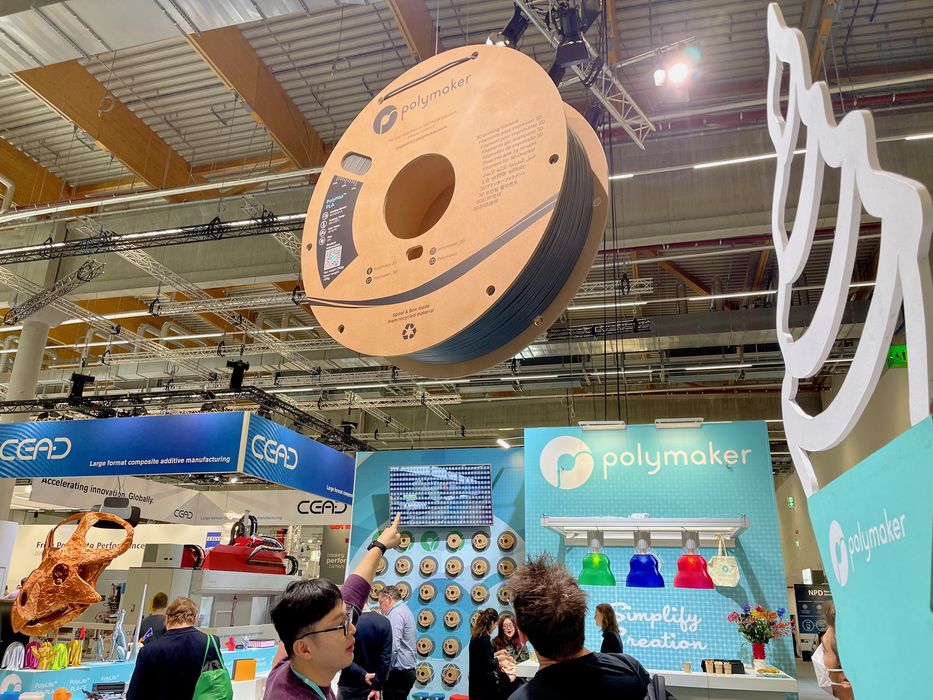
We just completed the epic Formnext exhibition and have some thoughts.
The exhibition is indeed by far the largest additive manufacturing / 3D printing show on the planet by any measure you care to examine: number of exhibitors, attendees, floor space, etc. We’ve been to the event many times before, but this was the first for us since the pandemic. We attempted to visit all 800+ exhibitors, and came pretty close, at least for the exhibitors of interest to readers.
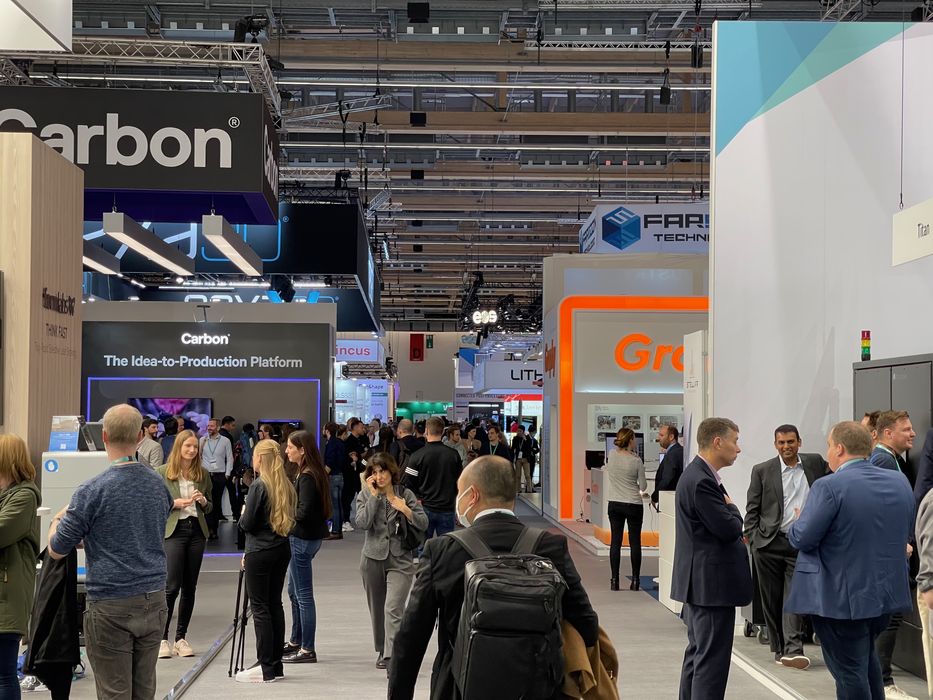
The event was outright cancelled in physical reality in 2020, as organizers resorted to a limited online operation that year. In 2021, the fair opened in physical form once again, but we’re told that participation wasn’t in top form.
