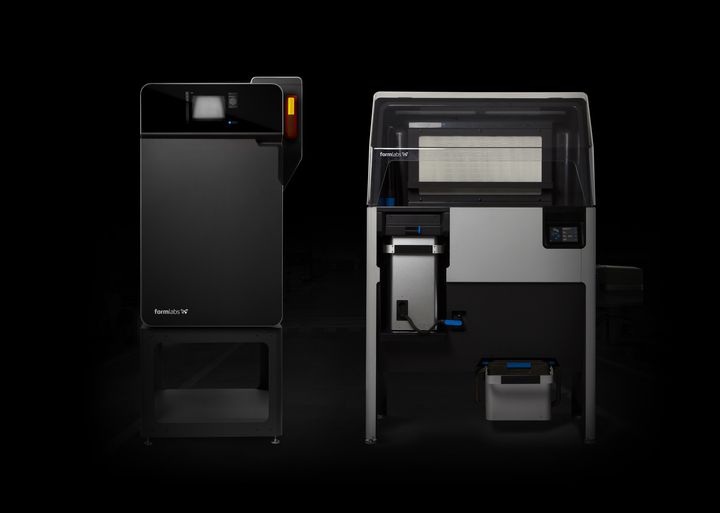
At long last, Formlabs has released the Fuse 1, their production SLS 3D printer.
The company has been working on the Fuse 1 for quite a long time. The company says the device has been in development for seven years, but we’ve been seeing it occasionally at trade shows where Formlabs has been showing prototypes of the Fuse 1. Fuse 1 was first announced in 2017, four years ago.
Typically, machines are released at the time of announcement or within a few months of announcement. That was definitely not the case here, as multiple years have elapsed since the initial announcement. In fact, we’ve had several stories pondering the reasons for the repeated delays.
I have some suspicions of why the delay occurred, but let’s hold that for later. Meanwhile, let’s look at what was announced.
Formlabs Fuse 1
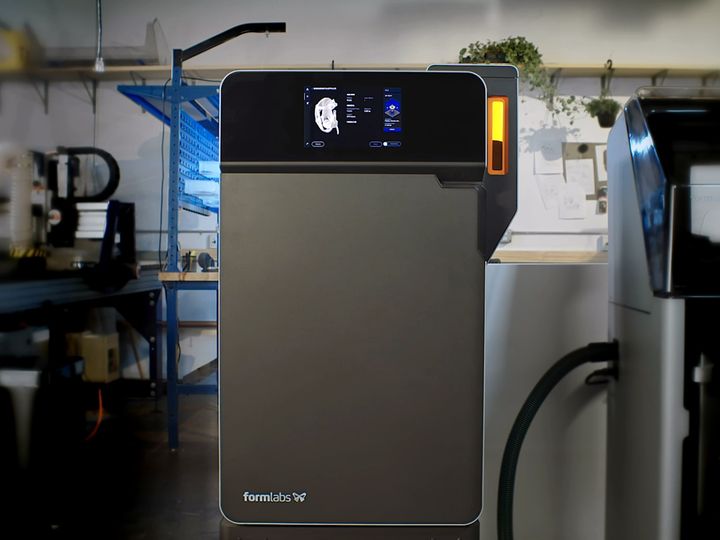
The Formlabs Fuse 1 is an SLS 3D printer, meaning it uses a powerful laser to selectively fuse polymer powder on a flat bed. This is not a new technology, but one that is now available for companies to produce due to the expiration of the original patents. The Fuse 1 offers a build chamber volume of 165 x 165 x 320 mm.
This approach offers a number of advantages, aside from a smooth surface finish and high resolution. The main advantage is that there is no need for support material, as surrounding non-fused powder supports any overhangs or loose parts.
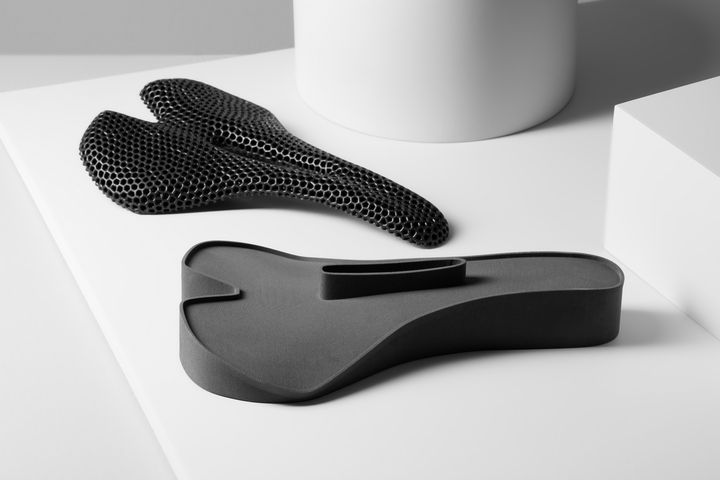
The absence of support structures does not mean there is no need for post-processing. Instead you’ll have to dig out the completed 3D prints from the build chamber, which is full of powder.
Formlabs Fuse Sift
Fortunately, Formlabs simultaneously announced the Fuse Sift, an accompanying finishing station.
If you’ve ever used a powder-based 3D printer, you’ll know that handling powdered items can be quite messy. However, it seems that Formlabs has designed the entire system to minimize mess, and consequently waste of material.
