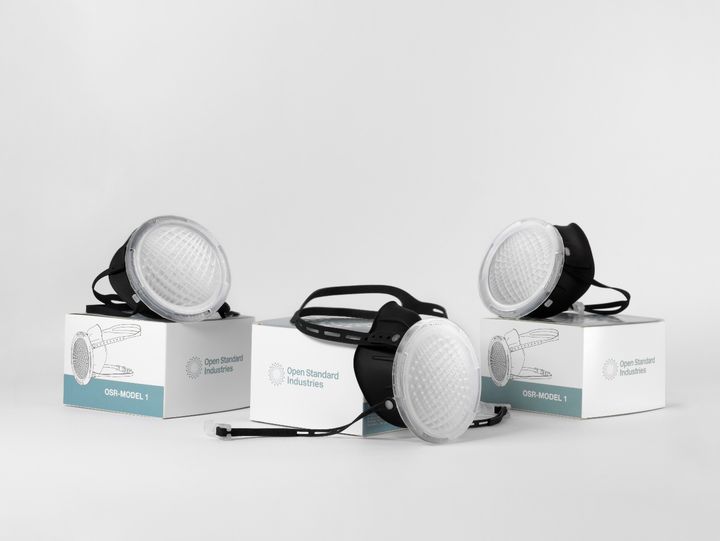
Last year, COVID-19 caused many of us to take a step back, but for some it was a chance to take a step forward.
Matt Carney, a recent PhD graduate from the MIT Media Lab’s Biomechatronics Group, was building a company that was trying to make bionic legs more accessible.
When he went into lockdown, Carney found himself looking for ways that he could use his engineering knowledge to help.“I found myself on the ‘Helpful Engineering’ Slack channel, which was basically an instantaneously generated, open hardware, global hackathon,” explained Carney. “The entire world was suddenly staying at home and, rather than read the scary news, around 13,000 people on that Slack channel began working ourselves into a frenzy.“
Face shields looked too easy, ventilators looked really hard and dangerous, but masks seemed solvable. At the same time, I was concerned about the safety of all the 3D-printed designs, and before I knew it, I was co-leading a team of strangers who were hell-bent on fixing masks.”
One of the main problems that Carney and his colleagues identified was traditional supply chains, which were unable to scale up production quickly enough to meet the surge in demand at the beginning of the pandemic.Subsequently, distributed production methods such as additive manufacturing were utilized to supply front-line medical workers with personal protective equipment (PPE) like face masks and shields.
However, Carney says that additive manufacturing technologies lacked a widespread level of material, production quality and sophistication, which limited the safety, repeatability and scalability for manufacturing N95 filtering facepiece respirators.
One of the main problems that Carney and his colleagues identified was traditional supply chains, which were unable to scale up production quickly enough to meet the surge in demand at the beginning of the pandemic.Subsequently, distributed production methods such as additive manufacturing were utilized to supply front-line medical workers with personal protective equipment (PPE) like face masks and shields. However, Carney says that additive manufacturing technologies lacked a widespread level of material, production quality and sophistication, which limited the safety, repeatability and scalability for manufacturing N95 filtering facepiece respirators.
Read more at ENGINEERING.com