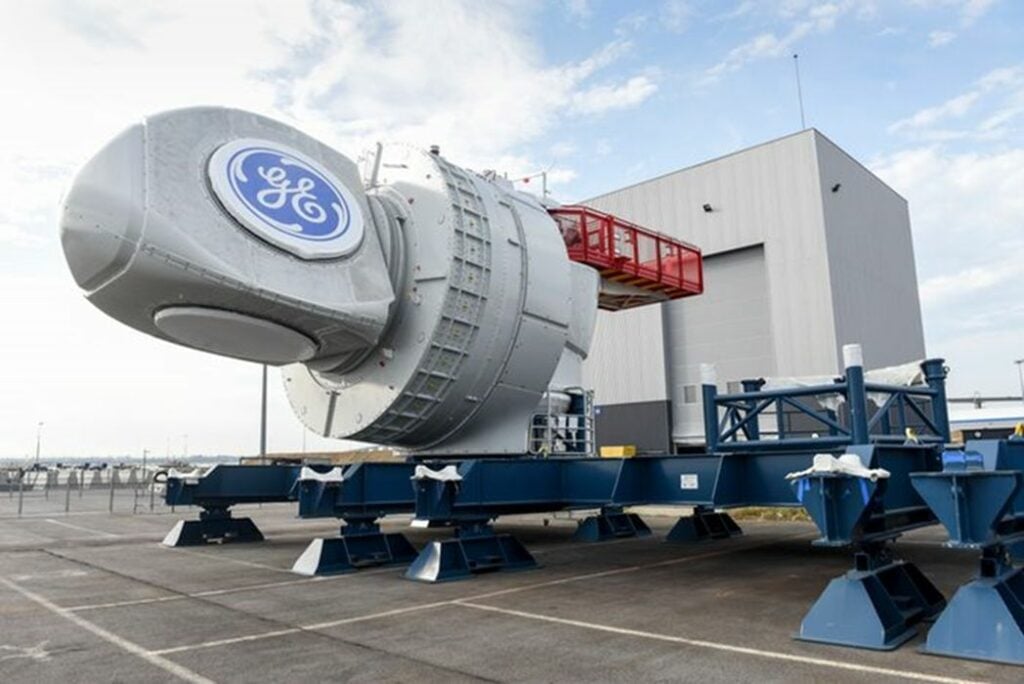
Charles R. Goulding and Preeti Sulibhavi look at how GE will handle 3D printing during its corporate restructuring.
As previously covered in 2021, breaking up is hard to do, and GE is no exception. GE is breaking into three business segments. They are GE HealthCare, GE Aerospace, and GE Vernova, for their renewable energy, power, and digital services.
GE HealthCare has realized that both patients and doctors want quick and accurate diagnoses. 3D printing is a tool that can help automate healthcare processes such as routine scanning, abnormality detection, and identification of lesions and diseases. We have covered this topic as it relates to other leaders in the industry such as Siemens Healthineers and Varian Medical.
It also helps patients understand their condition and the need for treatment in a clearer way. For instance, GE Healthcare is helping physicians use data from ultrasounds to create 3D models of patients’ hearts and other organs before and after surgery to illustrate the treatment in a more understandable and relatable manner.
GE has also built the first European 3D Printing and Design Center in Uppsala, Sweden. This is a space where engineers and manufacturers can collaborate under one roof to develop and produce parts for healthcare equipment. The center opened in October 2017 and is the home of advanced 3D printing manufacturing technology such as metal and polymer printers and co-bots as well.
