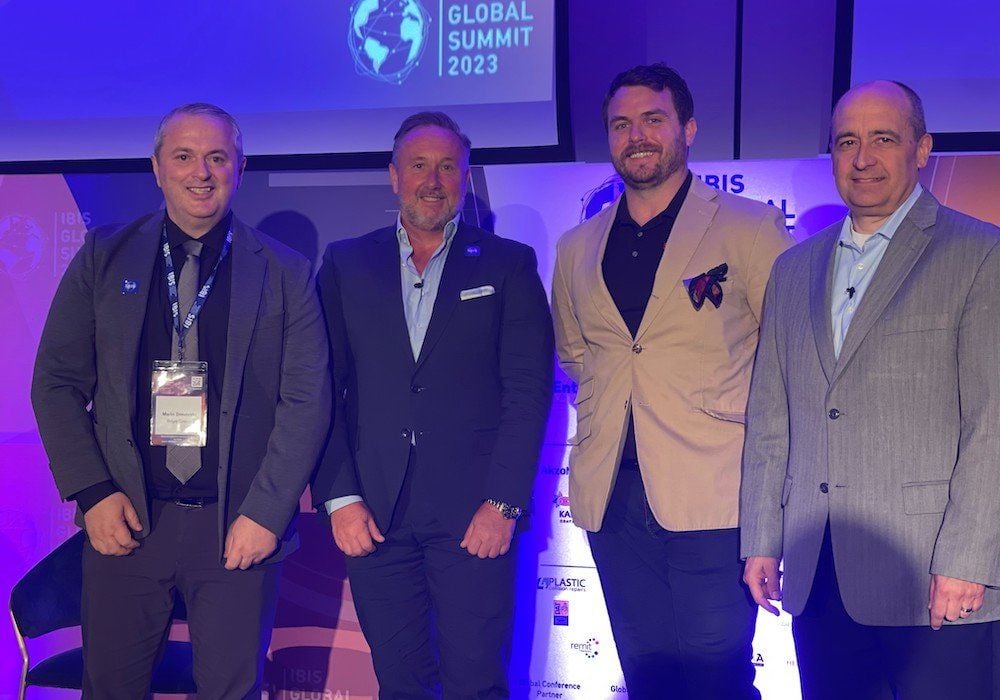
Charles R. Goulding and Preeti Sulibhavi take a look at the new 3D Printing Auto Repair Tasking Force what its implementation could mean for the auto part industry.
Up until now, 3D printing for auto parts and autobody parts has only had limited applications.
At the major manufacturer OEM level Ford, BMW and Porsche have made well-publicized progress. Collectors who are typically well-to-do, including Jay Leno, have been able print some unavailable parts.
Formula One, with its large resources and high-performance needs, has achieved some great results.
However, the current mainstream auto market has a dire need for 3D printed solutions for both regular auto repair and auto body parts. The new car market remains supply-constrained, used car prices remain high and repair and replacement part costs are at an all-time high. New larger 3D printers can be an effective way to circumvent this problem.
In April 2023, the International Bodyshop Industry Symposium (IBIS) held a USA 2023 Trade Conference in Nashville, Tennessee where it announced it was launching a “3D Printing in Auto Repair Task Force”. At the helm of the task force will be Harold Sears, who has over two decades of 3D printing experience at Ford Motors.
