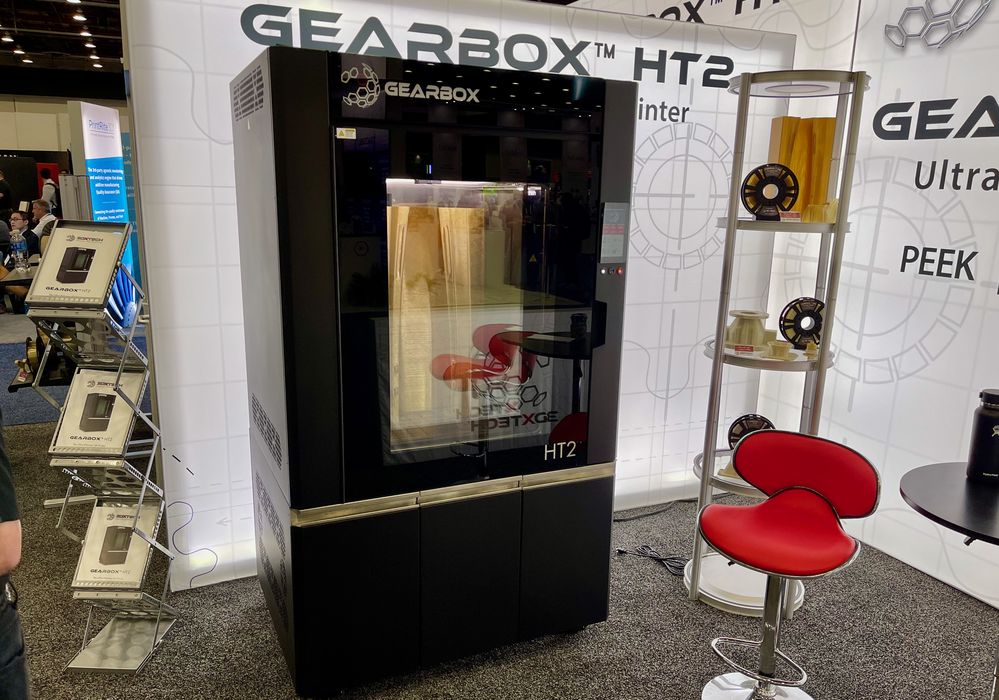
I came across a high temperature 3D printer with a big difference.
High temperature 3D printing is in great demand these days, and for good reason. The higher temperatures allow for the use of more powerful engineering materials. Not only are these materials providing additional heat resistance, but some can also provide additional chemical resistance and other useful properties.
These materials are so powerful that in some scenarios it is possible to substitute a 3D printed polymer part for a heavier metal original part, so long as the thermal stress isn’t too high. That can provide a tremendous weight advantage, and that’s where the demand comes from.
To address this demand multiple players offering high temperature 3D printers have emerged in the past few years.
One of them is 3DXTECH, based in Grand Rapids, Michigan. The company started in 2014 with folks familiar with the plastics industry after realizing there wasn’t a 3D printer on the market that properly printed engineering materials.
So they made one, which required three years to develop.