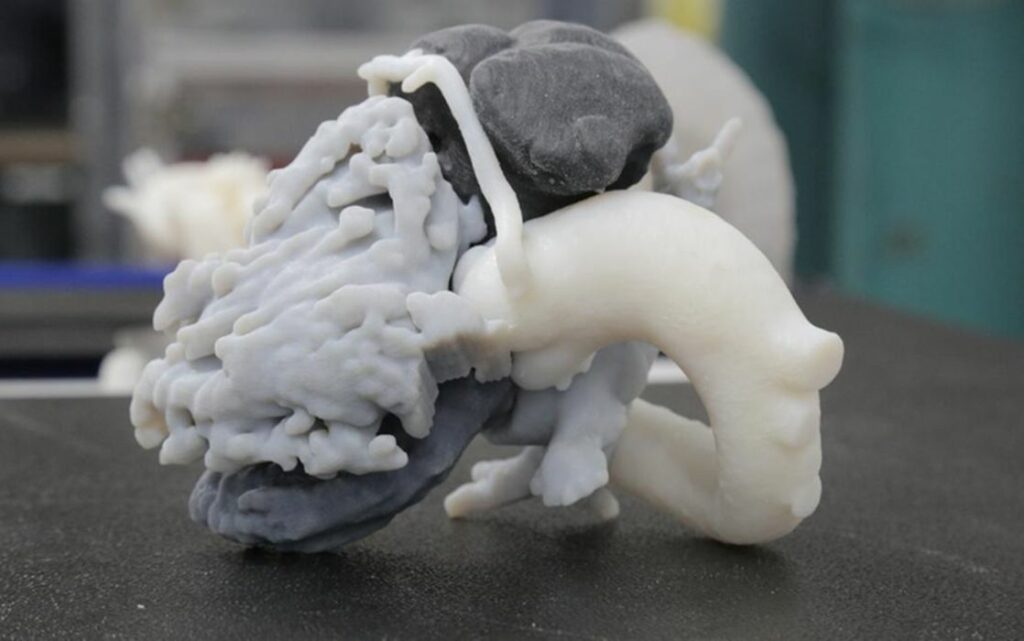
The aerospace industry has been using metal and polymer 3D printing and AM practices in recent years and making innovative strides as well. GE has been improving and developing its 3D printing capabilities. Last year, the company launched GE Additive, a business segment dedicated to supplying 3D printers, materials and engineering consulting services.
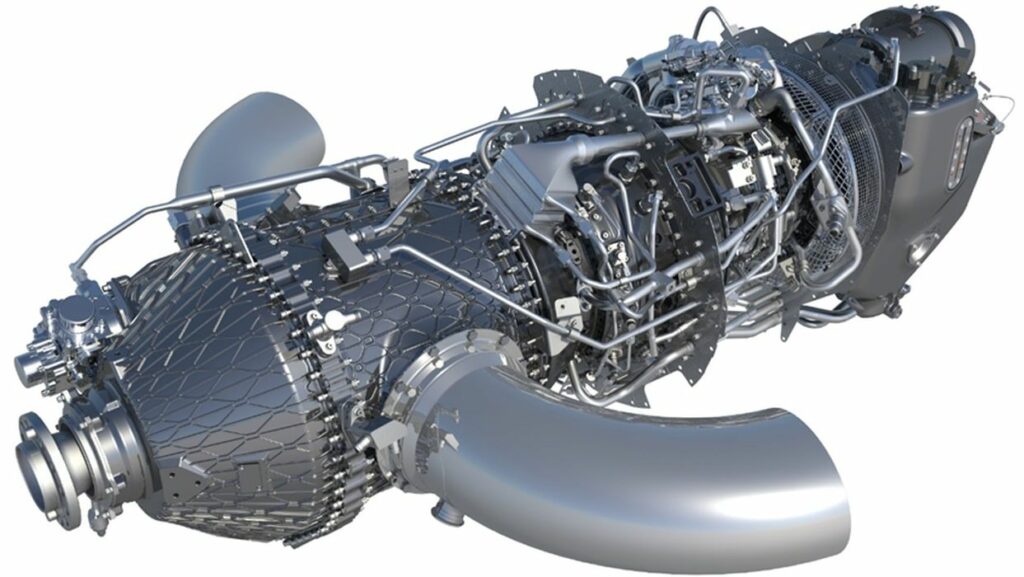
CFM Aviation, a joint venture between GE Aviation and Safran Aircraft Engines, developed and produced the LEAP engine, a complex 3D printed engine that is being used by Airbus and Boeing’s new fleet of narrow-body commercial airliners. The LEAP engine cuts fuel burn and emissions by 15 percent.
