has enabled our team to enhance testing and find innovative new ideas to improve performance. I cannot overstate how important these benefits are in Formula One, with super tight deadlines to deliver cars to the next race, and where the smallest design iteration can make all the difference between winning, losing or making up positions on the grid.”
It seems that AM is now so deeply used in this industry that a team could not properly participate without it.
When will this happen for other industries?
Via Stratasys