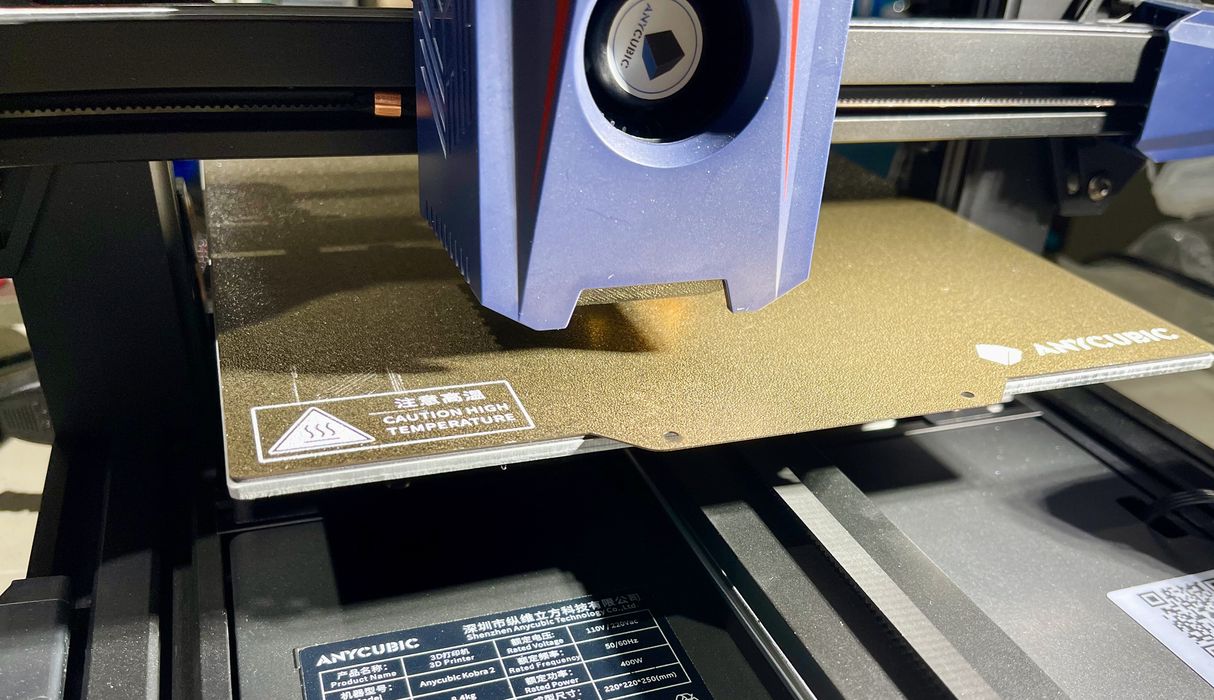
SPONSORED CONTENT
I had some further thoughts on Anycubic’s latest FFF 3D printer, the Kobra 2.
While Anycubic has produced dozens of open-gantry desktop FFF 3D printers over the years, this one is very different. That might seem surprising, given that it visually appears quite similar to all the previous models: it has a base, a print plate, gantry and toolhead.
But it’s under the hood where the real changes appear, and they’re not entirely obvious to the eye.
Why is this important? It’s because the Kobra 2 is one of the first of a new wave of upcoming high speed desktop 3D printers that will almost certainly take over the market. A year from now I expect that no one will want to be a “standard speed” 3D printer — one that prints between 30-80mm/s.
In this case, “high speed” means 150mm/s and above.
There have been a number of machines recently emerge that can successfully 3D print at that rate, and it’s really not easy at all to do so.
For many years enthusiasts have attempted to squeeze more speed out of their desktop FFF devices, starting by simply increasing the print speed in the slicing software. Sure, that makes the machine run faster, but it can be at the cost of quality — or even print success.
There are two main issues: vibration and flow rate.
The Vibration Problem
As the machine runs faster, the toolhead has more momentum to overcome when directional changes occur. Imagine the typical movement of a 3D printer filling a flat layer by moving quickly back and forth. Now, in your mind, speed that up by three times. Or six times.
The scene could be reminiscent of those videos where a washing machine “goes crazy” if its payload is not even. Vibrations eventually cause the washer to break apart, and the same might happen with a 3D printer that attempts to move faster.
One approach for dealing with vibration is to make the mechanical aspects of the 3D printer more robust, and that seems to be what Anycubic has done with the Kobra 2. It has a much strengthened motion system.
In particular, the Z-axis has two threaded rods instead of just one, and they are quite a bit thicker than those used on other Anycubic models.
