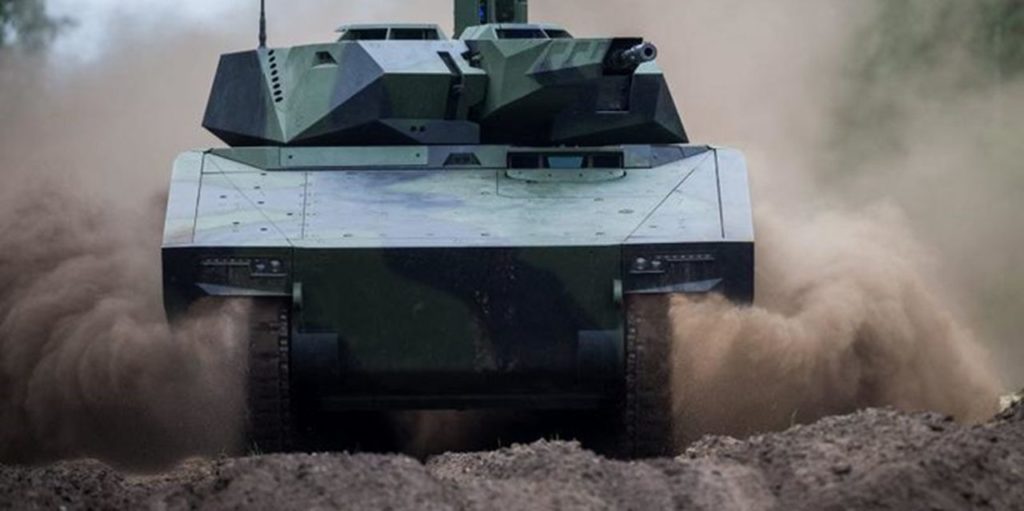
Charles R. Goulding & Ryan Donley examine the recent change in defense strategy in Germany.
German Chancellor Olaf Scholz’s sudden decision to inject 100 billion euros into Germany’s defense industry surprised the world. This funding, which is designed to both provide aid for Ukraine and defend Germany, is a historic shift from German policy against conflict involvement. The Chancellor’s announcement included promises of fighter aircraft and drone improvements.
Rheinmetall, Germany’s largest defense company, stands to benefit from the influx of defense spending. Germany has several defense companies in its ranks, including Thyssenkrupp for submarines and Hensoldt for sensors.
Rheinmetall, Thyssenkrupp, and Hensoldt are also large investors in 3D printing technology and have long been leveraging 3D printing to develop new products as well as improve upon existing products. Rheinmetall as Germany’s largest defense corporation has considerably invested in research and development, spending over 400 million USD alone in 2021 with a significant portion attributed to their 3D printing operations across their business units.
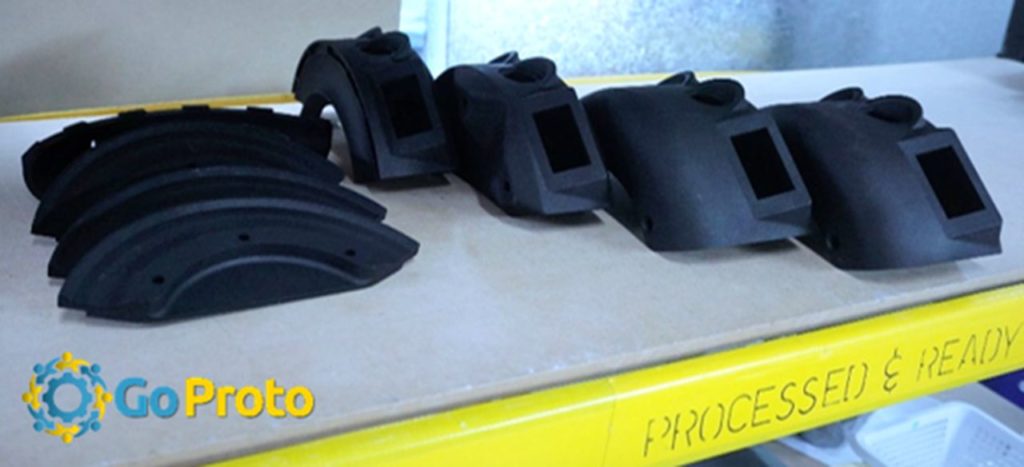
Rheinmetall has several divisions leveraging 3D printing technology with a focus on SLM and Multi-Jet Fusion technology. The company’s extensive capabilities in additive manufacturing have recently expanded into military applications; In a partnership with GoProto, Rheinmetall was to deliver 3D printed components, including handles and communication panels, for the Lynx vehicle.
Rheinmetall continues to exploit the full capabilities of additive manufacturing and has incubated several 3D printing startups under its umbrella to continually increase development, especially in military and vehicle applications. Solidteq is one of the companies that emerged from Rheinmetall and has been applying 3D printing for rapid prototyping up to the production of small series of components. Continually leveraging 3D printing has led Rheinmetall to believe they can soon consider additive manufacturing as an alternative (or complementary) to traditional manufacturing.
The Research & Development Tax Credit
The now permanent Research and Development (R&D) Tax Credit is available for companies developing new or improved products, processes and/or software. Eligible costs include U.S.-based employee wages, cost of supplies consumed in the R&D process, cost of pre-production testing, contract research expenses, and certain costs associated with developing a patent. As of 2016, eligible startup businesses can use the R&D Tax Credit against $250,000 per year in payroll taxes.
3D printing can help boost a company’s R&D Tax Credits. Wages for technical employees creating, testing and revising 3D printed prototypes can be included as a percentage of eligible time spent for the R&D Tax Credit. Similarly, when used as a method of improving a process, time spent integrating 3D printing hardware and software counts as an eligible activity. Lastly, when used for modeling and preproduction, the costs of filaments consumed during the development process may also be recovered.
Whether it is used for creating and testing prototypes or for final production, 3D printing is a great indicator that R&D Credit eligible activities are taking place. Companies implementing this technology at any point should consider taking advantage of R&D Tax Credits.
Conclusion
The Chancellor’s announcement opens up an entirely new business segment for German manufacturing expertise. The 3D printing industry needs to be part of this opportunity.