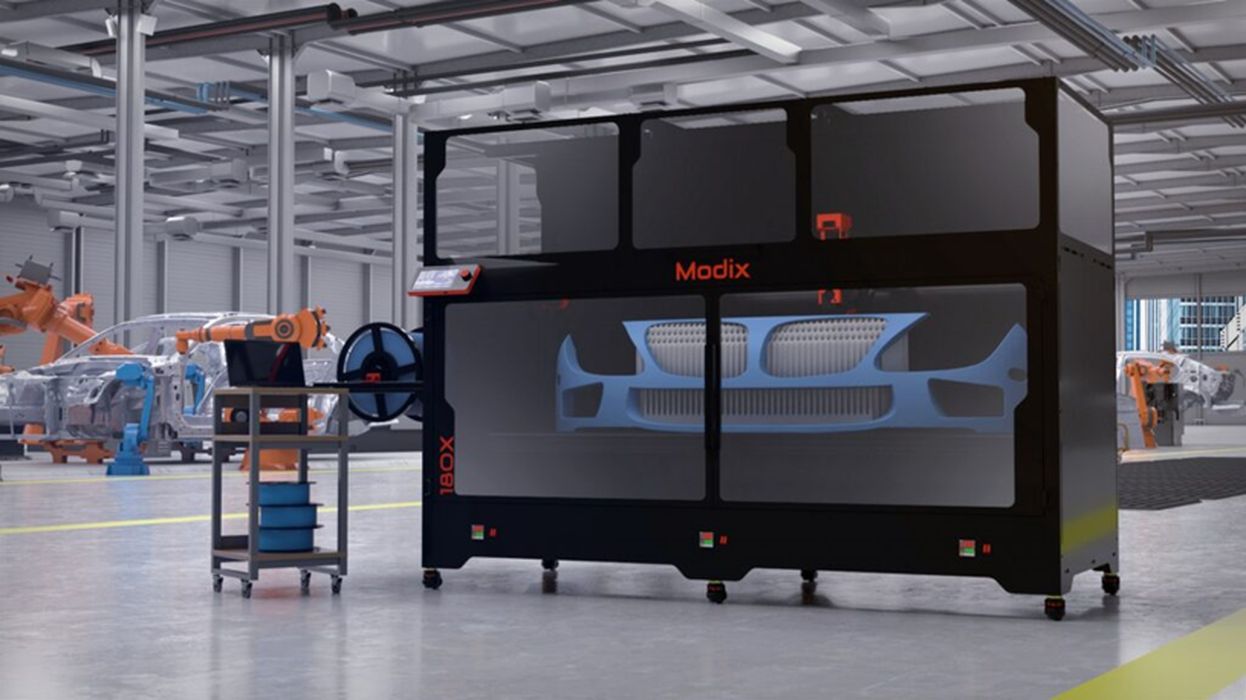
Sears is quoted as saying, “We are also seeking to provide a secondary solution for OEMs or parts suppliers who might need smaller part runs that are more cost-effective than traditional manufacturing and printed in the region where there is demand.”
Sears also indicated that this could include using 3D printing to create replacement parts, tools, and other components, as well as using the technology to improve the design and manufacturing of existing parts. Additionally, it could be used to highlight any issues regarding suppliers or body shops using poor quality printed parts that are not designed for end-use application and thus can break down and cause the part to fail over time.
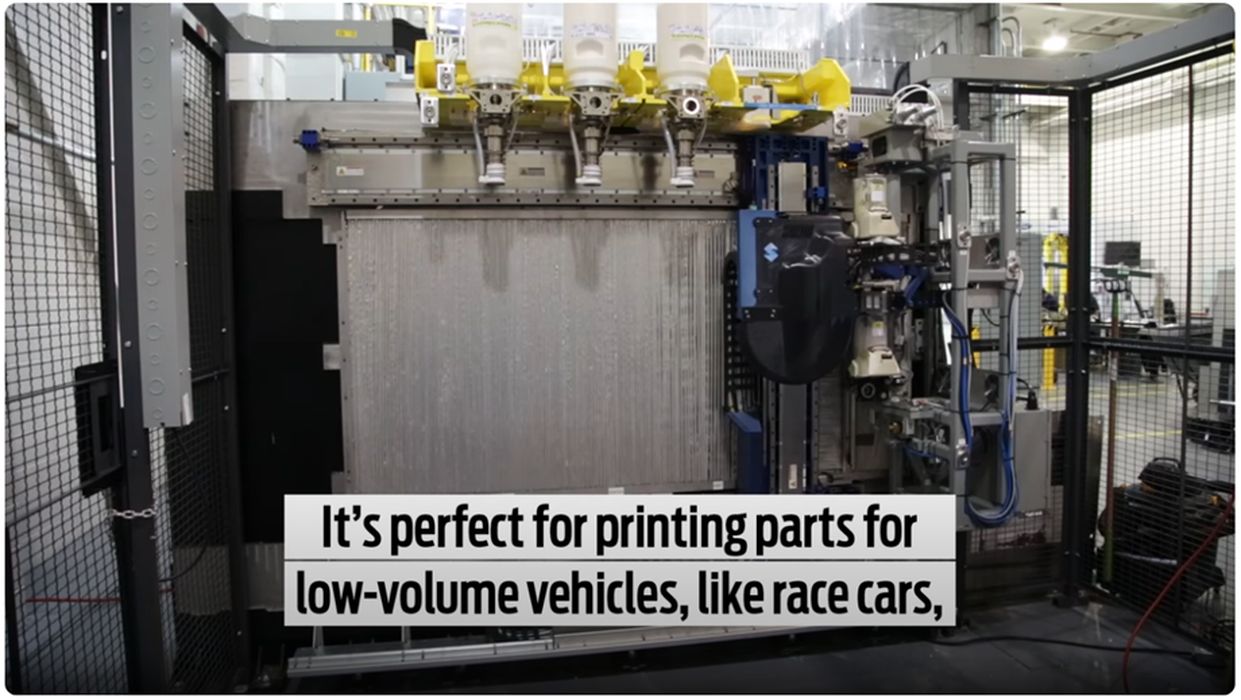
The goal is to research the use of 3D printing in automotive and collision repair and explore the potential for custom parts and components unavailable through OEM channels. All this while stopping the unregulated 3D printing of replacement parts that can be of poorer quality and comprised of low-grade materials.
In fact, Würth Additive Group joined the task force with the hopes of revolutionizing collision repair processes and enabling the use of 3D printed parts via Wurth’s advanced digital inventory management program, DIS3DP.
Würth, NA’s CEO, AJ Strandquist is quoted as saying, “I am honored to be included in the groundbreaking initiatives of this task force and for the future collaboration of this thought leadership.
He went on to say, “I appreciate the Würth organization for supporting the vision of digital infrastructure, and Würth Additive Group’s unwavering commitment to these efforts. I look forward to working with my new colleagues on the task force to take the next steps in implementing additive manufacturing best practices, integrating digital inventory management solutions, and helping to shape the transformation of the automotive repair industry through the innovations of 3D printing.”