Now we’re in 2022, and, it would seem, Formnext was back to normal. They had a similar or perhaps even larger number of industry exhibitors as in 2019 (802), the year before the pandemic. They seemed to have a great deal of attendees (almost 30,000), as the aisles were frequently clogged and some exhibitor stands were effectively impossible to approach due to crowds at times.
All normal. Or was it?
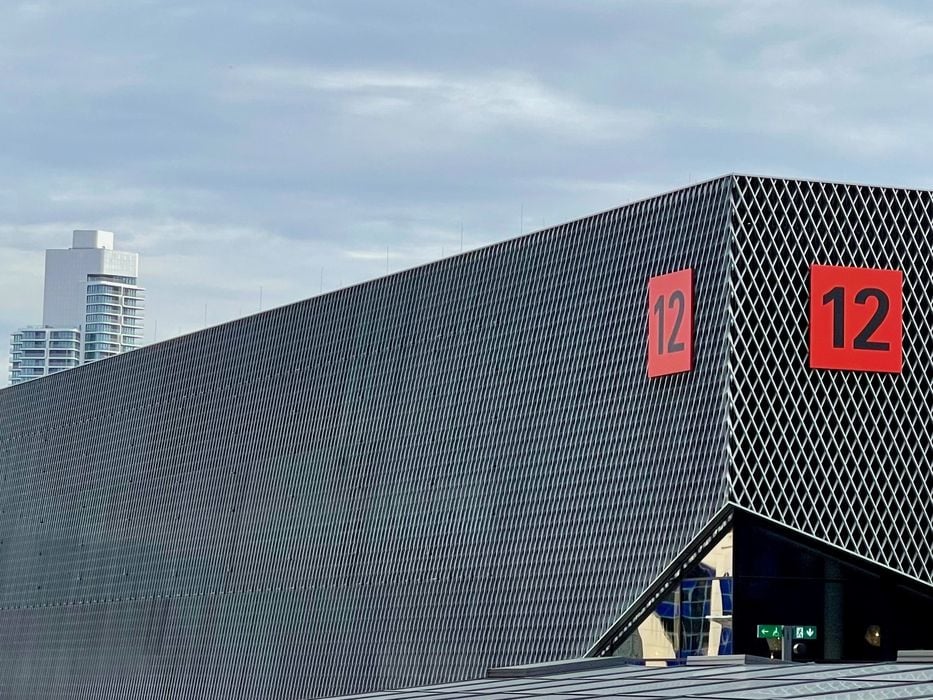
There were some deviations from the norm, some obvious, and some subtle.
One was that there were essentially no Chinese exhibitors, who normally occupy a notable chunk of those showing equipment. This is understandable, as re-entry requirements to China were up until recent weeks, quite severe. Basically you had to go into quarantine “prison” for several weeks before being allowed free. At the time companies had to book space at Formnext, I’m pretty sure they were less interested in going through that protocol, hence the dramatically decreased Asian presence.
