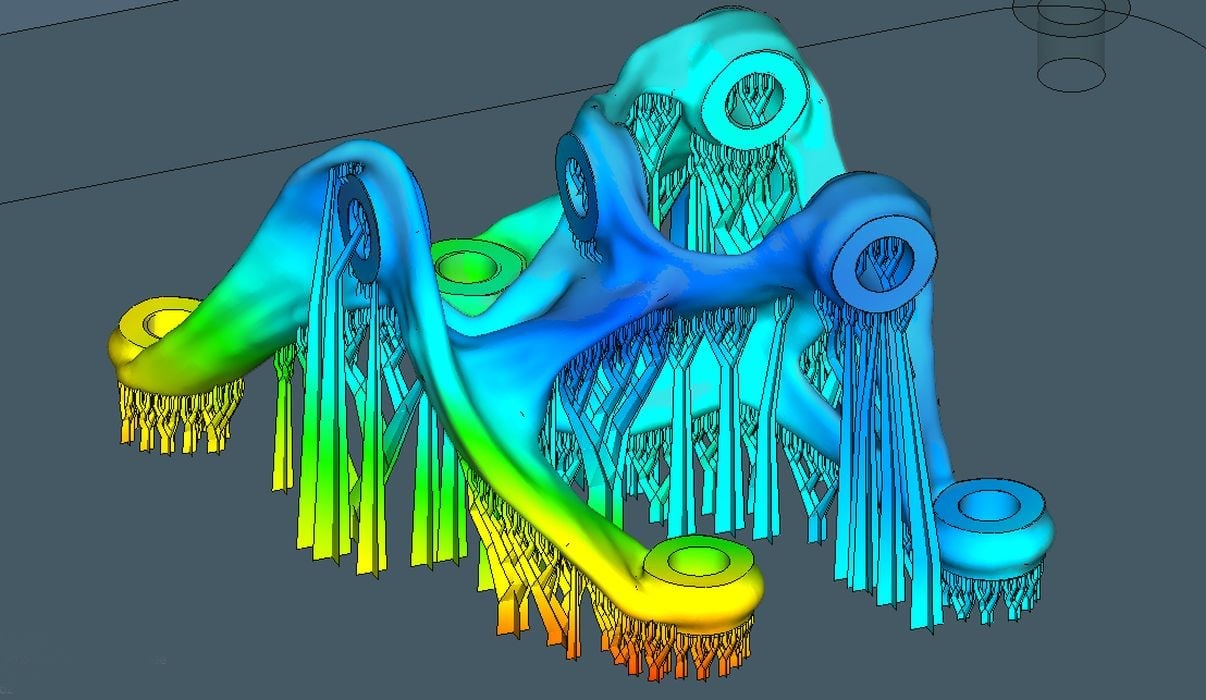
Hexagon released an interesting new platform that may be of interest to companies using additive manufacturing.
If you’re not familiar with Hexagon, they are an unusual company that produces “digital reality” solutions. This is an advanced form of the “digital twin” concept, where a digitized representation of a physical system can provide a centralized point of true information about the system.
The company’s cloud-based solution accumulates real-time data from a wide variety of sensors to power their digital realities. These realities can then undergo analysis for optimization and further automation that might not have been possible otherwise. In fact, Hexagon’s goal seems to be autonomy: automation without human supervision.
Their Nexus platform has just been made available to manufacturers, and it provides far more than just digital twin capabilities.
