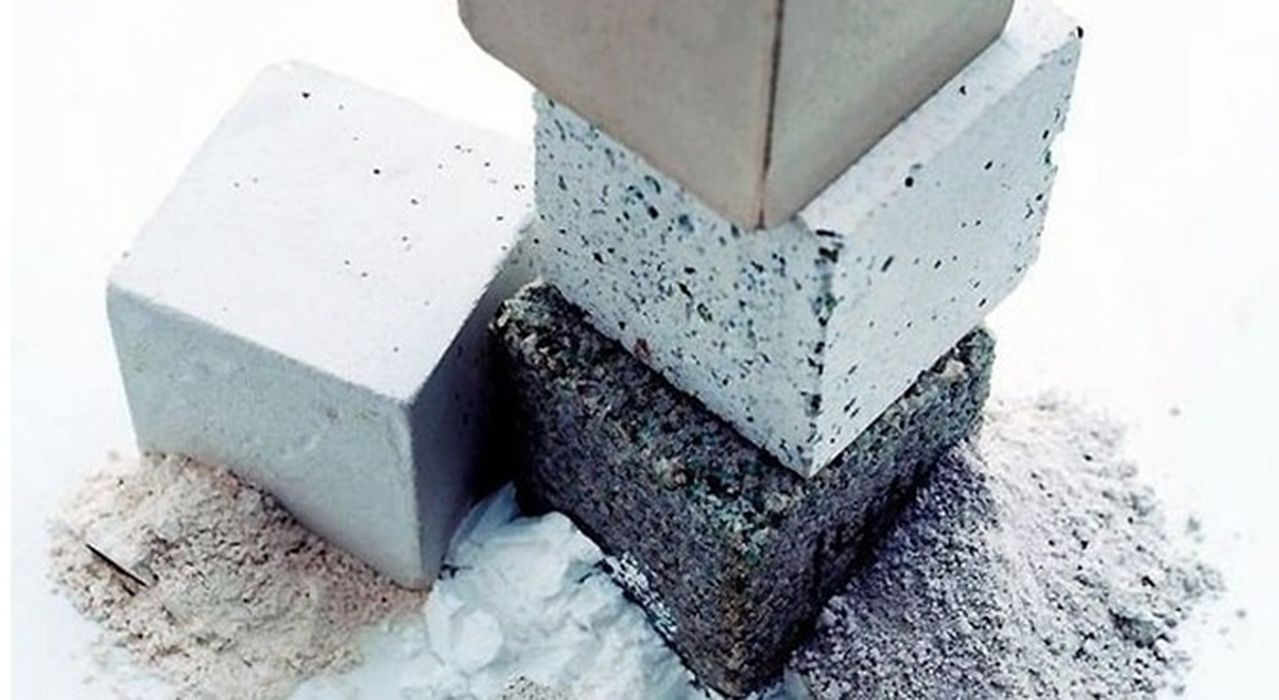
Charles R. Goulding and Preeti Sulibhavi discuss companies adopting green concrete and collaborations with 3D printing technologies.
Construction results in new homes, commercial buildings and infrastructure, but the environmental impact of the process is often overlooked
Concrete’s impact on the environment begins when limestone is blasted in quarries to make cement. Then limestone is transported to a cement plant, where the fuels used by the plant and machinery emit carbon dioxide. The limestone, or calcium carbonate, releases CO2 when it is heated to make the cement. Forty percent of CO2 emissions from the cement plant come from the combustion process and sixty percent of CO2 emissions come from the calcination process. Needless to say, the impact on the environment is quite substantial.
Now, there is a solution to reduce carbon dioxide emissions that the construction industry is known for. Cement that is mixed with wastes like power plant byproducts, recycled concrete, fly ash, glass waste, red mud, burnt clay, combustor ash or foundry sand ensures a sustainable structure of concrete that has low carbon dioxide emissions, wastewater and conserves energy is considered “green” concrete. While it is slightly more expensive to mix than traditional cement, green concrete offers substantial cost savings in the future.
In producing green concrete, liquid carbon dioxide is sprayed inside the mixing drums on concrete trucks. This is where it reacts with calcium ions in the cement to form calcium carbonate, a mineral embedded in the construction material. It is the “rock-like” calcium carbonate that reduces the amount of cement actually required for construction thereby cutting emissions by at least 5 percent and locking away the rest of the CO2 emissions into the structure that would otherwise have been emitted.