There were, as far as I could tell, no Russian companies present, because, well, you know why. I did see and speak with Ukrainian companies, however.
Aside from those visible effects, there were other observations.
Company Participation
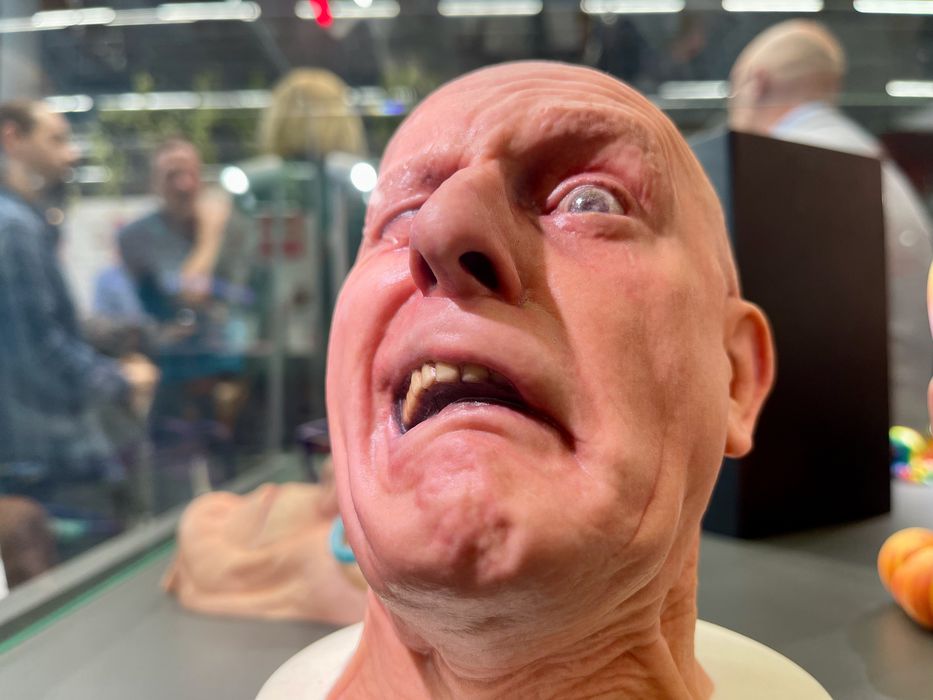
One was a distinct lack of announcements, particularly from the “majors”. Time after time we asked companies what’s new since their display at Rapid last May, and were told, “well, not much.”
Even the biggest companies tended to announce basically nothing, or perhaps a new material or two.
Yet these companies did in some cases occupy vast space for their displays. I suspect it was because the booking deadline might have been long ago when they had different notions of the future state of affairs in November 2022. Once booked, however, you’re going regardless of your 2022 budget.
That said, several leading companies had noticeably smaller exhibition space and fewer staff onsite. This jives with news that many companies had experienced layoffs in past months, some quite major. One unnamed exhibitor said they are “here but we have no money.”
The exception to this was Nexa3D, which somehow ended up with by far the largest stand of all exhibitors, even larger than the biggest companies in the space. This was seen by some visitors as curious, given the company had laid off a large number of staff just months earlier.
I also noticed the distinct absence of several companies that had for many years appeared at the event. I’m fearful for their well being.
