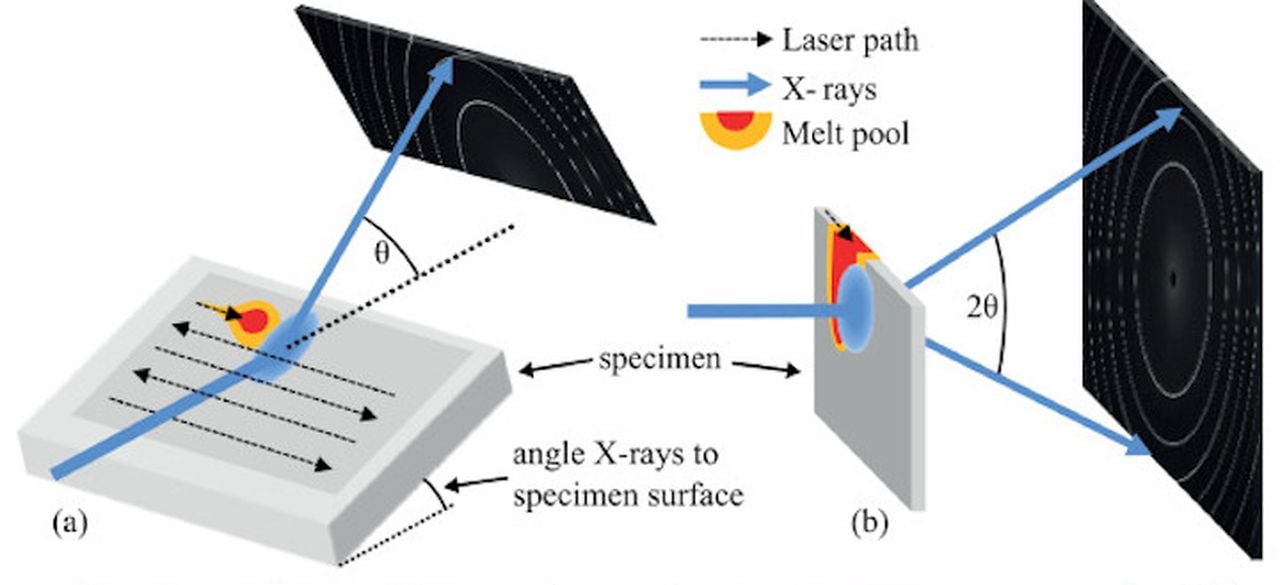
Researchers have now probed the mysteries of metal 3D printing with particle accelerators.
Metal 3D printing is a practice becoming more widespread in industry, but it is still facing significant barriers.
One problem is that there is an extremely limited set of possible materials that can be used by today’s metal 3D printers, while there are thousands of alloys being used by industry in traditional making processes.
The reason for the limitation has a lot to do with the resulting parts. Due to the 3D printing process, which is typically LPBF where a high-power laser swiftly melts a bed of metal powder, the characteristics of the metal are not always predictable.
Key part properties, such as thermal resistance, strength, chemical resistance and more are all related to the micro crystalline structure of the metal in the part. This microstructure is largely determined by the cooling process when the part is made.
In traditional making processes, the cooling processes can be made uniform and predictable, leading to predictable performance parts.
However, the thermal conditions in LPBF metal 3D printing are quite extreme. While the laser blasts the meltpool, the temperature is significantly higher than surrounding areas. Then the laser moves away and cooling takes place. But then the laser re-appears on the subsequent layer, generating significant rise and falls in temperature.
The result is a part with microstructures that may or may not meet requirements.
The new research attempted to determine how the cooling process actually unfolds within a LPBF environment.
The experiments involved using two different particle accelerators. These “synchrotrons” are circular arrangements where particles spin around and around, gaining speed during each circuit. Eventually they are magnetically routed out of the circuit to impact a target. The two facilities involved were the Argonne National Laboratory’s Advanced Photon Source and the Paul Scherrer Institute’s Swiss Light Source.
The particles manifest as X-rays as they hit the target, and by measuring their reflections it is possible to produce images of the target. The target in this case was a meltpool that represented the activity that takes place in an LPBF metal 3D printer.
Specifically, different cooling rates were examined using this rather expensive setup. The cooling rates ranged from tens of thousands to a million kelvins per second.
The researchers wanted to compare the results of the additive process with well-understood traditional cooling models used in industry.
NIST explains the findings:
“The data the researchers collected depicted the push and pull between two kinds of crystal structures, austenite and delta ferrite, the latter being associated with cracking in printed parts. As cooling rates surpassed 1.5 million kelvins (2.7 million degrees Fahrenheit) per second, austenite began to dominate its rival. This critical threshold lined up with what the model foretold.”
Research of this type will eventually lead to more finely tuned metal 3D printing, which will provide a means to more easily produce reliable parts that meet engineering requirements. That will only mean an increase in use of metal 3D printing in the long term.
Via NIST and Science Direct