It is important to note that structures constructed with green concrete have less useful life than those made with conventional concrete and the cost of reinforcement slightly increases as well with green concrete.
A November 3, 2023, article in the Wall Street Journal (WSJ), titled “Green” Concrete Offers Hope on Climate, highlighted this construction trend.
The article highlighted companies such as CarbonCure Technologies, Vulcan and Heidelberg Materials, which are doing amazing things to drastically reduce the industry’s carbon footprint with help from green concrete.
Eco Material Technologies
In Round Top, Texas, there is a residential development known as the Caistas @ Halles that features five 3D printed houses. The cement used was “green” and the houses are therefore eco-friendly and made from a near-zero carbon cement mixture.
Danny Gray, P.E., the executive vice president for business operations and strategy at Eco Material Technologies has stated that, “this sustainable construction material, known as PozzoCEM Vite, completely replaces the use of traditional portland cement, dramatically reducing the product’s carbon footprint.” Eco Material, based in Utah, manufactures the PCV green cement product, which generates about 90% fewer emissions than traditional, portland cement during its production while setting much faster during application — in just minutes rather than the 4-6 hours for portland cement.
Eco Material worked with Houston-based Hive3D, a leading automated construction company, to customize its low-carbon material to print the five, single-story structures at The Casitas.
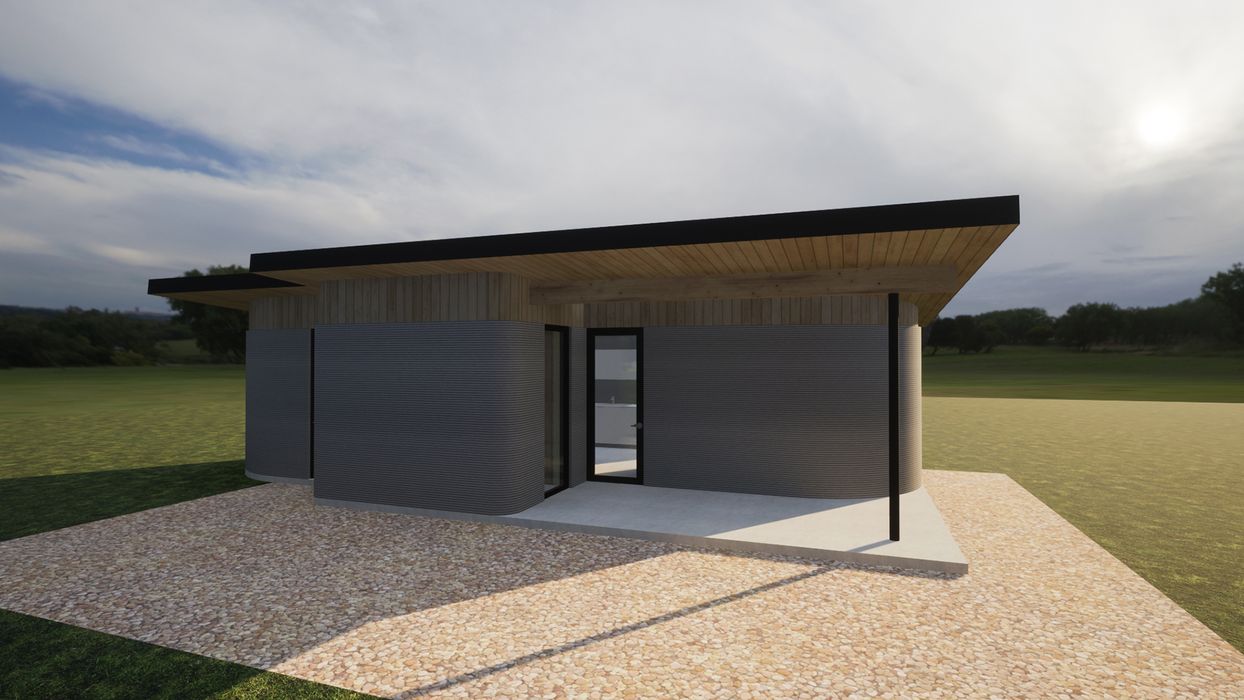
HeidelbergCement’s Subsidiary – Italcementi
HeidlebergCement has been optimizing green concrete formulation to meet the needs of 3D printers chosen for their construction projects to guarantee sustainability and more efficient construction (printing is quicker than traditional construction methods). It began in 2018 when Heidelberg’s Italcementi entered the 3D HOUSING 05 project at Milan Design Week to design and prototype a 100 square-meter house that was 3D printed on-site by a robot that used green concrete.
