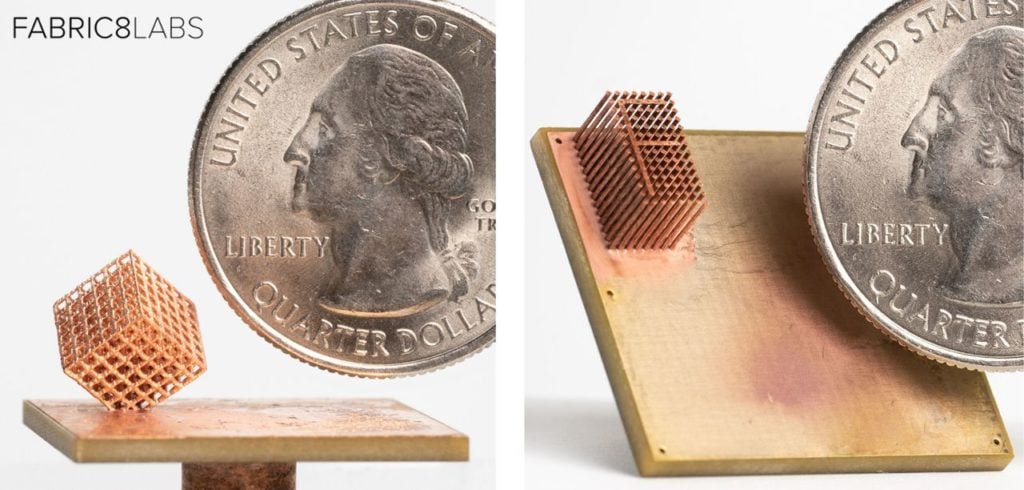
I came upon a news release explaining that Fabric8Labs raised US$19M. But who are they and what do they do?
There’s no shortage of new 3D printer startups, even decades after the first rudimentary 3D printing processes were developed. This clearly shows how much the industry has to go to mature.
One of the latest to become visible is San Diego-based Fabric8Labs, which has developed a mystery metal 3D printing process. Little is known about the company; we’ve never spoken with them nor seen them at a major 3D print event. They were founded in 2015, and currently have several dozen staff on hand.
The company has received two rounds of funding, first a US$4M jolt in 2018, and this week a US$19M boost from a variety of investors, with Intel Capital as the lead investor. That totals US$23M raised from VCs. I’m not surprised to see Stanley Ventures among their investors, as that organization, the VC arm of Stanley Tools, is frequently found investing in 3D technologies. Mark Cuban is also a major investor in Fabric8Labs.
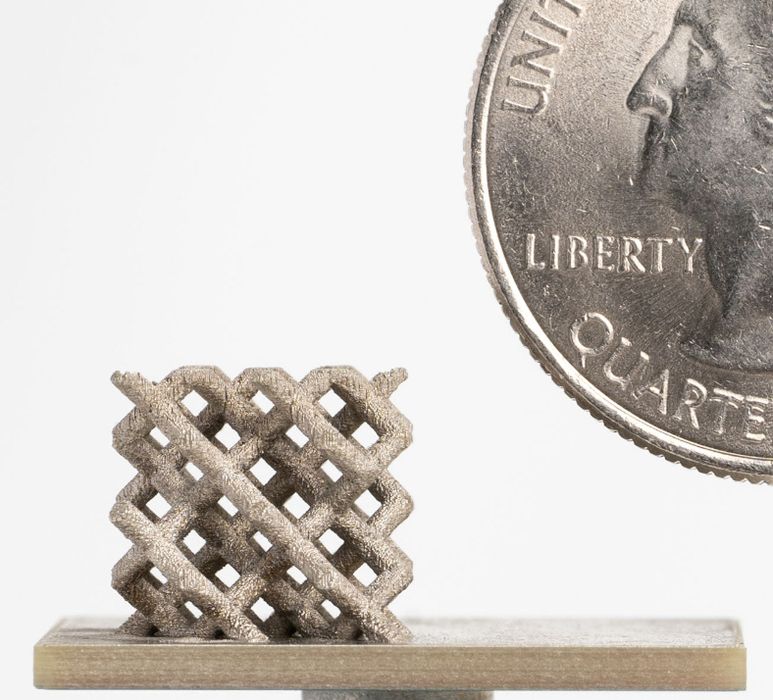
The company is developing a metal 3D printing process that appears to be somewhat different from existing approaches. In an interview on TechCrunch, Fabric8Labs’ CEO Jeff Herman briefly described the process:
“Our process is inherently different and does not utilize powder nor thermal processes. Instead, it is based on electrochemical deposition, which operates at room temperature, has a significantly lower power demand, and utilizes an aqueous (water-based) solution made from low-cost metal salts. In combination, the commodity priced raw materials and power-efficient process enable a step change in reducing the total cost of ownership and cost per-part.”
Fabric8Labs’ website does not explain their process or product in a descriptive manner, so we’re left to speculate on what they might be doing.
Based on the statement from Herman and the images from Fabric8Labs, my speculation is that the Fabric8Labs metal 3D printing process:
- May use a form of liquid droplet printing using very fine resolution inkjet heads
- Bonding occurs electrochemically, like electroplating
- Could be scaled to larger volumes by increasing the number of inkjet heads
- Requires prints to undergo a post-processing step or steps in a furnace to finalize the print
- Is capable of extremely fine resolution
- Is able to handle extreme overhangs, likely enabled by a separate support liquid that solidifies, but later disappears during post-processing
- Does not use lasers
That last point is important, because the presence of lasers in traditional PBF-style metal 3D printers is one of the main generators of high costs. To print faster with a PBF system, you must increase the laser power (more cost) or add more lasers (even more cost).
Another factor limiting PBF systems is their use of powder. Powders can become airborne and thus become a toxic and explosive risk. With a liquid approach as is used by Fabric8Labs, all of that risk — and cost — goes away.
The energy consumed by this style of process is certainly far less than that used by traditional PBF metal 3D printing systems, and therefore Fabric8Labs could have a significant pricing advantage over PBF competitors once their products hit the market.
There are some questions about the materials possible with this process. To enable electroplating, the metals must be mixed with salts, and it’s not clear to me what this means regarding the potential breadth of material choice.
This is a notable development, because PBF metal 3D printing is seen as the most popular method to produce dimensionally accurate, higher resolution metal parts. While there are lower cost alternatives, they often don’t produce parts with the same properties. It may be that the Fabric8Labs process could pose serious competition for existing PBF players.
While potentially damaging to competitors, the availability of a lower-cost, lower-energy alternative that can produce metal parts with precision and high resolution would be welcomed by industry.
Via TechCrunch and Fabric8Labs