CNC Manufacturers
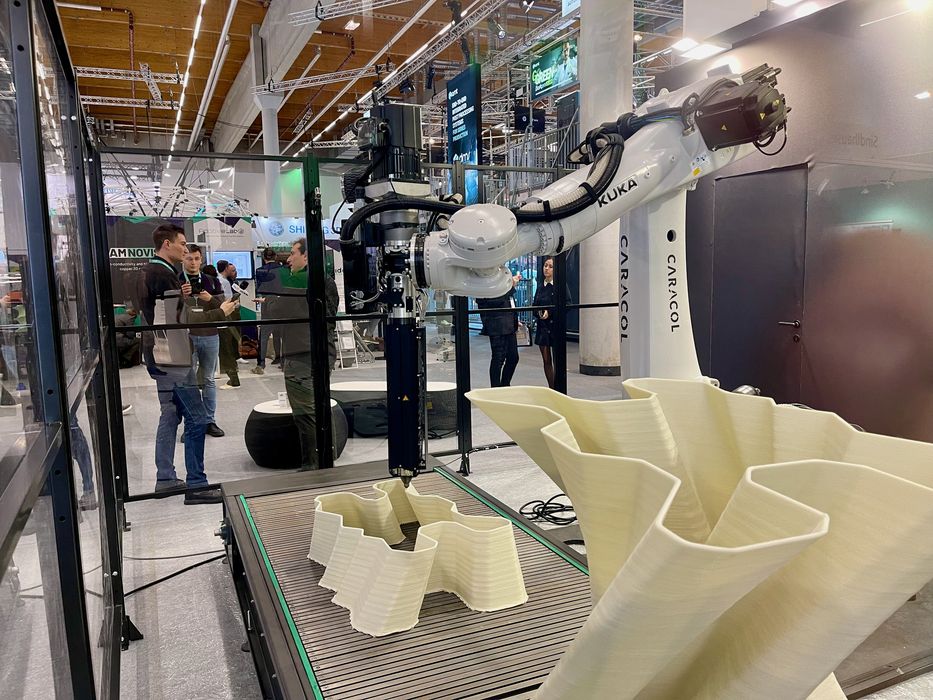
A noticeable trend on the show floor was the appearance of a large number of seemingly new players offering essentially identical wire DED equipment. These are CNC machines with “AM toolheads” pasted on a robotic arm, capable of depositing material to form 3D objects.
It’s not a new technology, but I was surprised at the number of these new participants. But who were they?
As far as I can tell, most of them were existing CNC equipment makers or similar tool manufacturers. My thought is that these companies saw interest in additive manufacturing rising, and quickly threw together an AM machine by adapting a new toolhead to their existing tech.
I’m not sure that’s good for the industry. New players with little experience in additive technology are probably going to mess things up for some customers, whereas the long term players know a great deal more about the practicalities of the technology and exactly how it should — and should not — be used. The last thing we need is more industries upset with AM.
Materials
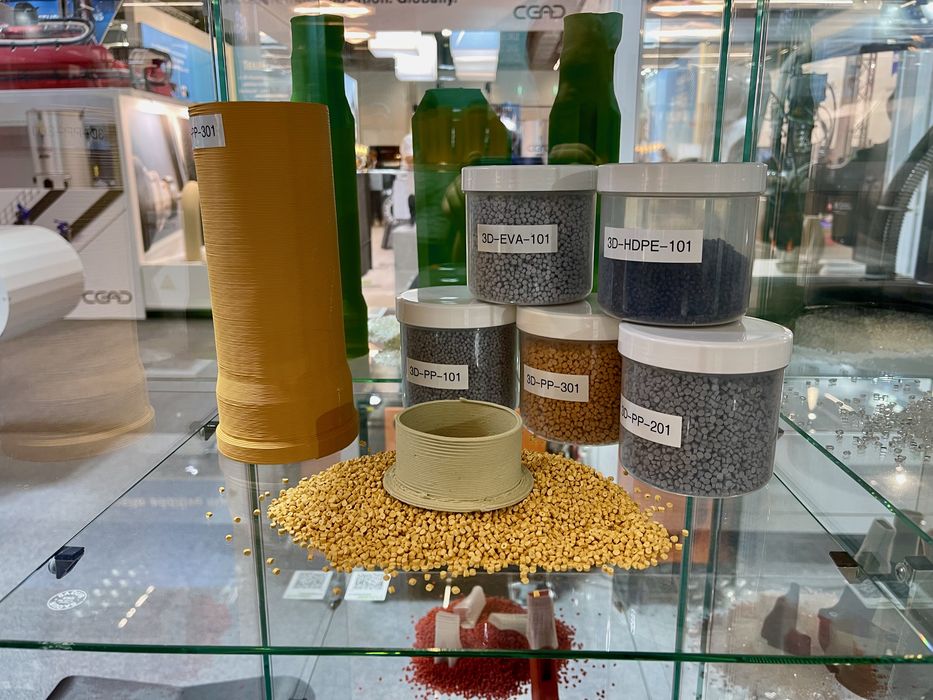
In days past the materials for 3D printing were ABS and PLA, maybe PETG. Nowadays that’s changed. Only recently we’ve seen the introduction of a wide suite of engineering materials, including nylons, PC and high temperature materials like PEEK.
