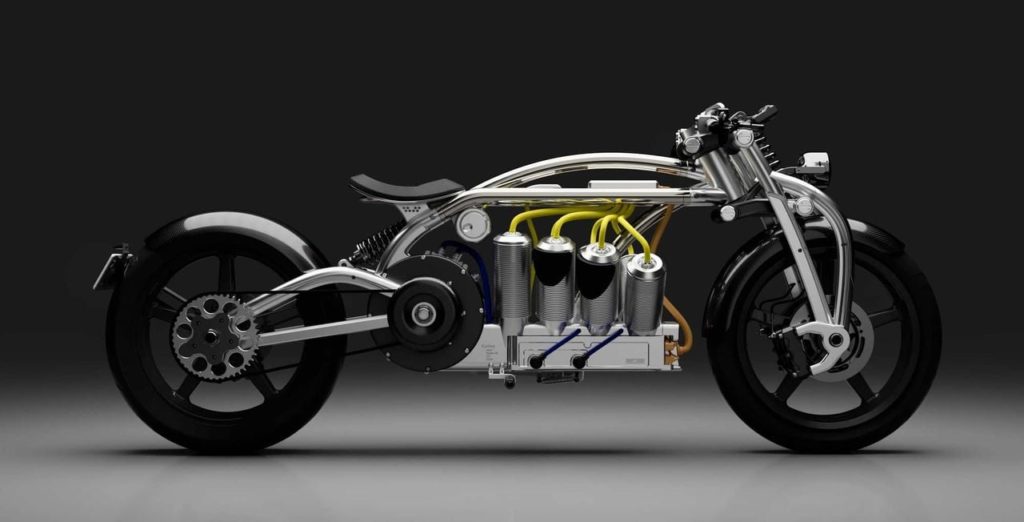
Automotive manufacturers have been turning to new technologies to ramp up growth in recent years.
Major automotive players have explored additive manufacturing (AM) business models to create design iterations and enhance cost-effective prototyping. The use of AM in the quest for product innovation through customization isn’t only of interest to traditional automakers and OEMs. Manufacturers of luxury and electronic vehicles are also leveraging the technology.
Although various materials can be used in AM, the most common are sophisticated combinations of high-performance polymers, carbon-fiber-reinforced thermoplastics and metals such as aluminum. Advances in these materials and technology have made it possible to manufacture automotive parts using additive technology.
AM makes customization and personalization easier, and can achieve part geometries—including consolidated parts—that couldn’t be made any other way. AM is also a valuable tool in the product development process. Because additive methods don’t require any tooling, completely functional prototypes can be made in as little as a day or two, speeding up time lines and allowing for more iteration.
AM has applications in low-volume production and on-demand manufacturing. Customers can order on-demand parts in small quantities as they are needed, rather than having to meet high minimum order quantities and then pay to warehouse excess supply, which is especially beneficial for spare parts and products at the end of life. Instead of stocking spare parts for obsolete products, companies can print replacement parts as needed with little to no overhead.
Cloud computing is another technological paradigm that has disrupted traditional manufacturing. In essence, this service-oriented business model allows manufacturing capabilities and resources to be share online on a cloud platform. Cloud manufacturing is growing in popularity because it can encompass the whole product life cycle, from design to production to testing and maintenance. It empowers manufacturers through data, streamlining operations, making them more cost- and energy-efficient and, ultimately, more productive and sustainable.
Fast Radius is a digital manufacturing partner that offers cloud manufacturing services from design to on-demand manufacturing at scale. It offers HP Multi Jet Fusion (MJF), Carbon Digital Light Synthesis (DLS), Fused Deposition Modeling (FDM) from Stratasys, and Stereolithography (SLA) from Formlabs.
Fast Radius Co-Founder and Chief Manufacturing Officer John Nanry explains the company’s strategy.
“We deploy a microfactory strategy or ‘factory in a box,’ which is designed to be copy and pasted for scale. These are small carbon footprint, low capital expenditure (CapEx) factories, placed in strategic locations to make parts closer to the end user. Our microfactories are integrated with our Cloud Manufacturing Platform to provide full transparency into how components are designed, produced, and delivered locally.”
Fast Radius has established a detailed physical and digital architecture along with the ability to identify and control variables that drive reliability and repeatability, allowing for microfactories to be scaled across the globe.
Nodes are deployed to expand capacity in existing locations and new geographics–some proximate to delivery partners, enabling supply chain sustainability via more localized production.
An examination of three of Fast Radius’ recent projects provides insight into the future of cloud manufacturing and AM in the automotive industry.
Read more at ENGINEERING.com