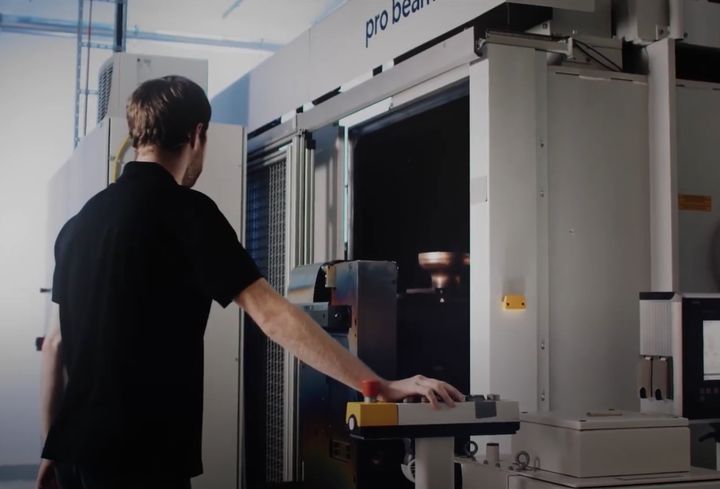
Two companies have partnered to develop an additive manufacturing system using wire-based electron beam melting.
The companies are FIT AG and pro-beam Group, both based in Germany.
FIT AG has been around for decades providing a variety of additive manufacturing and related services, while pro-beam Group has decades of experience in EBM technology, although it’s historically been used by them for cutting and welding processes.
FIT AG is a larger provider of AM services, now with 250 staff. They currently offer 3D printing in these processes:
- Laser melting (metal PBF)
- Electron beam melting (metal PBF)
- WAAM (wire arc AM)
- Supersonic (SPEE3D)
- SLS
- Stereolithography (3D Systems)
- PolyJet (Stratasys)
- Full Color PolyJet (Stratasys)
- Binder jetting
- GDP (Massivit)
- SCA (Selective cement activation)
As you can tell, they offer an enormous range of 3D printing technologies from a number of providers. However, FIT AG is not a company that builds 3D printers; they acquire them from 3D printer manufacturers and operate them. Their true value proposition is in the other activities in the AM lifecycle.
FIT AG specializes in the workflow surrounding the actual printing, and provides engineering, consulting, design, process, and other aspects.
Meanwhile, pro-beam Group seems to be developing a 3D printer, as seen in this video:
From the video we can tell that the technology will be wire-based EBM, where a welding wire will be instantly heated to melt point as it is fed from the toolhead. By using a robotic system the toolhead can move around and deposit material into 3D objects. It also appears that the potential build volume for the new system will be rather large.
The two companies have arranged a partnership where their specialty knowledge will be combined. FIT AG said:
“In a framework agreement, the two manufacturing specialists have expressed their intention to pool their know-how and create new technological opportunities through the resulting synergies. The cooperation will cover the areas of process development, material development, and equipment development for additive electron beam technology.”
This seems to be a very complementary arrangement; FIT AG can provide operational skills, materials knowledge, process templates, while pro-beam Group can build the hardware. With the two working together they will no doubt develop a system — that’s machine and process — better than each could have on their own.
The resulting AM system will be added to the list of options for buyers, and certainly will appear early on FIT AG’s workshop floor.
Via FIT AG and pro-beam Group