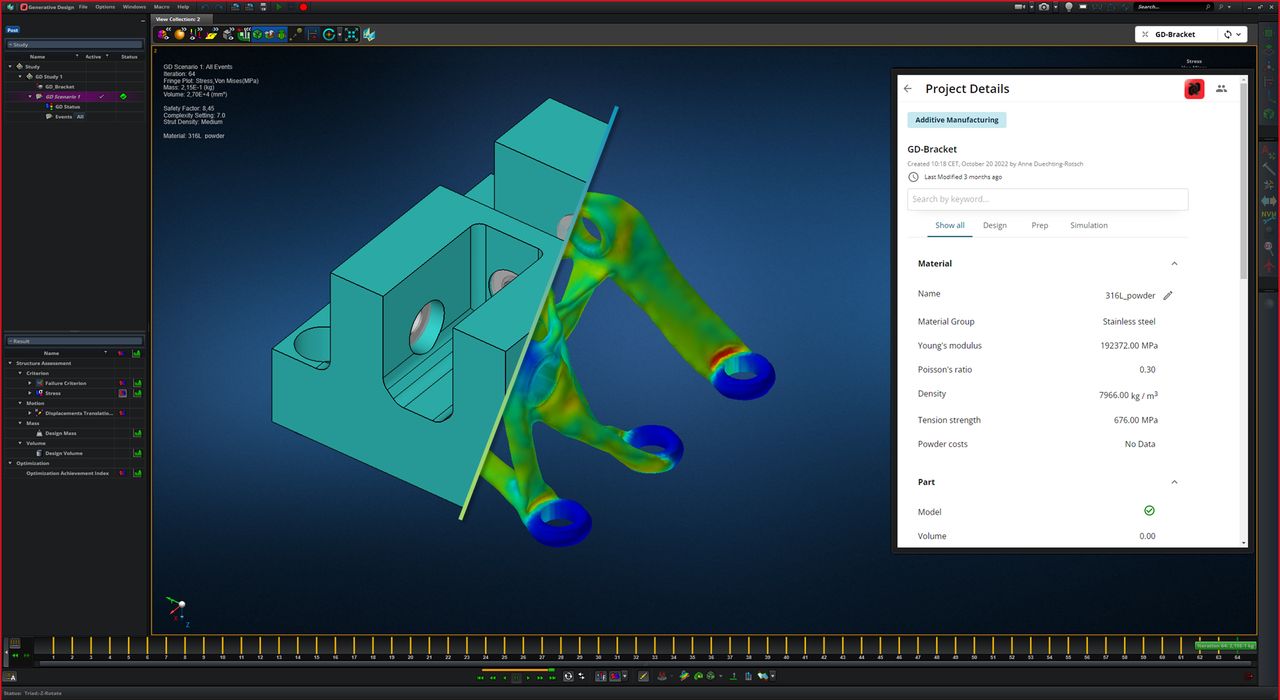
The initial form of this release includes four Nexus applications. Hexagon explains each:
Metrology Reporting, a Nexus App: The app connects Hexagon and third-party metrology data sources in Nexus’ secure cloud environment so that companies of all sizes can immediately report on previously untapped quality control data from their equipment to spot trends and identify tolerance issues. Any user can generate interactive three-dimensional CAD-based reports and insightful trend plots, KPIs and compliance documentation and up-to-the-minute data with colleagues, customers or suppliers.
Materials Connect, a Nexus App: An all-new, cloud-based library for material data, that empowers manufacturers or material suppliers to manage material data, physical test data and behaviour models for use in product Computer Aided Engineering (CAE) workflows.
Materials Enrich, a Nexus App: A first-of-its-kind Enrich app, it uses the Nexus platform’s machine learning capabilities and cloud-accelerated material behaviour simulations to help users find and simulate optimal materials that may have never been made or measured, improving the performance and sustainability of their products.
Design for Additive Manufacturing (DfAM), a Nexus Solution: A pre-configured Solution that makes it easier and more efficient for teams to jointly develop an optimal metal 3D-printed part and prepare it for a successful print using the laser powder bed fusion (PBF) process. Customers can use the Nexus web interface to connect Hexagon’s MSC Apex Generative Design and Simufact Additive process simulation software with AM Studio from CADS Additive and Materials Connect via the cloud, and easily manage user access to projects.
The last application above, DfAM, is of most interest to us. The new Hexagon system will allow multiple parties work on the same 3D model through the cloud. This should short-circuit the common silos of expertise throughout a product development lifecycle.
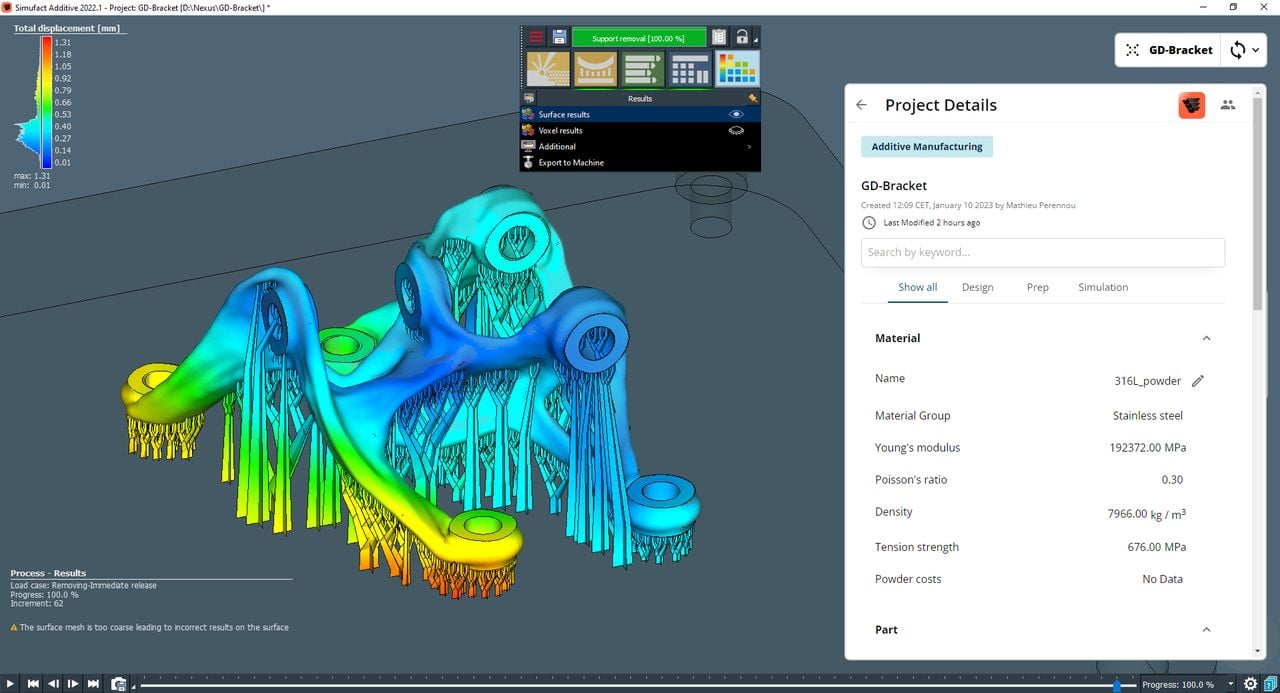
Participants are able to discuss the design as it evolves, and at the same time employ powerful tools for adapting or generating new design forms.
