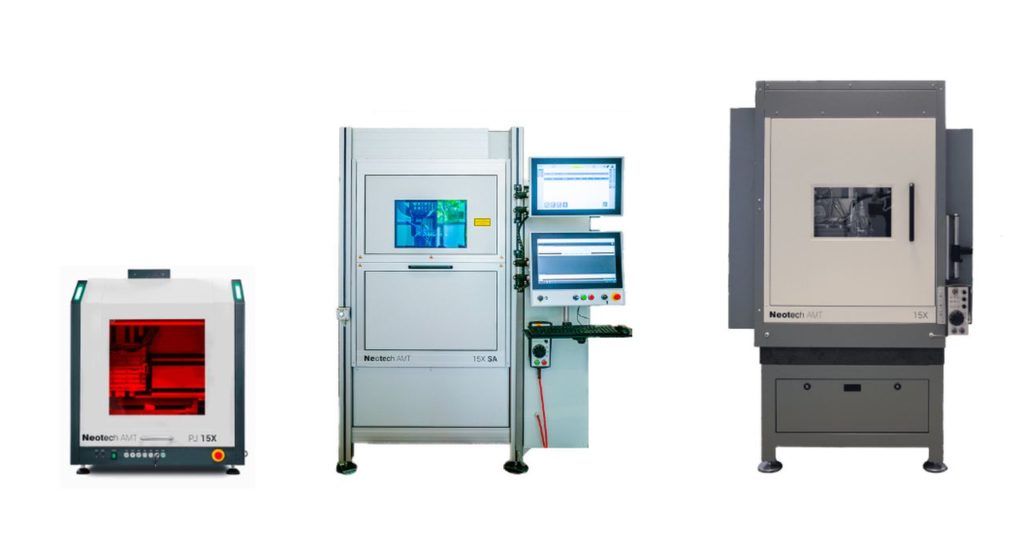
A company provides five axis electronic 3D printing, but what is this used for?
Electronics 3D printing is not widely understood by many in the 3D space, but it is a fascinating topic that more should be aware of and make use of.
3D printing typically produces the solid parts of a mechanical assembly, but these assemblies become far more interesting when electronics are involved. Motors, sensors and software can transform chunks of plastic into a functioning machine.
But how can this be done with 3D printing?
Most printed circuit boards are built using a subtractive process, where material is removed to leave the electrical traces through which signals and power travels. This implies there will be a circuit board installed in the device, which must be connected to sensors and motors with cabling. That’s pretty much the standard design used in most machines these days.
3D printing offers the possibility of embedding the electrical traces on and inside the mechanical parts of a device. Instead of running a cable from a central PCB to a sensor, there could be conductive material printed instead. This would simplify assembly of the device, as there would be fewer or even no cables involved.
Some 3D print companies attempt to do this by adding extruders to conventional 3D printers that can deposit lines of conductive material. As the print proceeds, electrical traces can be slowly built up. But there are constraints on this approach, mainly due to a conflict between the extrudability of a material and its electrical resistance.
Another issue is that the path of an electrical trace is not necessarily solely along a layer; it could (and likely will) need to pass through multiple layers. This creates an awkward interface for the conductive material as it could form a “stair step” pattern when complete, which may not be optimal for certain applications.
One company that’s doing something quite different in this space is Neotech AMT.
The company has developed a unique five axis motion platform that can deposit electrical traces in three dimensions. Currently the company markets three devices using this technology, the 45X G4 for mass production, the 15XSA for rapid prototyping, and the compact desktop PJ 15X for prototyping.
Five axis 3D printing has been developed previously, but only for thermoplastics. This approach is far more costly than simpler motion systems, but allows 3D printing to take place without the need for support structures: the motion system simply rotates the in-progress print to the right position for easy deposition.
That support-free advantage is leveraged by Neotech AMT as their technology can deposit conductive traces on the surface of a 3D print very easily, as you can see in this short animation:
Neotech AMT has been developing this tech since 2006, and has been distributing it since 2010.
But to truly leverage this technology, product designers would have to fully embrace the concept and create designs that place the electronics in the product in very different ways.
In spite of Neotech AMT’s technology being available for several years, I am curious as to why it has not been adopted more strongly by the additive manufacturing community. The prospect of making parts that already include electronic traces should be an advantage.
Via Neotech AMT