Holcim
Beginning in 2019, Holcim has been collaborating with COBOD to advance its proprietary ink, “TectorPrint,” which is designed for 3D printer use. Holcim and COBOD have successfully collaborated on a range of innovative building projects, from 3D printed windmill tower bases with GE, to the world’s first 3D printed school in Malawi, as well as Africa’s largest 3D printed affordable housing project in Kenya.
Holcim President, Edelio Bermejo, Head of Global R&D is quoted as saying, “At Holcim we are continuously expanding our range of building solutions to build better with less, working to improve living standards for all in a sustainable way. 3D concrete printing will help us meet these goals. In close collaboration with COBOD, we look forward to expanding our TectorPrint range of proprietary 3D printing ink.”
The range of collaborative 3D printing cement projects highlights the compatibility of using green concrete for such projects as it will save time, cost and reduce carbon emissions.
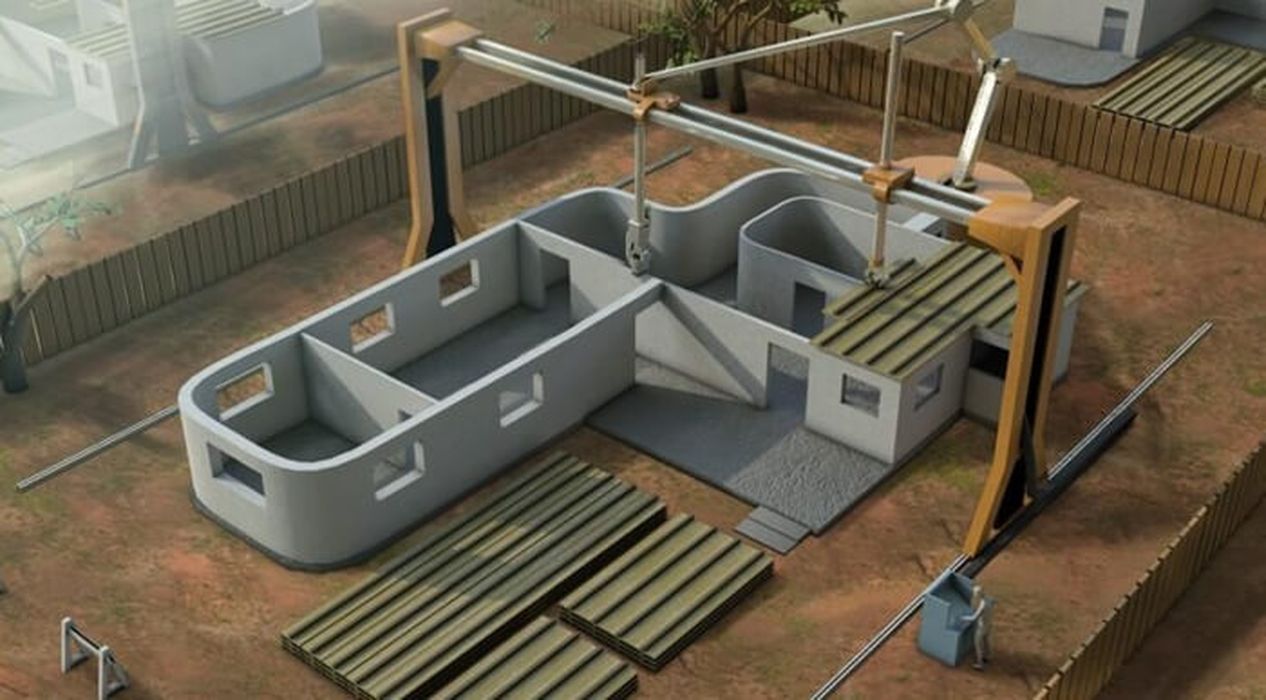
Vulcan
To date, ICON’s Vulcan construction system has 3D printed several housing communities in Mexico and Texas. The homes are stronger, longer-lasting than those built with traditional materials such as wood, and are constructed quicker with less waste and harmful emissions. We have covered homes built by ICON previously on Fabbaloo.
