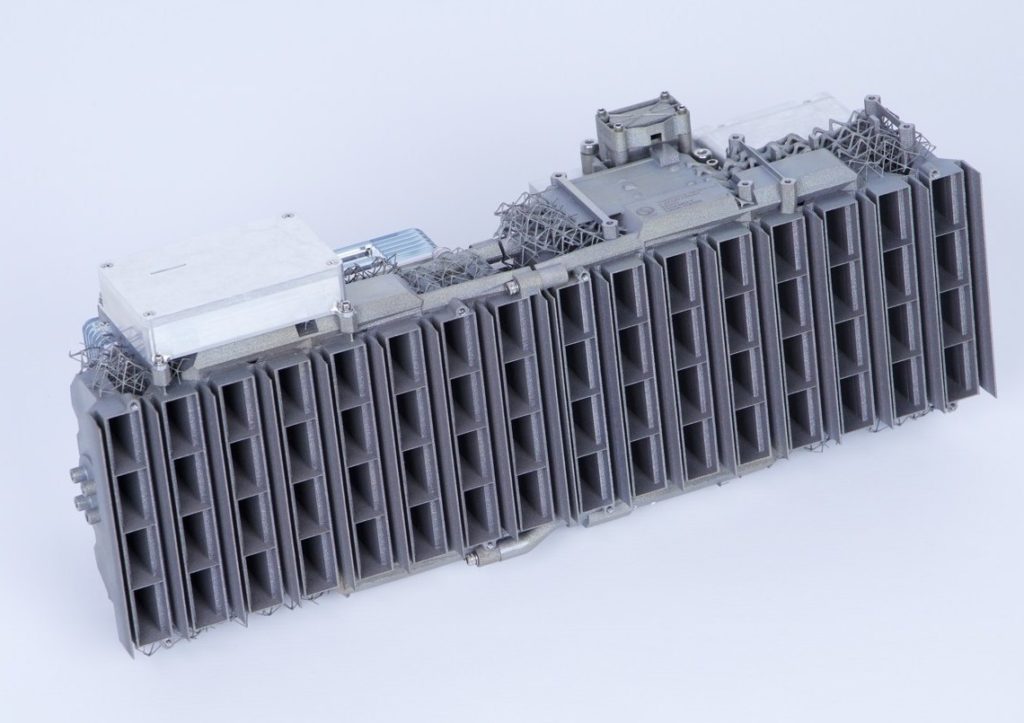
I’m seeing evidence that 3D printing has truly taken hold in advanced manufacturing, at least in some industries.
That might seem obvious to some, but for a very long time this was definitely not the case. I can still recall years ago hearing experienced engineers describing 3D printing as a “fad” that would soon evaporate.
Well, they were wrong.
The first huge challenge to widespread adoption of 3D printing was, and in some cases still is, the proper use of the technology.
The first to consider using 3D printing in their processes simply attempted to re-make their existing designs, except using 3D printing instead of their traditional making processes.
In almost every case this approach failed because 3D printing would be almost certainly more expensive than doing it the “old way”. Many business leaders dismissed 3D printing because of this “analysis” and the technology obtained an unnecessary reputation.
In fact these folks were doing it the wrong way.
The “original” parts were designed sometimes years ago with assumptions on how they would be made, and with specific materials and processes in mind. Those would, of course, be traditional processes and materials.
Taking designs made for other processes and attempting to make them using new processes was always doomed to fail.
The proper approach would be to recognize that part design and making process are actually intertwined, and that to truly use 3D printing one would have to produce different designs. These would be designs that could not easily be made using conventional making processes.
Over the years this concept has morphed into something called “DfAM”, or “Design for Additive Manufacturing”. It’s a design approach in which the older rules of thumb are thrown out the window and replaced with new ones more aligned to the current 3D technologies.
However, “DfAMing” a world full of design engineers is a huge challenge. Many, particularly older participants, were trained using traditional approaches, and some found the transformation difficult.
The more DfAM-capable designers, the better it will be for the 3D printing industry.
Over time older designers retire and are replaced with younger folks who, hopefully, have been trained in or at least exposed to modern 3D and DfAM approaches. More designers have adopted DfAM, too.
As this slowly happens in the background, how might we see this progressing? I would expect to see increasing appearances of highly complex parts producible only with 3D printing processes. When that happens we know the message is getting through and can conclude that DfAM is becoming more widespread.
There are two areas that have caught my eye in this regard lately.
One are is heat exchangers. These are devices that collect heat in industrial processes. Very often an improved heat sink can dramatically improve system performance, because heat is often a limiting factor in a system design.
3D printing allows the creation of highly complex heat exchangers that can more accurately match the specific needs of a given thermal situation. Production of said heat exchangers is about the same as other 3D prints once designed: you just hit “print” on the machine.
Typically these heat exchangers will be produced in copper material, as it is a substance that promotes very high thermal flow. I previously thought that copper could become a popular 3D print material for this reason.
The other area of interest is antennae. Like heat exchangers, antennae can be highly complex as they must be able to catch or emit electromagnetic waves of differing frequencies and powers in a wide variety of industrial and aerospace situations. Being able to produce arbitrarily complex designs and produce them is an incredible advantage.
One I’ve seen this week was provided by SLM Solutions, who produce high-end metal 3D printers. One of their clients, Optisys, has been using their devices to produce very complex RF products for aerospace, apparently including devices that are to travel to deep space. You can see one of these complex 3D prints at top.
The message here is that we have at least two application areas for 3D printing where DfAM designers have truly taken hold and are now producing revolutionary new products.
But we all know there are more.