There’s more to the story. Hexagon has partnered with 3D Systems’ Oqton to enable the newly created designs to freely flow through that company’s Manufacturing Execution System (MES), right to production.
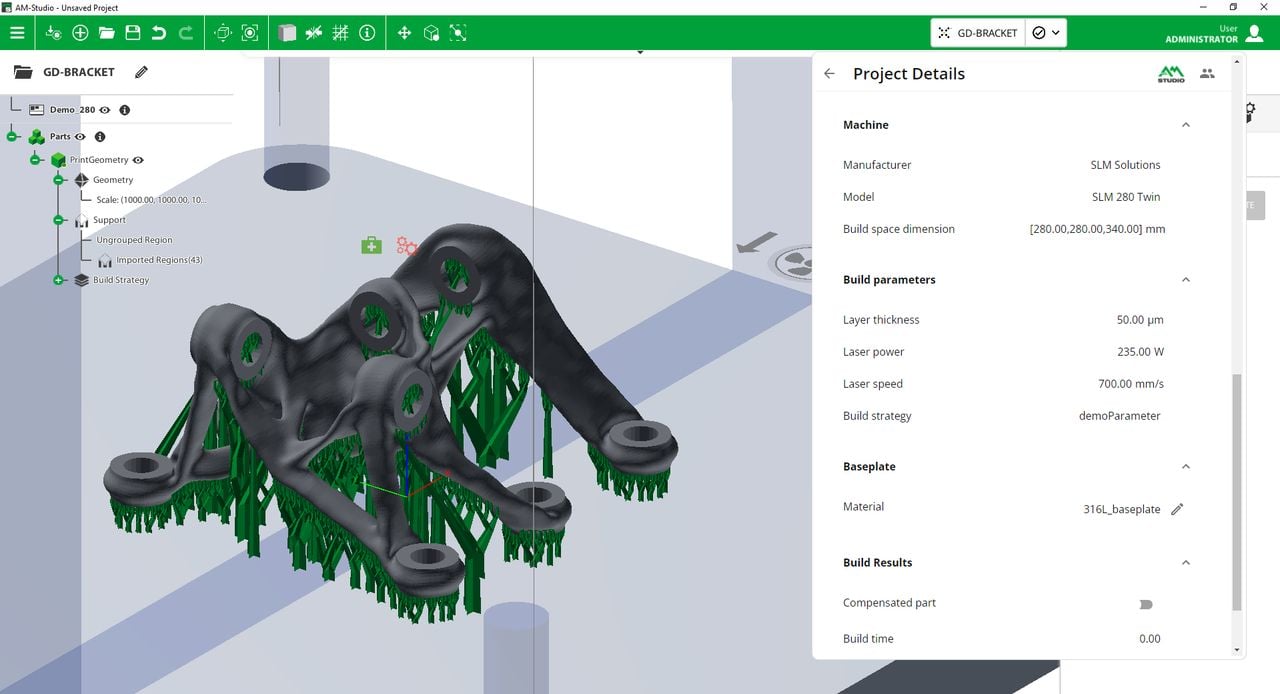
Hexagon has also partnered with Altium for electronics design handling.
This is an interesting development and fits into the class of solutions that is attempting to bridge the gaps in product development and manufacturing. Hexagon’s solution may end up being more powerful than some competitors due to its modular nature: just add new function as required.
Via Hexagon