Auto Parts and 3D Printing
Auto accessories are particularly good candidates for 3D printing integration. For starters, cosmetic customization parts such as rear-view mirrors, cup holders, custom frames, and phone stands are the easiest category to start with. Other small parts like lids, valves, and specialized auto components are another category of auto parts that are well-suited for 3D printing.
The Research & Development Tax Credit
The now permanent Research and Development (R&D) Tax Credit is available for companies developing new or improved products, processes and/or software.
3D printing can help boost a company’s R&D Tax Credits. Wages for technical employees creating, testing and revising 3D printed prototypes can be included as a percentage of eligible time spent for the R&D Tax Credit. Similarly, when used as a method of improving a process, time spent integrating 3D printing hardware and software counts as an eligible activity. Lastly, when used for modeling and preproduction, the costs of filaments consumed during the development process may also be recovered.
Whether it is used for creating and testing prototypes or for final production, 3D printing is a great indicator that R&D Credit eligible activities are taking place. Companies implementing this technology at any point should consider taking advantage of R&D Tax Credits.
Conclusion
The IBIS initiative is coming at the ideal time and could present great results. We have seen industry-focused consortiums accomplish major change in rail with the European Rail and in lighting with the Rensselaer Polytechnic Institute lighting consortium. Auto repair and autobody parts have the potential to be one of the largest volume 3D printing applications.