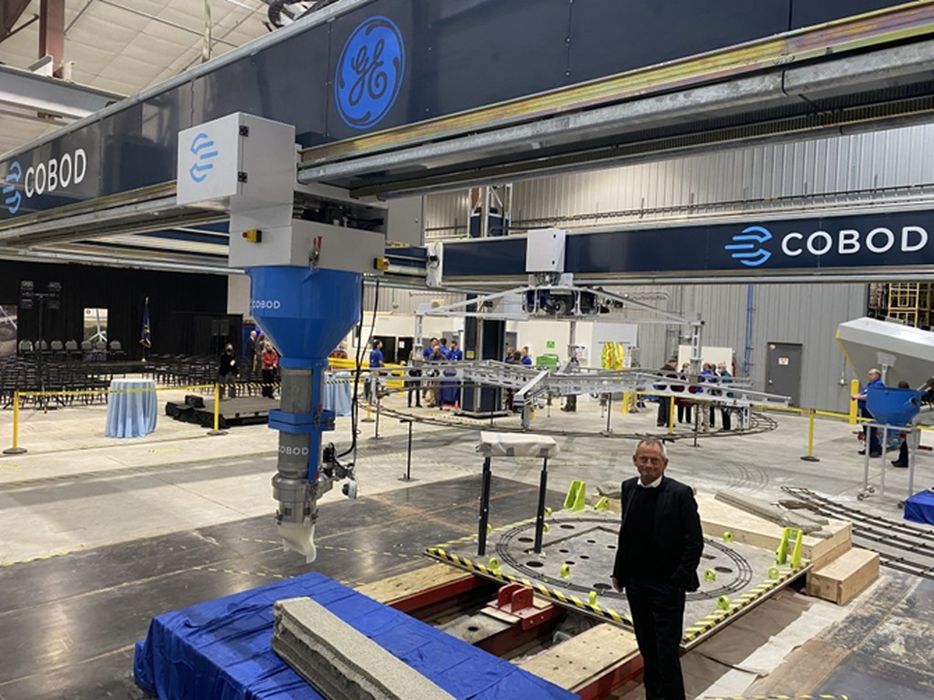
GE’s energy business is comprised of several different companies that share the same commitment to energy transition and sustainable power. Vernova, the moniker derived from “verde,” which is Spanish for green and “novus,” or new in Latin, will essentially be the umbrella company for making turbines for power plants and wind farms.
As pictured above at GE’s R&D facility, COBOD’s founder and CEO, Henrik Lund-Nielsen, stands in front of the BOD2 3D printer that is capable of 3D printing real concrete structures up to three stories tall.
The Research & Development Tax Credit
The now permanent Research and Development (R&D) Tax Credit is available for companies developing new or improved products, processes and/or software.
3D printing can help boost a company’s R&D Tax Credits. Wages for technical employees creating, testing and revising 3D printed prototypes can be included as a percentage of eligible time spent for the R&D Tax Credit. Similarly, when used as a method of improving a process, time spent integrating 3D printing hardware and software counts as an eligible activity. Lastly, when used for modeling and preproduction, the costs of filaments consumed during the development process may also be recovered.
Whether it is used for creating and testing prototypes or for final production, 3D printing is a great indicator that R&D Credit eligible activities are taking place. Companies implementing this technology at any point should consider taking advantage of R&D Tax Credits.
Conclusion
GE is divesting its business, but getting more focused at the same time. It is honing in on emerging trends and innovative technologies. All three of its new business segments are heavily invested in 3D printing.