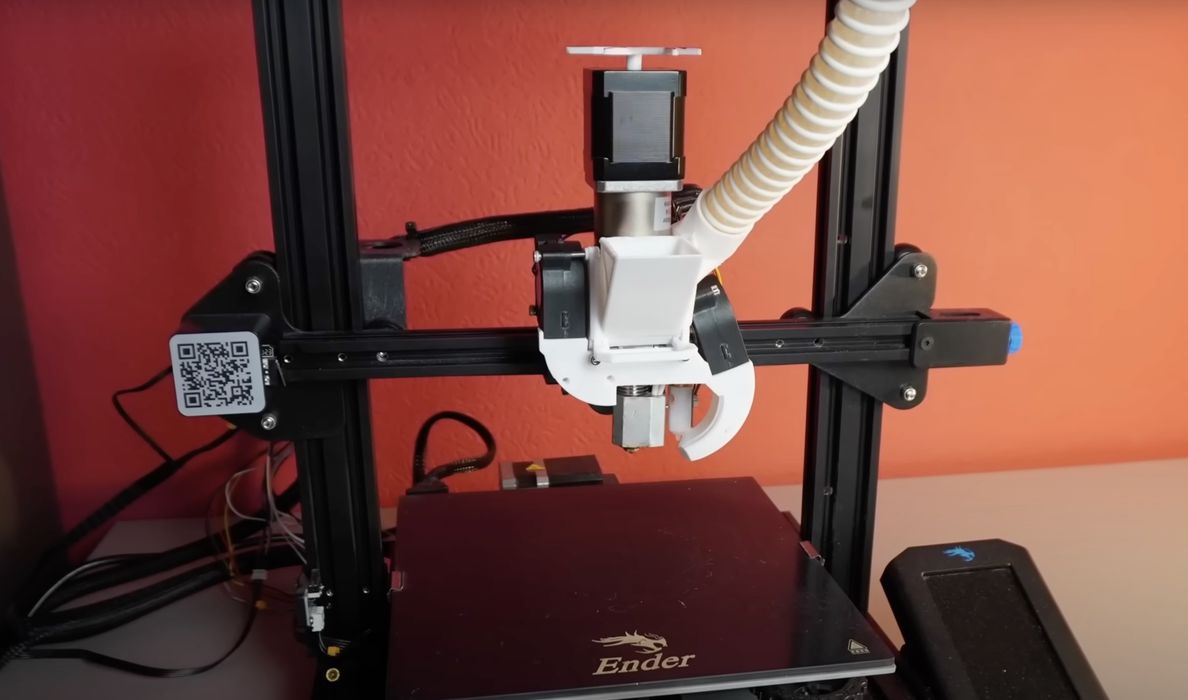
Kristian Friesen, a.k.a. “GreenBoy3D”, has provided an update on his pellet extruder project.
Friesen unleashed his radical idea earlier this month, in which he’s attempting to develop a pellet extruder. Pellet extruders are not new, but this one is different: it’s targeted at entry-level 3D printers that have never had the ability to 3D print with inexpensive pellet material.
Pellets, from which filament is made, are far less expensive than filament. Sometimes even 10X cheaper.
However, it hasn’t been possible to use pellet extruders on low-cost 3D printers because of a number of technical issues. Solving the issues adds cost and places pellet solutions out of the market for that segment.
Frisen’s design has apparently designed a pellet toolhead that overcomes these challenges and yet should carry a very low cost.
This week he provided a video update on the project, along with some interesting twists:
Friesen explains progress on the retraction issue, which pellet extruders find challenging. This is because the screw acts as a reservoir for fluid material, which simply leaks downward when stopped. The latest version includes a unique screw that is designed to vacuum up material when reversed. However, there is still the matter of material in the nozzle, which can drip out.
The question of flow rate seems to be answered, as Friesen demonstrated a very high flow rate on his prototype extrusion setup. This would suggest high speed 3D printing is possible using this pellet extruder design.
One of the issues with pellet printing is that to achieve the best possible cost you have to purchase the pellets by the pallet. That’s impractical for many desktop 3D printers operators, limiting the potential cost benefits.
A solution to that issue could be the ability to re-use waste 3D prints: recycling. But grinding up 3D print waste often requires a hefty shredding system that breaks down models into pellet-sized chunks.
Here Friesen demonstrated that it is possible to use a standard kitchen blender to chop up 3D models into smaller pieces. These were then sifted through size filter to obtain particles of suitable size for the pellet extruder. He was even able to successfully 3D print objects using this recycled material.
If that process was refined, it could provide a considerable advantage to those using the pellet extruder: there would be ZERO cost for material.
Of course, the resulting prints won’t be as perfect when compared to prints using high quality filament. However, that’s not the goal of Friesen’s project, where he’s attempting to lower the cost of 3D printing while maintaining “just good enough” print quality. That would be quite suitable for many 3D print applications.
Another issue with pellets is that they generally don’t come in a wide variety of colors. Typically they arrive from the factory in “natural” state and require coloring. Filament manufacturers do this by mixing in a “masterbatch” of color powder during filament production.
Could something like this be done using the DIY pellet extruder? It turns out yes, it can be done. In the video Friesen demonstrates several methods of coloring pellets, but one seemed to be the best approach.
That approach was to spray the pellets with a transparent coating, and then while wet mix in the masterbatch color powders. This mixture was then shaken up in a 3D printed jar, and the result was seemingly uniform color on each pellet.
These are all experiments at this point, but it seems that Friesen is on to something big here, if all these jigsaw pieces can be sewn together into a complete system. I’m looking forward to future updates — and eventual adoption of pellets extrusion and use of recycled material.
If you’re interested in this project, by all means provide some input on Friesen’s online survey, and consider joining the Discord.
Via Greenboy3D and Discord