Gearbox HT2 3D Printer
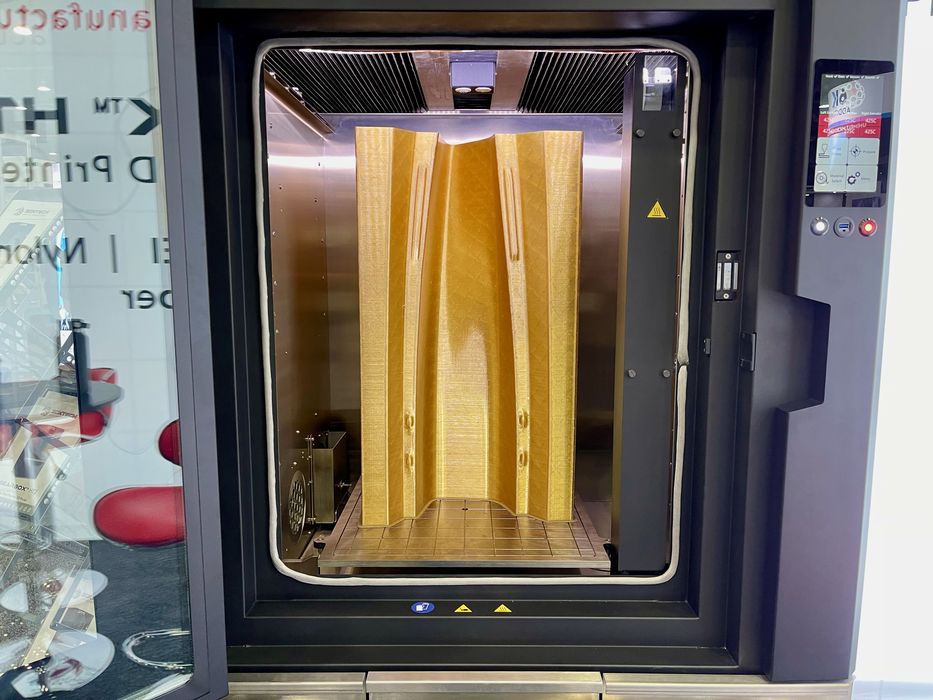
The result is today’s Gearbox HT2 3D printer, which was launched last October, and it’s quite an interesting device. For a high temperature 3D printer, it has a rather large build volume of 457 x 457 x 813 mm, perhaps the largest high temperature build chamber available today.
The HT2 includes dual extruders, allowing for the use of high temperature-compatible support material for complex geometry 3D prints. 3DXTECH offers both soluble and breakaway support options.
Filament storage is actively heated and dried, a mandatory feature for notoriously thirsty engineering materials that would quickly become corrupted if left in open air. The HT2 has a huge 16kg capacity, able to store four 4kg spools.
Gearbox High Temperature Materials
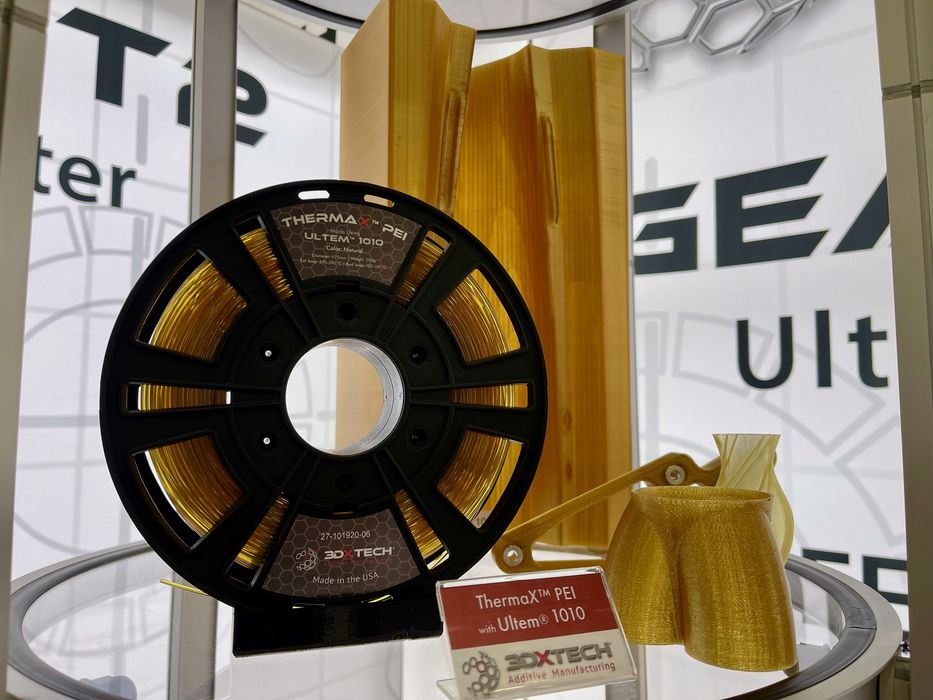
The HT2 offers a wide variety of material capability, and is indeed an open materials device. They say they’ve certified use of PEEK, PEKK, PEI/Ultem, PPA, HTN, PA12, PA6, PC, PC/ABS, PET, ASA, ABS.
