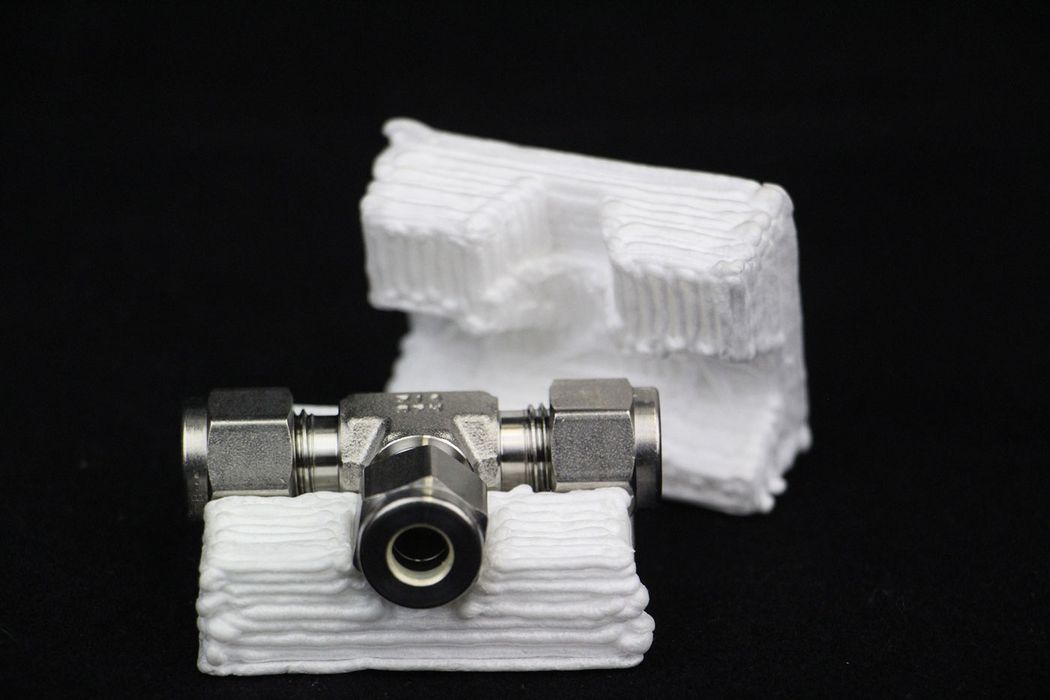
Fraunhofer ICT has developed a versatile printable filament approach that can “foam” in controllable ways.
The German research institute has frequently developed new solutions that eventually make their way to the commercial world, and this latest development is quite likely to do so.
Foam is a highly desirable technique for 3D printing because it enables the production of objects with low density. This can be important for applications involving weight (such as aerospace) or insulation.
A foaming filament is one that is designed to produce bubbles within the material stream when heated. This allows for normal storage of the filament spool, but produced foam material when extruded through the hot end.
Foaming filaments are not new; the first one we observed came from colorFabb with their varioShore material. The material can produce slightly different degrees of “foaminess” as the extrusion temperature changes.
Fraunhofer ICT seem to have refined this concept with the development of new agents that can transform standard 3D print materials into foam-capable filaments. They’ve also developed a specialized print head that “closes” to eliminate the drip problem that occurs with most foaming filaments.
So far they have tested their approach on bio-based PLA, cellulose propionate (CP), and polystyrene (ABS/ASA). These are quite different materials than varioShore, which is TPU-based. Here the materials are rigid.
What’s surprising is the effectiveness of the agents. Fraunhofer ICT reports that they can achieve densities of only 5% of the equivalent solid material. That would allow printing of extraordinarily lightweight polymer parts.
There’s another interesting twist to this: the foaming effect can be controlled by temperature, and this suggests the ability to print foam core objects: objects with a hard shell but with foam inside. This is a common industrial part approach that now could be 3D printed in a single job.
There is a downside, however. The vastly expansive foam — up to 20X the original volume — dictates that the print speeds must be quite slow.
Nevertheless this is an important material development that will almost certainly become commercialized in the near future.
Via 3D Druck (Hat tip to Benjamin)