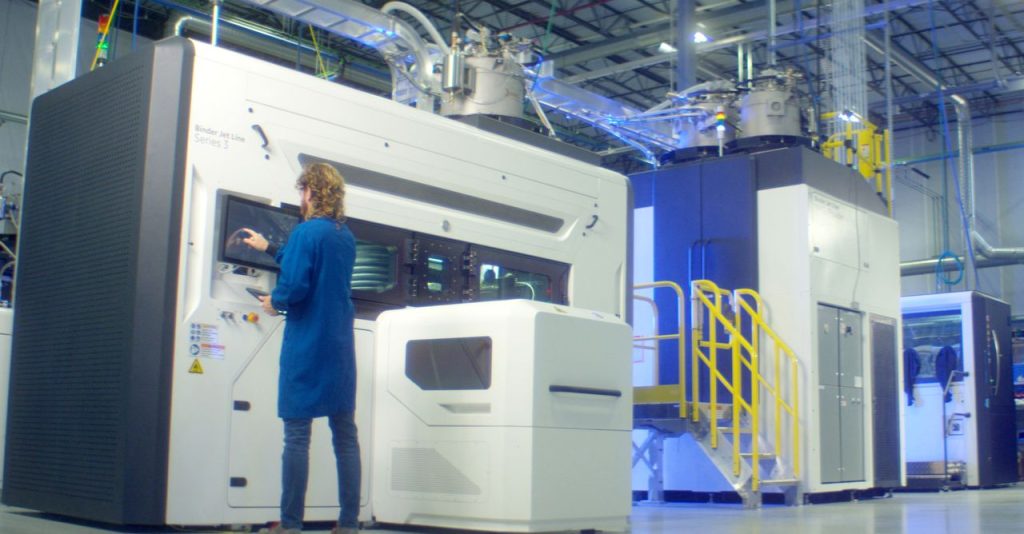
GE Additive announced the Series 3D binder jet metal 3D printer system yesterday, and it could be a revelation for manufacturers.
I was privileged to visit the GE Additive development center where the device has been secretly being built over the past five years. Unfortunately, due to legal requirements I was not permitted to take any pictures of the machine or sample parts, but they will emerge over time.
The Series 3 is not a modification of an existing system, and is an entirely new machine and accessory components. It’s all designed to seamlessly fit into metal foundry operations that up to now have been unable to financially justify the high cost of LPBF 3D printing technology.
Using a binder jet approach for 3D printing metal objects is not new, but GE Additive’s approach is different in both materials and process from other systems.
Not an Easy-Bake Oven
The Series 3 is not an “Easy Bake Oven”, a term sometimes used for standalone 3D printers that while they can 3D print, cannot easily or effectively fit into a modern manufacturing operation.
Here GE Additive has taken great steps to ensure not only that the Series 3 can be directly integrated into factory scenarios, but they’ve made it incredibly efficient and cost effective, too.
Series 3 Printing Process
The Series 3 uses a binder jet approach in which a specially designed binder is selectively dropped by inkjet nozzles on a flat bed of metal powder and applies heat as the arm passes over the bed. The powder is then recoated with a second arm that compresses the bed with a roller and pre-heats it with infrared lights.
The result is rather solid green parts embedded in a build box full of metal powder. These parts must be extracted, depowdered and sintered to finalize the part.
What is quite incredible is that the binder material developed by GE Additive creates extremely strong green parts. Sample parts tested by myself were extraordinarily difficult to break apart by hand, even when literally hammering them on a table.
These parts are incredibly dense as GE Additive uses only a very small (~1%) ratio of binder, and the compression during printing removes most of the voids. During sintering the remaining air inside the part escapes, leading to solid parts with little evidence of layering.
This means the Series 3 will be able to make rather robust green parts that would not be able to support themselves as is the case with other binder jet systems. In other words, the Series 3 should be able to produce a wide variety of geometries using an inexpensive binder jet process.
Series 3 Automation
GE Additive has spent considerable effort to ensure the Series 3 will be highly efficient and easy to implement in factory scenarios. This is done through a variety of ingenious innovations that are likely the first to be seen in the industry.
One principle used by GE Additive is safety: the Series 3 system ensures no operator is exposed to powder or materials at any point in the process, up to the removal of the parts from the depowdering station.
How is this accomplished?
Along with the usual atmospheric seals on the build chamber to avoid contamination, the build box itself is sealed — including its inert gases — after it emerges from the 3D printer and travels to post processing stations. No powder is exposed.
In addition, the powder and binder handling on the Series 3 is quite unique. Instead of filling up the hoppers on the 3D printer, these materials are distributed from secondary materials handling units via plumbing!
There is a Powder MHS and a Liquid MHS, with the liquid version handling both binder and cleaning fluid. The cleaning fluid is used to ensure the nozzles don’t gum up with repeated use of the binder. The Liquid MHS also takes up returned waste liquid (mostly cleaner contaminated with binder) for safe disposal.
The most amazing thing to me on the Series 3 was the Powder MHS. This is a central unit to which the operator rolls up drums of powder from the manufacturer. The Powder MHS then safely slurps up all the powder from the drum and maintains a central repository of powder for Series 3 machines in the factory.
How does the powder get to the machines? There are literally hoses from the Powder MHS to each Series 3, and a hefty air pump blows inert gas the flow the powder quite some distance to the printers. The powder flow was described (and seen by me) like a “sandstorm in a pipe”. GE Additive representatives said they could move around 25kg of powder per minute, which is enough to “fuel” a Series 3 printer for at least 14 hours of continuous use.
Apologies for the lack of proper images to show how this amazing system works, but again I was not permitted to take any by GE Additive. However, in the top image you can just barely make out some of the plumbing between the machine components above the equipment.
Series 3 Scaling
The Series 3 system is designed from the ground up to be scaled to very large implementations. Here’s how it works:
Centralized MHS systems can attach to multiple printers. Theoretically, a Powder MHS can supply over a dozen printers — continuously, if jobs are set up to stagger the workload across time.
GE Additive explained the entire print process is automated, except for the depowdering step. This means very little labor is required to produce vast quantities of parts.
Regarding the depowdering, GE Additive explained that it is a horrendously complex problem, and they are still working on a solution. It’s complex because of many factors, including unknown part geometry, requirement for robotics, tracking of individual parts from a build box (you may have more than one customer’s parts in a job) and the fact that each company using the Series 3 likely has a different way to post process parts.
The Series 3 build volume is 500 x 500 x 500 mm, and, as with any powder system, can be used in 3D: objects can be stack on each other within the build volume. This means you can Tetris in as many parts as will fit and get them all done within a single job.
GE Additive suggested they’ve done tests with as many as a thousand parts in a single job. Now imagine a dozen printers doing that from one central MHS. Now imagine multiple clusters of them. I think you get the idea: this concept is incredibly scalable.
Series 3D Prospects
After seeing the Series 3 working and examining some of the parts produced on the system, there is little doubt that this system could be a massive success in industry environments.
I intend on posting a followup story with the implications of this important announcement later this week.
Via GE Additive