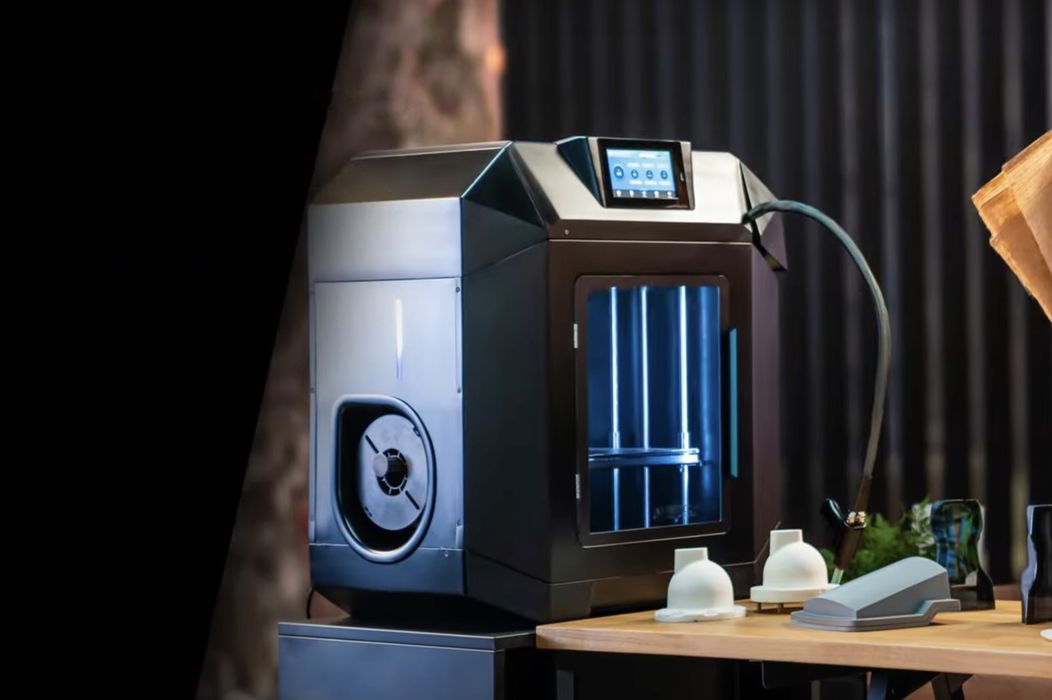
I’m looking at a new manufacturing process called “RIM” that makes use of 3D printing.
RIM was developed by Texas-based Neckog Industries, and implements it in their upcoming Flovv-e device.
So what’s RIM all about? It stands for ”Reaction Injection Molding”. It’s really a hybrid process in which a mold is first 3D printed, and then used for injection molding.
The Flovv-e is indeed a 3D printer, and it can print molds in ABS material. However, the interesting part is that the Flovv-e also includes an accompanying injection molding system that can be used on the freshly 3D printed mold.
Hold on, what exactly can you mold with this? ABS molds aren’t suitable for many materials. It turns out that the RIM process is specifically designed for molding polyurethane objects: foam!
The Flovv-e’s injection molding process uses a two-part system. It stores two resins in separate containers, which are mixed in a high pressure chamber for injection into the mold.
On the left side of the Flovv-e you will find all the equipment for injection molding, including a coloring kit, mold release material, nozzles, mold bolts, etc.
It seems that with the purchase of a Flovv-e the operator will be instantly ready to produce injection molded polyurethane parts. Many, in fact, as the molds can be reused multiple times.
That could be a very convenient solution for certain businesses, particularly those that need to occasionally produce unique polyurethane objects.
What’s most intriguing here is the entire concept of the Flovv-e. The process described by Neckog Industries is one that’s long been done in 3D printing: design & print a mold, then use it for injection molding. The difference is that the entire process is bundled into a single device.
That’s something we haven’t seen frequently in the 3D print space, where most manufacturers simply offer standalone 3D printers. It’s usually up to the buyer to determine what to make and how to do so with their 3D printer.
With the Flovv-e we instead have a device that is dedicated to a very specific manufacturing process. Bundling these functions together make it far easier for the operator, yet constrained in what it can make.
It may be that we could see similar hybrid implementations that bundle up common 3D printing workflows into easier-to-use packages.
In the meantime, those requiring polyurethane parts might consider looking at the Flovv-e, which isn’t quite yet available.
RIM is not new. It was developed in the 60s and predates Additive Manufacturing. It is a well established process. 3D printing moulds for RIM is not new either, we used to do it 25 years ago. This is just a small desktop machine.