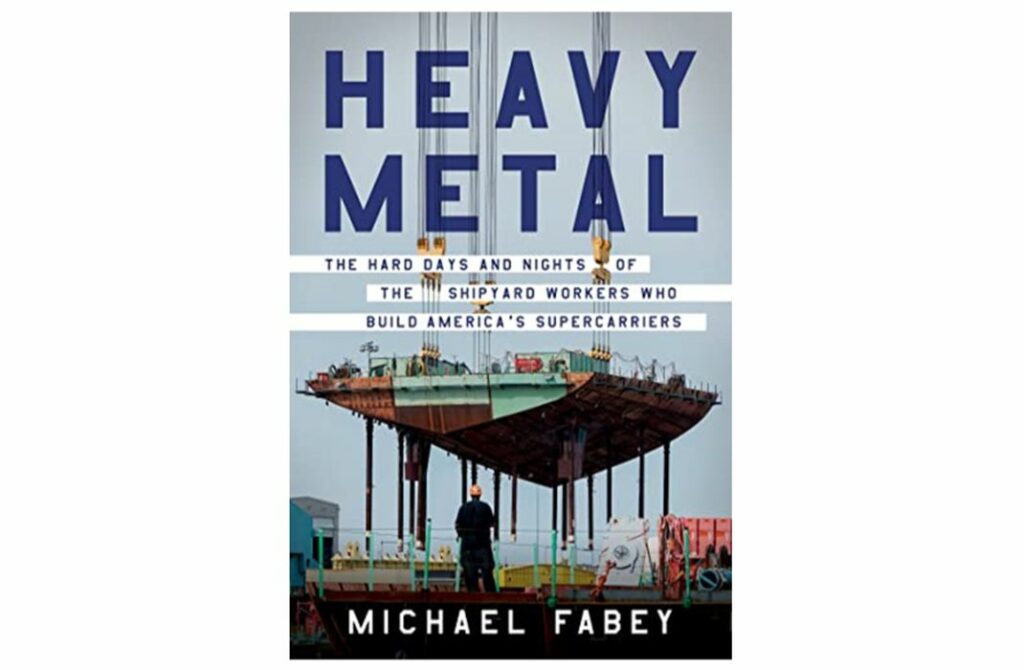
Charles R. Goulding reviews a new book on shipbuilding, where 3D printing can take a lead role.
Author Michael Fabey has a new book out called “Heavy Metal: The Hard Days and Nights of the Shipyard Works Who Build America’s Supercarriers,” describing what it’s been like to build aircraft carriers at Ingersoll’s Newport Shipyard in Virginia.
Instead of the typical business-informed senior management perspective, this book covers generations of family shipbuilding workers who do the back-breaking welding, pipe fitting, painting, lifting and other shipbuilding tasks in a challenging close-quarter environment. Fabey focuses on the construction of the 100,000-ton John F. Kennedy, which arguably uses the most sophisticated technology in the history of shipbuilding.
Technological challenges include issues with aircraft launching and landing systems, weapons and elevator systems. Lifting technology is also impressive and was needed to move and install the huge multi-ton fabricated subsections.
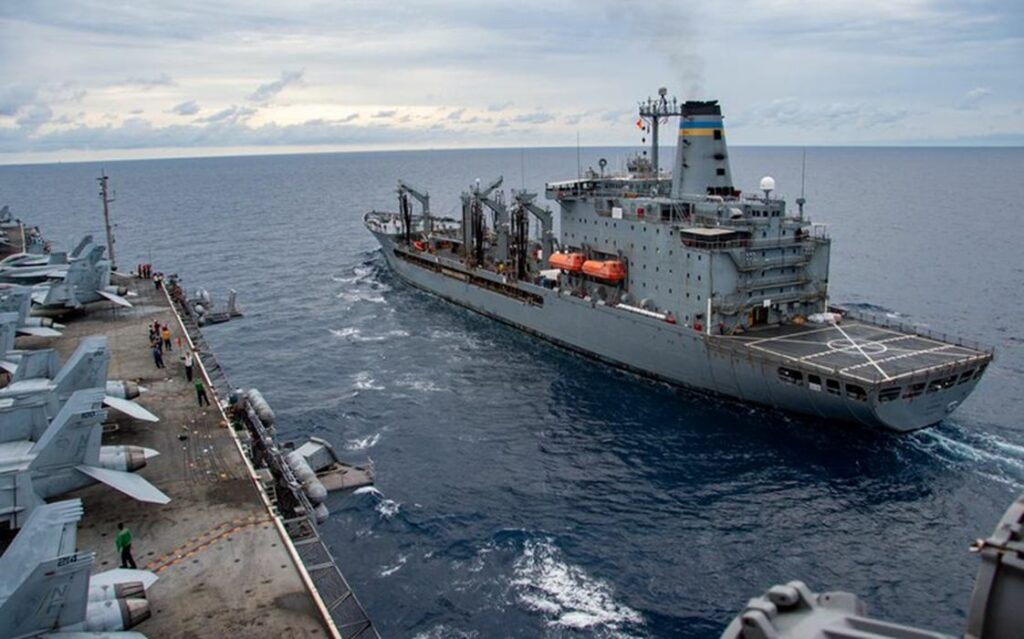
The book is written in a historical context and includes racial mistreatment that occurred in previous periods. The book’s release is timely as the aircraft carrier USS Ronald Reagan is now cruising in Asia in an effort to keep China’s expanding naval program in check.
In his previous work, “Crashback,” Fabey has covered in detail the crucial US/China naval competition. Fabey does a good job of explaining the pride and dedication of each family generation to build better ships more efficiently.
With regard to innovation, the Newport News Shipyard is making increasing use of 3D printing technology which is presented below.
Date | Newport News |
January 2019 | First 3D printed metal part delivered to US Navy for installation on an aircraft carrier |
March 2021 | 3D Systems collaborates with Newport Shipbuilding to help develop Copper-Nickle (CuNi) and Nickel-Copper (NiCu) alloys for powder bed fusion AM for parts traditionally cast |
February 2022 | US Navy utilizes additive manufacturing for submarine parts to help ease the demand for parts and current supply chain issues |
We have previously written articles on the Electric Boat, which is the other major US Navy shipbuilder.
The Research & Development Tax Credit
The now permanent Research and Development (R&D) Tax Credit is available for companies developing new or improved products, processes and/or software.
3D printing can help boost a company’s R&D Tax Credits. Wages for technical employees creating, testing and revising 3D printed prototypes can be included as a percentage of eligible time spent for the R&D Tax Credit. Similarly, when used as a method of improving a process, time spent integrating 3D printing hardware and software counts as an eligible activity. Lastly, when used for modeling and preproduction, the costs of filaments consumed during the development process may also be recovered.
Whether it is used for creating and testing prototypes or for final production, 3D printing is a great indicator that R&D Credit eligible activities are taking place. Companies implementing this technology at any point should consider taking advantage of R&D Tax Credits.
Conclusion
I wholeheartedly recommend this book, especially to those in the 3D printing industry as it is replete with examples where 3D printing can resolve issues and become relevant.