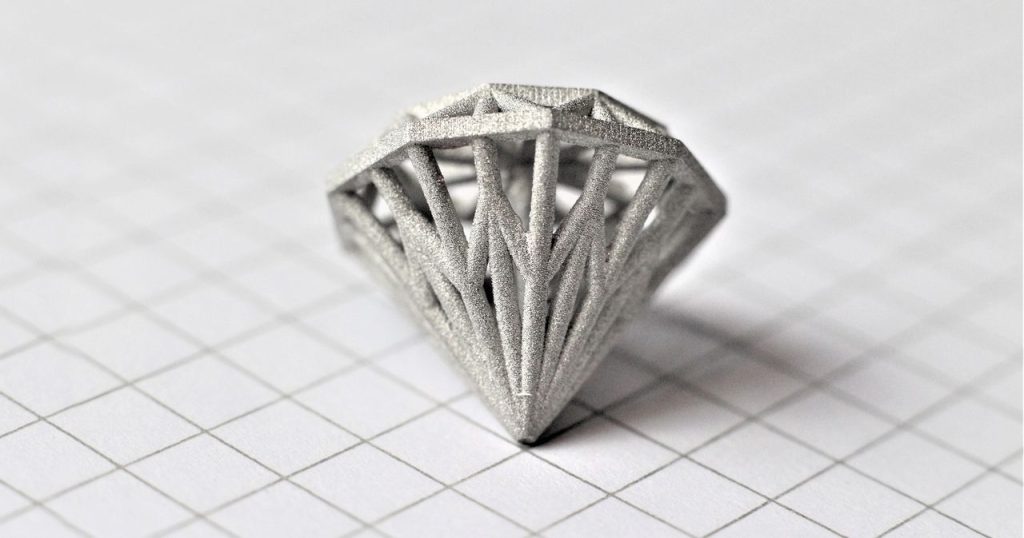
MetShape is a different kind of 3D print service.
Most of the 3D print services we encounter are pretty general. They use equipment from the major 3D printer manufacturers, and associated materials. Mechanical parts are routinely produced.
Many of these service bureaus have expanded in recent years to add a variety of different making services, such as sheet metal processing, injection molding and CNC milling. They did so because it turns out many clients need multiple technologies to complete their application, and why leave those customers for someone else?
So we have a large number of making services that more or less mostly offer the same type of services.
This might hit the majority of the market, but what about unusual needs.
Last week I was looking for an obscure type of 3D print technology among the usual service suspects, and in fact did not find any major service that met the needs of that particular job.
In such situations, the obvious route is to contact the manufacturer of the unusual 3D printing process and ask for help in getting the part printed. Many will often just run the job for you on their equipment, for a fee. However, there is little consulting done in this type of relationship as compared to a proper service bureau that can provide custom advice and expertise when required.
But there’s a gap between that and the commonly available 3D print services. Unusual 3D print technology is not often found in service bureaus.
Here’s an exception: MetShape.
The German startup company offers metal 3D print services, but with a difference. They are able to produce 3D prints of exceptional quality and extremely fine resolution, in stainless steel 316L, stainless steel 17-4PH, and titanium Ti6Al4V.
They are able to produce very thin walls, and the surface quality is so good that you often don’t require much post processing.
While the maximum part size is only 70 x 45 x 100 mm, that’s sufficient for many small and complex metal parts. The layer size is 0.035mm, and up to 250 layers can be printed per hour.
Where are they getting all this capability from? It turns out they’ve adopted the LMM technology from Incus, which we explored in 2021.
LMM, or Lithography-based Metal Manufacturing, is an optical process involving metal-infused resin being selectively cured using UV light. The system operates top down, as opposed to many SLA and MSLA systems, as the resin is quite thick with up to 60% weight being metal particles.
LMM is a multi-step process. After printing the part must be cleaned, and then have the polymer binder removed, followed by high temperature sintering to finalize the part. LMM is able to produce parts of exceptional dimensional accuracy.
That’s what MetShape is using behind the scenes, and it’s pretty unique for a 3D print service, and proves that there are services to do what you need, if you look hard enough.
If you’re shopping for small and complex metal parts with exceptional accuracy, MetShape could be a consideration, along with their US-based sales representatives from Qualified3D.
Via MetShape and Qualified3D