At Formnext 2022 I saw an explosion of an incredible variety of exotic materials, with many exhibitors showing literal walls of options. The choice of materials has never been as high.
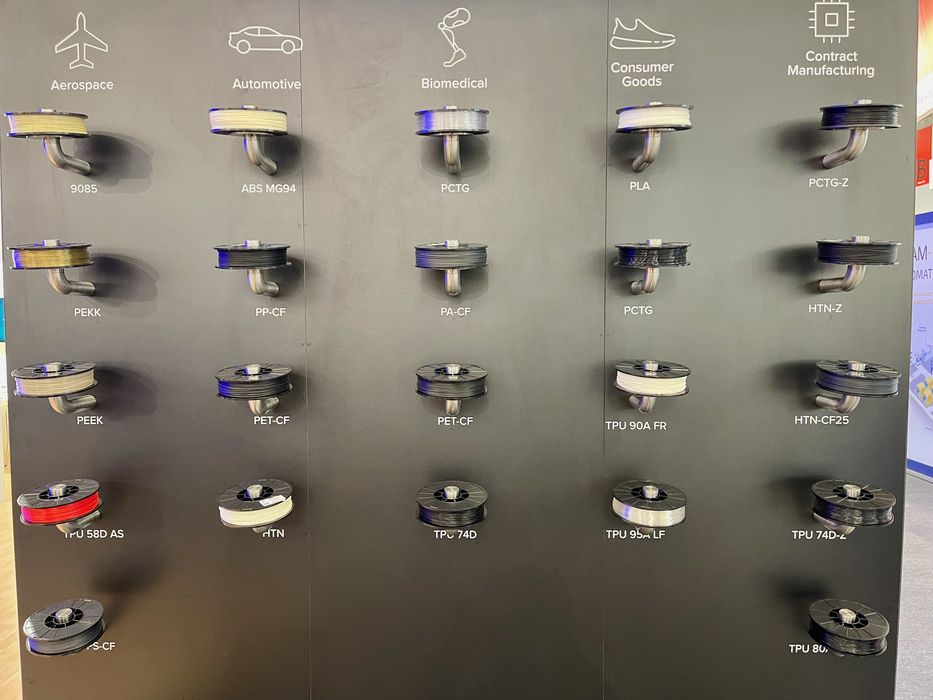
The message here is that manufacturers definitely want very specific materials for their products, and I’m convinced that limitation has kept some from entering the AM world. Now, the industry is answering that challenge with even more choices.
A good example is Carbon, which started with a single type of elastomer a few years ago: “We have rubber-like resin!” Now they offer four types, each with very different properties. Their customers can now choose the right one for the job.
Actually, a better way to say that is that their NEW customers now can use the technology because the right material is now available to them.