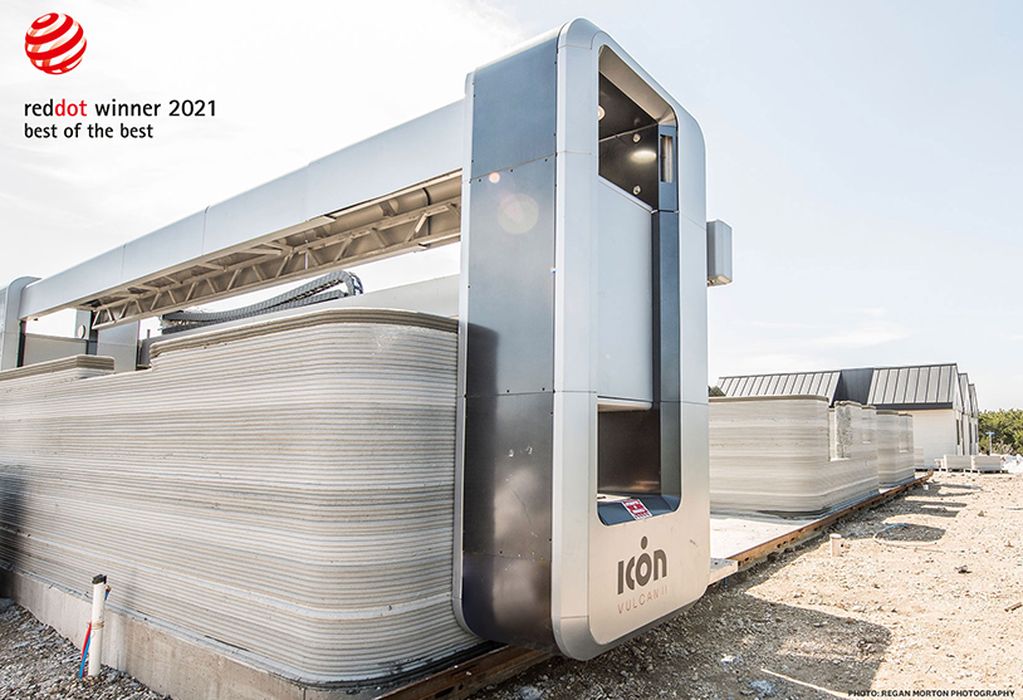
Cemex
Cemex Ventures has been advancing technologies for the construction industry and that includes 3D printing materials like cement.
Cemex has expanded its partnership with COBOD to develop a family of proprietary admixtures called D.fab, which allows conventional concrete to be efficiently customized for 3D printing construction. Cemex is working with COBOD to reduce the carbon footprint of its 3D printing construction projects by working on materials and mix preparation. Cemex is working on investments in the decarbonization space, especially for carbon capture, utilization, storage, alternative fuels, and hydrogen-related solutions.
The Research & Development Tax Credit
The now permanent Research and Development (R&D) Tax Credit is available for companies developing new or improved products, processes and/or software.
3D printing can help boost a company’s R&D Tax Credits. Wages for technical employees creating, testing and revising 3D printed prototypes can be included as a percentage of eligible time spent for the R&D Tax Credit. Similarly, when used as a method of improving a process, time spent integrating 3D printing hardware and software counts as an eligible activity. Lastly, when used for modeling and preproduction, the costs of filaments consumed during the development process may also be recovered.
Whether it is used for creating and testing prototypes or for final production, 3D printing is a great indicator that R&D Credit eligible activities are taking place. Companies implementing this technology at any point should consider taking advantage of R&D Tax Credits.
No Time to Waste…
The construction industry is notorious for its massive carbon footprint. With green concrete, the opportunity to reverse this is available. The 3D printing industry can go green and integrate green cement into the design of cement 3D printers.