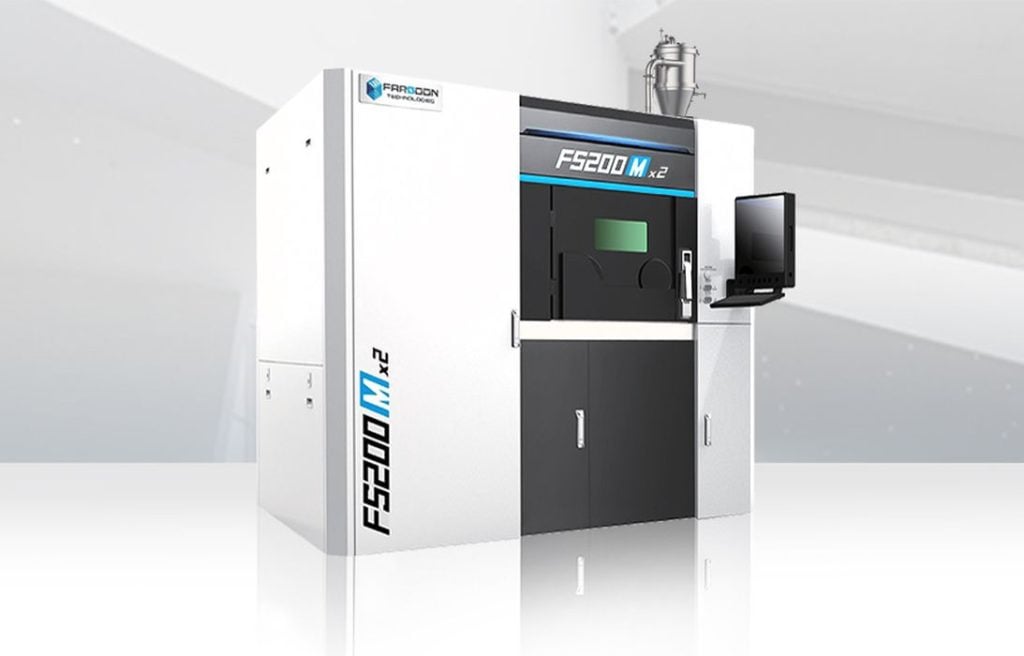
Farsoon announced the FS200Mx2 Metal 3D printer, which includes quite a few very interesting features.
Farsoon, based in Changsu, China, operates worldwide and produces both metal and polymer 3D printing solutions for industry. In fact, they offer about a dozen major devices, with five being metal 3D printers.
The latest is the FS200Mx2, which falls in their midrange category. That classification is based on the build volume of the device, which happens to be 425 x 230 x 300 mm, large enough for some serious parts, but not the largest possible volume from the company.
The “x2” in the product name should hint at this machine’s major feature: twin 500W lasers, which should provide more throughput and print speed, as two lasers can operate on a part via overlapping laser zones. Farsoon explains:
“The rectangular build platform is well suited for the dual 500-watt laser configuration; with advanced calibration algorithms precisely controlling both lasers’ operations, achieving an intelligent distribution of each laser’s up time for an overall improved build efficiency; and a softened laser overlapping area for more uniformed part properties.”
However, the FS200Mx2 has a few more interesting features beyond the dual lasers. For example, there is a back-flush filter feature that should extend the life of system filters. That should not only save on filters, but increase machine uptime and reduce operational labor costs.
One of the more interesting features is a quality control system that’s based on a build chamber camera system. The cameras observe each powder recoat layer to ensure it has been properly deposited. If it hasn’t then the system will automatically re-run the recoat until it is successful. This should cut down on failed print jobs, and thus save more money on materials and machine time.
The FS200Mx2 will also automatically notify the operator when the powder reservoir is running low. In some cases, this could increase machine uptime if operators refill can be delayed.
Finally, a very quiet but very important feature is the machine’s footprint. The footprint is the floor space that the machine must occupy on a factory floor. At first you might think that the footprint is simply the machine’s exterior dimensions. Instead, the footprint is actually those dimensions plus the space required to access the machine when service panels are opened up. Typically this quadruples the footprint as panels usually are opened on all sides of the machine.
That’s not the case with the FS200Mx2, which has service panels only on the front and right sides. This leads to a relatively small footprint of only 3.5sm. The implication is that the device will fit operationally into a much smaller space, or more units could be placed within a given space. For operations with a space crunch, the FS200Mx2 could be ideal because of this feature.
My hope is that other 3D printer manufacturers consider the footprint issue. As more manufacturing moves toward the technology, we will continue to see growing farms of machines, and they’ll have to be squeezed together somehow. Farsoon is setting a good example here.
Via Farsoon