Speedy Printing
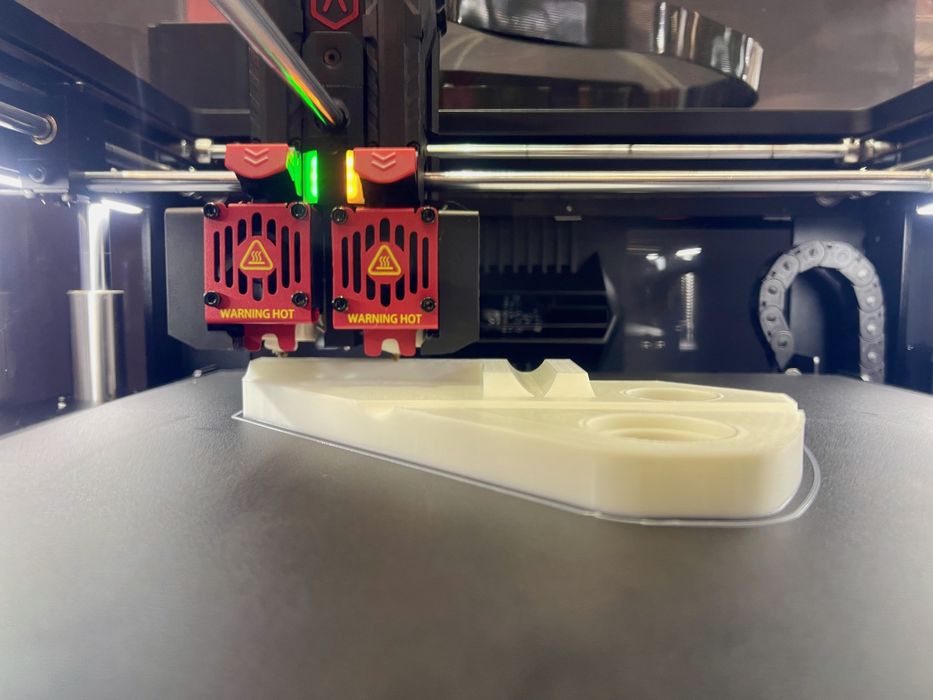
Another slight trend that seems to be emerging is a new class of high speed FFF 3D printers. Typical desktop devices run at around 40-60mm per second, but an increasing number of companies offer machines with noticeably faster equipment with speeds ranging from 200-400mm/s.
Raise3D even offers an upgrade kit to speed up their Pro3 series for a pretty reasonable price.
I suspect this trend will continue and before too long we’ll expect a minimum of 200mm/s print speeds on any acceptable device.
Post Processing
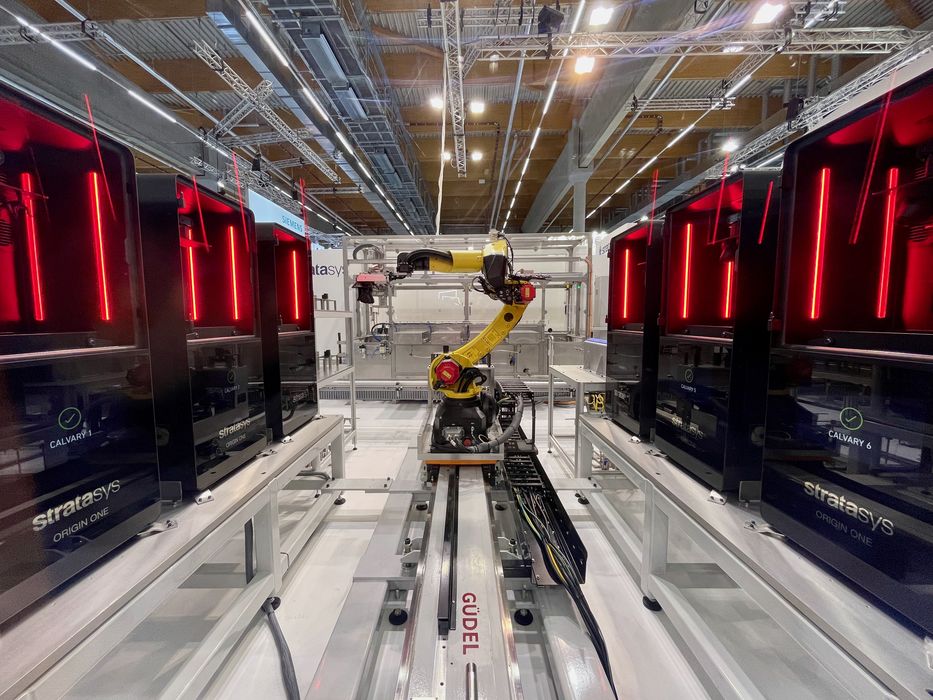
Another recurring theme was aspects of post processing. Anyone who’s undertaken a 3D print job will know that the “printing part” requires the least manual effort, and the post processing is where all the work takes place.
