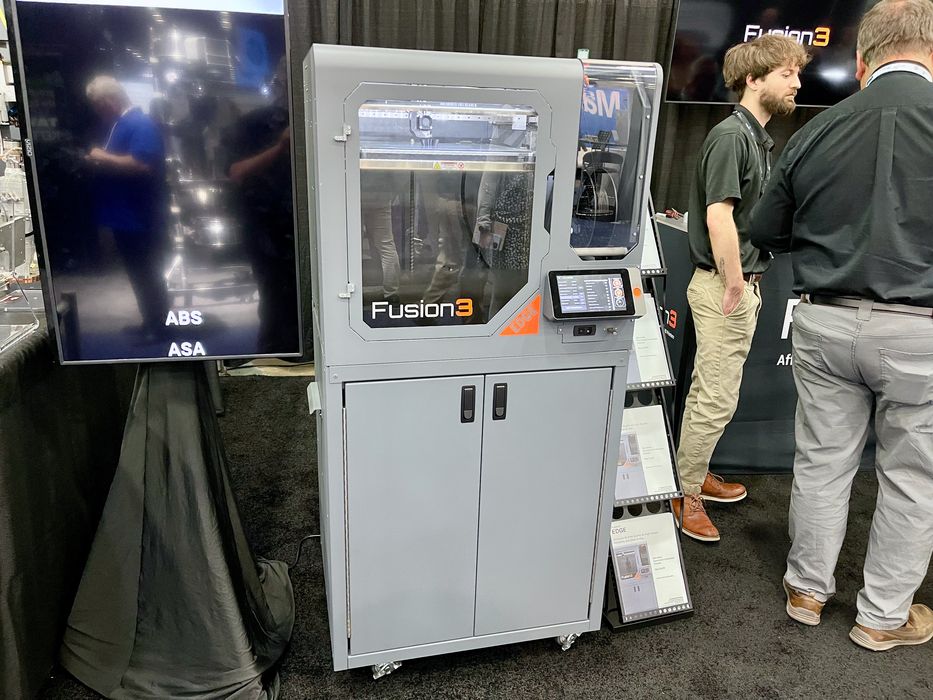
Fusion3 announced an interesting deal with ActivArmor to place equipment directly at healthcare operations.
Fusion3 is the producer of a line of very capable professional 3D printers. Their equipment, led by the flagship EDGE device these days, is capable of producing production parts at good speeds and excellent print quality. They are typically used for low volume production applications to make parts in various engineering materials.
ActivArmor is a very interesting company that’s leveraged the capabilities of 3D printing to provide highly unusual casts and splints for broken bones.
Normally casts are made from plaster, which, although perfectly fitting the patient, is heavy and prevents access to skin — a very annoying restriction if you need a scratch.
ActivArmor’s approach is to scan the patient’s limb and then use software to generate a complex sparse cast design that can be 3D printed. This provides a cast that is not only lightweight with skin access, but also looks very cool.
It’s our understanding that ActivArmor has up to now operated central printing factories for casts, often using Fusion3 equipment. We interviewed one international ActivArmor operator to understand how this works.
However, the new arrangement with Fusion3 is a bit different. It seems that ActivArmor is adding the capability for appropriately-sized healthcare operations to print-on-site with Fusion3 equipment, rather than having ActivArmor print and ship them.
Fusion3 CEO and founder Chip Royce explains:
“ActivArmor is expanding its business to include the licensing of the entire production suite (software, scanning and Fusion3 EDGE 3D printer) to hospitals, doctors’ offices and clinics. The inclusion of the Fusion3 3D printer is a great win for our company and a validation of its capabilities for the fast production of large, mission-critical medical parts out of engineering-grade materials.
From our experience as a 3D printer manufacturer, the interest in 3D printing orthotics has exploded over the past couple of years. ActivArmor is positioned to capture the demand here in the US and internationally with a great product, a well-developed ecosystem of partners, and regulatory approval.”
This is a very interesting move, because it cuts out part of the usual ActivArmor workflow and should make casts available to patients much faster than when using ActivArmor’s centralized production facility.
I suspect it may also increase the use of ActivArmor product. It’s quite possible that healthcare facilities and even patients might view the new product with a bit of suspicion, but having it “around the office” will make everyone more familiar with the concept and thus potentially increase use.
ActivArmor CEO Diana Hall said:
“Fusion3 is our supplier of choice for this game-changing project. Fracture-care patients need casts that are protective, strong, safe, and fast! We chose Fusion3 as our partner because ease-of-use, consistency, speed, and reliability are essential to the adoption of a new technology in the traditional casting space.”
ActivArmor will certain see an uptick in production because of this move, but also Fusion3 will benefit: any healthcare facility taking part will be effectively purchasing new Fusion3 3D printing equipment.
There’s a lot of healthcare facilities that make up this market, so both companies could see significant growth.
Via Fusion3 and ActivArmor