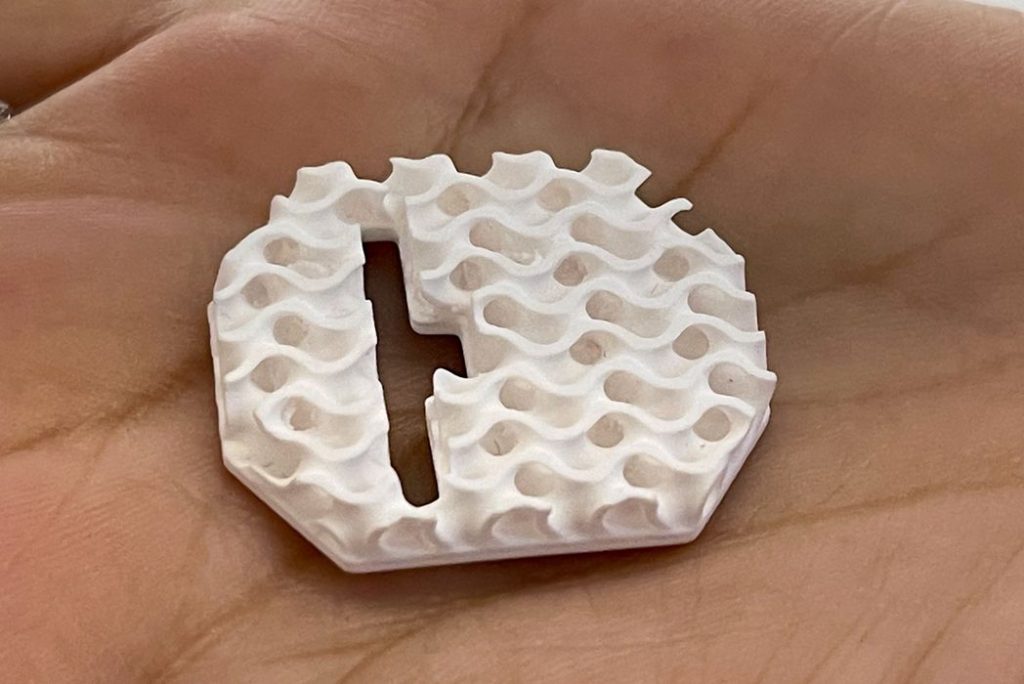
Fortify has been developing new and quite interesting 3D printable materials.
We recently spoke with the Boston-based company about their progress. They launched only a six years ago with a highly unusual 3D printing process called “Fluxprint”.
Basically the process, as described to us by founder and CEO Dr. Josh Martin back in 2019 uses magnetic fields. While many 3D print processes can use composite materials that involve a mix of fibers for strength, they all suffer from a problem: the fibers are randomly oriented.
Fortify’s Fluxprint process uses a magnetic field to orient the fibers during the photopolymer printing process to achieve far stronger parts. The magnetic field can even be rotated to make the fibers align to different directions during the print.
This all works because the fibers mixed in with the photopolymer resin are ferric-coated, which make them susceptible to the magnetic field.
It’s a fascinating process that can make extremely strong parts, something not usually achievable with resin 3D printing.
Since their launch they’ve gained considerable attention, and received a hefty US$20M in investment cash to expand operations.
Since their launch they’ve continued to develop a series of unique materials suitable for Fluxprint. Their current list of materials includes:
- HTS, a high temperature and high strength material that can substitute for PEEK and other high temperature exotic materials
- DT, a stiff polymer reinforced with ceramic fibers for tooling applications. This material has a heat deflection temperature exceeding 300C, meaning it could, for example, be used as a mold for injection molding of ULTEM
- Radix, a low-loss dielectric material for use in electronics applications
- High Purity Alumina ceramic, which yields parts of 99.8% ceramic with only a shrinkage rate of 12%
- Low Shrinkage Aluminum Silicate, another ceramic that exhibits only 5% shrinkage during post-print sintering
- ESD High Temperature, which prevents static charge build up for electronic applications
- Thermally Conductive Dielectric, for unusual electrical applications requiring insulation but also thermal cooling
- ESD-Elastomer, a flexible material that has electrostatic dissipative properties
All of these materials can be printed in high resolution using Fortify’s DLP-based 3D printing systems. In addition, the company is also certifying a series of third-party materials for use in their systems.
In speaking with their representatives, it seems that they’re focusing on “technical ceramics” these days, as you can tell from their list of materials. These are quite impressive materials, which by the way were developed in conjunction with Tethon 3D, makers of all manner of ceramic resins.
I was able to see some sample parts printed with these materials and they indeed were impressive and stiff, as you can see in the images. Fortify told us some of their parts have been used in oceanic applications for months at a time, clearly demonstrating their durability.
Finally, it sounds like Fortify is also now performing contract manufacturing for injection mold tooling, likely using their DT material, which is ideal for that application.
Via Fortify