The Fuse Sift will accept an entire sealed build chamber from the Fuse 1, and this can be done immediately upon print completion. That leaves the Fuse 1 ready for a second build chamber to start a second job right away without waiting for the first job to be post-processed. I’m impressed with the steps they’ve taken to minimize powder spills.
You can see how this works in Formlabs’ introductory video:
Fuse 1 Materials
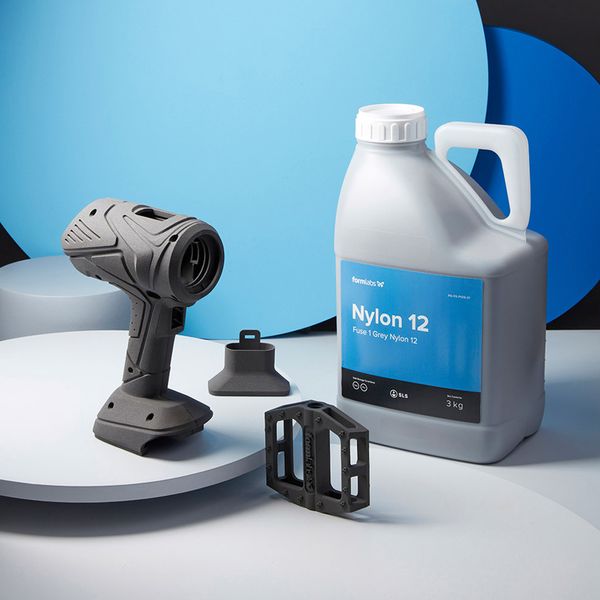
The Fuse 1 is initially set up for nylon powder (PA12), which is a dark color as opposed to the white color you might see on much more expensive SLS 3D printers. This is likely a means of lowering the cost of the Fuse 1, as fusing white powder requires more energy, thus more expensive laser systems are required. Darker powder allows for lower power lasers and reduces overall system cost.
Formlabs is developing additional materials for the Fuse system, and likely the next available material will be PA11, with others to follow.
The combination of the SLS process and PA12 material allows the Fuse 1 to produce highly accurate and strong 3D prints. In fact, the quality will certainly be high enough for use as end-use production parts. That fact and the continuous workflow with the Fuse Sift mean the system could be used for low-volume production.
The material has another very interesting property: high reuse. Normally SLS systems use a mix of 50% fresh powder combined with 50% recycled powder that was used — but not fused — in previous jobs. The reuse method does reduce the overall cost of material somewhat, but the higher the ratio of recycled powder, the lower the quality of the produced parts. For extra-special jobs, some operations might use 100% fresh powder to ensure the best quality.
The Fuse system allows a reuse ration of up to 70%! In other words, each job could save 20% on powder cost over typical SLS machines. That could be significant for workshops running the Fuse 1 system continuously.
Fuse 1 PreForm
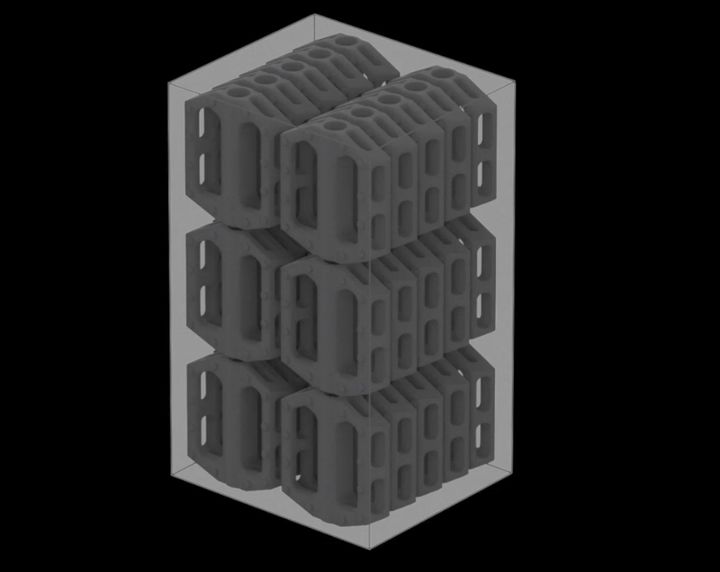
The software for the Fuse system is in fact Formlabs’ familiar PreForm tool. It can set up jobs in a highly intuitive manner, and is in my opinion the easiest slicing software one can use.
Now PreForm can handle SLS jobs for the Fuse 1, but there’s a bit more to the story here. SLS allows for three-dimensional job packing, something that cannot be done for FFF or SLA systems where there’s only one layer of parts allowed. In SLS you basically Tetris all your parts to fill the build chamber and then let the system run overnight. PreForm now has the ability to perform advanced job packing to maximize use of the Fuse 1.
Formlabs says the Fuse 1 is priced at US$18,499, and the Fuse Sift is priced separately at US$8,999, which are very decent prices for such a high-quality and automated system when compared to high-end industrial units.
As for the long delay, I can only speculate that Formlabs has spent the time tuning the system to ensure that its ease-of-use is aligned with the expectations set by their Form system. Formlabs clients will no doubt be comparing the two and any difficulties with the Fuse 1 will be more noticeable.
Via Formlabs