The build surface is a bit unusual, as they don’t use a spring steel plate as do many 3D printers these days. Instead they use a plastic sheet that’s held down flat via a vacuum system. The print adheres to the sheet, which is easily removed once the vacuum shuts down. This system was also used by early Fortus equipment from Stratasys.
The key features of the HT2 are the high temperature components. The hot end is able to hit a sizzling 500C, enabling printing of practically any polymer. But what’s more interesting is the chamber temperature, which can be set as high as 230C. This is perhaps the highest build chamber temperature I’ve seen, and it enables additional productivity from the machine.
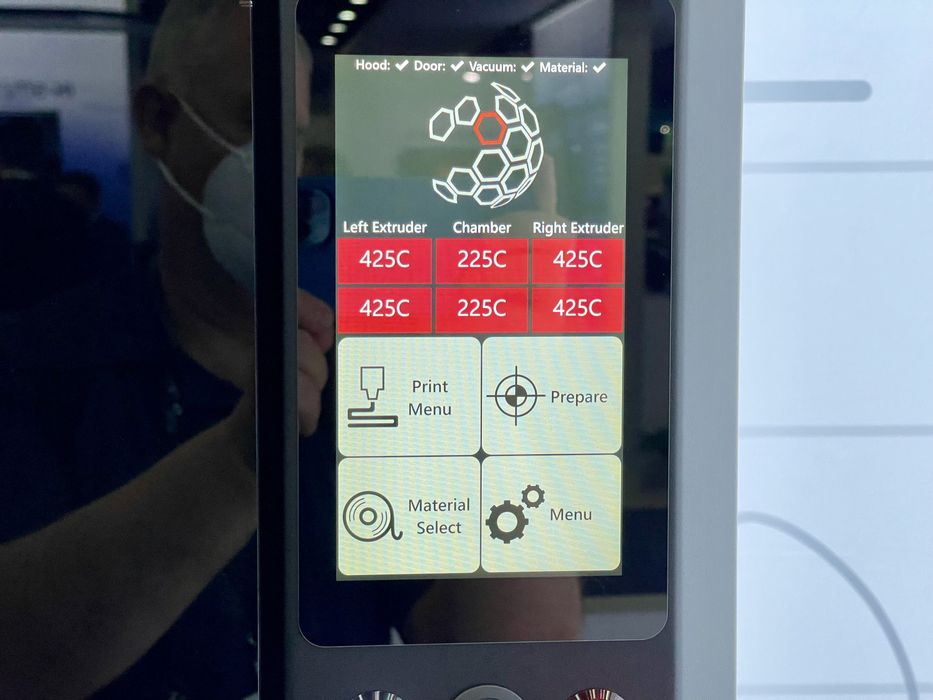
As a 3DXTECH representative explained to me, many “high temperature” 3D printers offer build chambers able to reach only 130C or so. This is a temperature insufficient to properly crystallize most high temperature polymers. The result is that for those systems a post processing step is required to anneal the prints with a heat treatment. That’s more work and slows down part production.
Meanwhile, the HT2’s operating temperatures are sufficiently high to fully crystallize materials such as PEEK. This removes a step to produce end-use high temperature parts.
This is a key feature of the Gearbox HT2, and one that should be considered by those looking to purchase a high temperature 3D printer. There’s more to the story than just having a printer, it seems.
We’re told the price of the Gearbox HT2 is approximately US$129K.
Via 3DXTECH
How much Max. job size we can do in this Gearbox HT2 3D Printer. we have 2 jobs
1. job type & size : Ring & OD:880mm, ID:660 mm
2. job type & size : Ring & OD:1900mm, ID:1500 mm
Please send me your feedback.