The rods are also secured at the top and tied together with a belt for synchronous movement. This also leads to significant strengthening of the frame itself as there are four vertical elements: two rods, two extrusions, instead of just two extrusions.
The motion system itself has been upgraded significantly. The X and Y axes now each use a metal double axle core and more advanced SG 15 bearings. These metal wheels are able to provide smoother motion during the very rapid movements of this speedy 3D printer, in addition to lasting significantly longer than the plastic D-shape wheels on other models.
The Flow Problem
The second issue is flow rate. If you print faster you must certainly move the printhead at a higher speed. But you must also be able to supply softened thermoplastic through the nozzle at a higher speed.
This is also a difficult challenge because it requires a way to somehow heat plastic at a faster rate because it is in the nozzle for a shorter period of time: it’s moving faster.
Anycubic solution involves a higher-power heating element in the Kobra 2, which is now rated at 60W. This means that as the cool filament passes by, the heat remains constant rather than cooling down. Think of the filament as “blowing air to cool” the hot end. If you “blow” too much, you’ll cool it down.
Another issue is the grip on the filament. To print at higher speeds, the extruder gears grabbing the filament must be better designed: standard methods risk shaving filament rather than pushing it; the gear becomes a saw! On the Kobra 2, Anycubic has redesigned the direct drive extruder to incorporate dual gears, which can grip the filament on both sides. This dramatically increases the grip on the filament.
Does this work? Indeed it does. I tested the flow rate of the Kobra 2 and found the following:
As you can see, the flow rate tends to drop off as the speed increases so long as the hot end temperature is sufficient. You can see that if you were to print at slower speeds, the lower temperature is more than adequate. But as you push filament faster, you must raise the hot end temperature a bit to keep up. And it works, the machine is completely capable of extruding up to 30 cubic mm of PLA material per second at 220C.
Anycubic has also installed an upgraded fan on the Kobra 2, which makes sense. The next print layer assumes the previous layer is solid, but if it hasn’t cooled to solidity because you’re printing so fast, the next layer could fail. To overcome this, Anycubic has beefed up the fan to 7000rpm, and that should ensure the layers are cool and solid by the time the hot end comes around again.
The Kobra 2 is Anycubic’s first high speed 3D printer, and its standard print speed is 150mm/s, with a maximum print speed of 250mm/s. I’m sure Anycubic will integrate further enhancements in future Kobra models to improve quality and speed even more.
Advanced Leveling
There’s another advance I’ve experienced with the Kobra 2: its advanced leveling system, which Anycubic has labelled “LeviQ 2.0”.
Leveling systems are critical for FFF 3D printers because they ensure the first layer properly adheres to the print plate. Without sufficient adhesion, there is a huge risk that the print will come loose during the print job and cause a failure, or worse, damage to the 3D printer. Because of this I always watch the first layer of each FFF print to make sure it succeeds.
In the old days there was no such thing as automated leveling. Instead you’d simply try to tilt the print plate to as level as possible and go with that. However, the truth is that all plates, aside from glass, are not really flat. They have slight dips and wobbles, particularly on removable print plates that are so popular these days.
If the printer assumes the surface is flat, it would be wrong and thus first layer extrusions over these dips will be either squished or not sticking.
The answer is to perform an analysis of the plate topology, and that’s what we call leveling. Once the topology is known the printer can dynamically adjust the Z-height to accommodate the dips and wobbles of any print plate.
The question is, how is this best done? In the case of Anycubic’s LeviQ 2.0, they use a proximity sensor attached to the printhead, which uses magnetic fields and inductance. As it gets closer to the print plate, it triggers without actually touching the plate. This is quite different from other sensors systems that involve physical touch. The LeviQ 2.0 inductance sensor is much faster.
LeviQ 2.0 has a feature I’ve seen only on high-end industrial 3D printers: nozzle wipe. The idea is to bring both the hot end and plate to operating temperature before calibration. This ensures the leveling will be accurate as all components will be thermally expanded. However, doing so tends to soften filament in the hot end, which leaks out. This must be removed before the leveling process can begin, and that’s what the wipe does. Other systems that don’t have the wipe feature must rely on the operator to manually remove any material from the nozzle.
LeviQ 2.0 also includes a “trigger switch” that is touched during the leveling process. This enables the system to automatically set the Z-offset since it is at the same level as the plate.
By combining all these steps together, the Kobra 2 is able to competently calibrate itself automatically and ensure proper first layer adhesion.
What makes the Kobra 2 different? It’s the advanced leveling system and its incredible high speed.
Via Anycubic
Will you have your hands on Flsun V400 ?