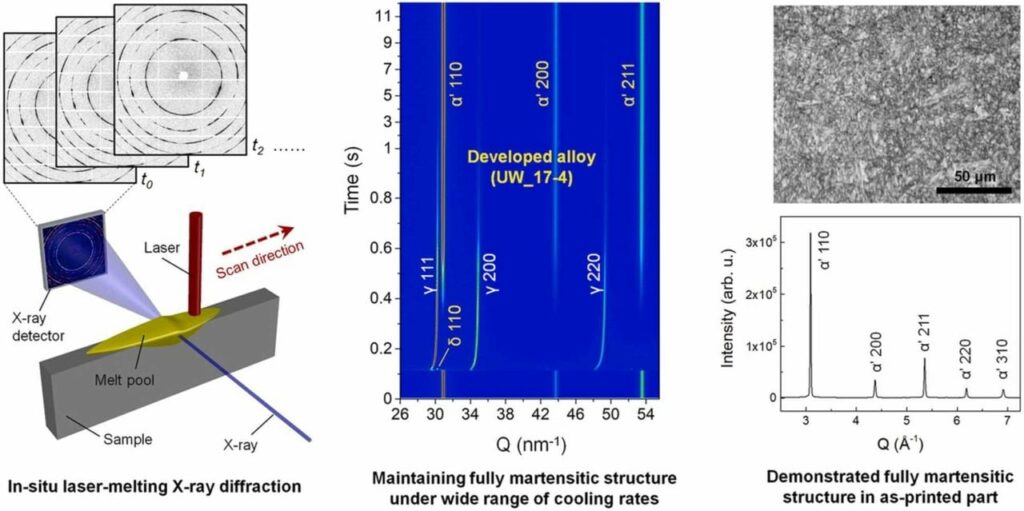
Researchers have found a way to 3D print fully martensitic stainless steel.
Martenistic stainless steel is one of the classes of stainless steel corresponding to a particular crystalline microstructure. The steel’s tetragonal structure allows for hardening and tempering in a variety of thermal profiles, and is thus quite useful in industry.
The problem with current metal 3D printing approaches is that they don’t really produce martensitic stainless steel easily, if at all. This is caused by the wildly varying thermal conditions that take place in the build chamber.
In spite of the efforts of 3D printer manufacturers to maintain consistent build chamber temperatures, the fact is that the energy source (typically a laser) must generate huge amounts of heat to melt the metal powder. The presence of this heat occurs momentarily as the meltpool passes by, leaving rapidly cooling zones in its wake.
The cooling profile largely determines the nature of the crystalline structure. Unfortunately, the messy nature of the cooling profile with current LPBF metal 3D printers is such that it is definitely not conducive to creating martensitic stainless steel crystalline structures.
The news is that the researchers were able to use an X-ray diffraction technique to solve this dilemma. They explain:
“Here we report a martensite stainless steel development guided by phase transformation dynamics revealed by in-situ high-speed, high-energy, high-resolution X-ray diffraction. This developed stainless steel consistently forms desired fully martensitic structure across a wide range of cooling rates (102–107 C/s), which enables direct printing of parts with fully martensitic structure.”
Note the words, “consistently” and “wide range of cooling rates”. That sounds quite a bit like the conditions inside a typical metal 3D printer.
But are these parts truly usable? They explain:
“The as-printed material exhibits a yield strength of 1157 ± 23 MPa, comparable to its wrought counterpart after precipitation-hardening heat-treatment. The as-printed property is attributed to the fully martensitic structure and the fine precipitates formed during the intrinsic heat treatment in additive manufacturing. The phase transformation dynamics guided alloy development strategy demonstrated here opens the path for developing reliable, high-performance alloys specific for additive manufacturing.”
This development could be very significant. There are countless applications where martensitic stainless steel is required, and where manufacturers have dismissed AM approaches. Once this technology becomes commercialized, then you can be assured there will be a lineup of new AM customers for the opportunity to make martensitic stainless steel parts.
Of course, there is a disclaimer here: this is only research at this point, and someone will have to carry this concept forward through the commercialization, which will likely take a year or more to do. It’s also possible this technique could be adopted by existing metal 3D printer manufacturers and incorporated into their products — after negotiation with the inventors, of course. That path could be somewhat faster than if done by a startup company.
Nevertheless, we will certainly see martensitic stainless steel parts being additively manufactured at scale in the near future.
Via Science Direct