This could include removing supports, sanding, painting, smoothing, etc., but also there are requirements for sorting, handling, packaging and other aspects that occur after the part is done on its own.
I saw a wide variety of efforts by many companies to address this issue with automation, software, AI and just plain mechanics.
It’s becoming increasingly important as companies shift towards mass manufacturing from mere prototyping. What do you do when you have 100,000 parts being made each week? How do you smooth them? How do you package them? How do you know which part is which? These are challenging issues, and there are solutions on the way.
However, these solutions have yet to agree on standardization that could enable future “plug and play” assemblies of post processing tech.
Alternative 3D Printing Processes
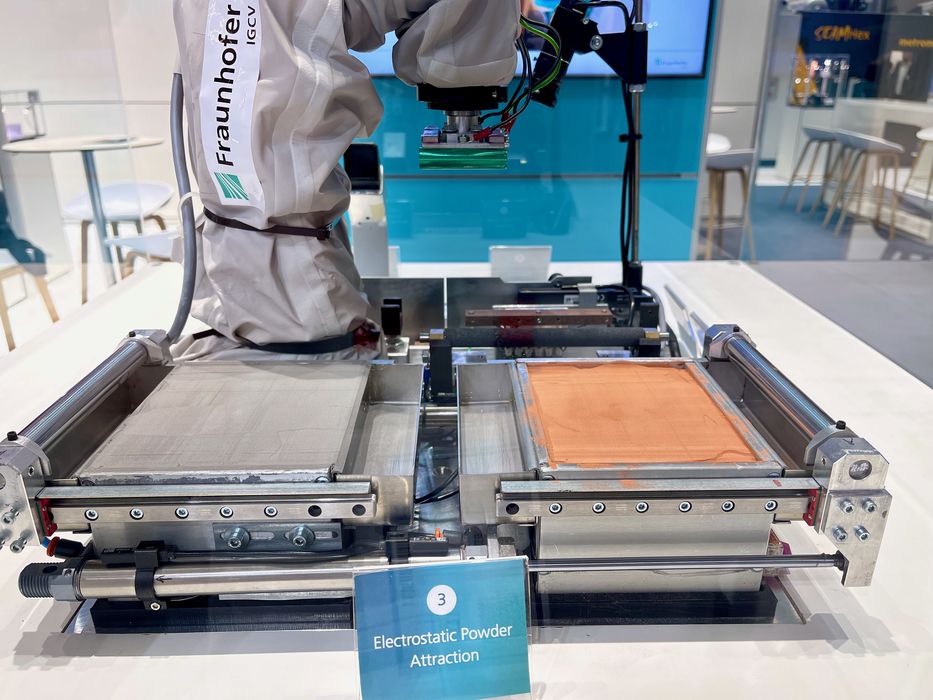
The time when there were three processes (FFF, SLA and SLS) is long past. As has been the case in every Formnext I’ve attended, there were a number of startup companies and research firms offering unique takes on building objects with additive approaches.
Some were a bit kooky and likely not going to get far off the ground, but others seem well-funding and with clear thinking. In coming weeks I’ll provide details on some of the more interesting options I saw at Formnext, as well as the normal stuff.
The industry will be shaken up, as it always has been.