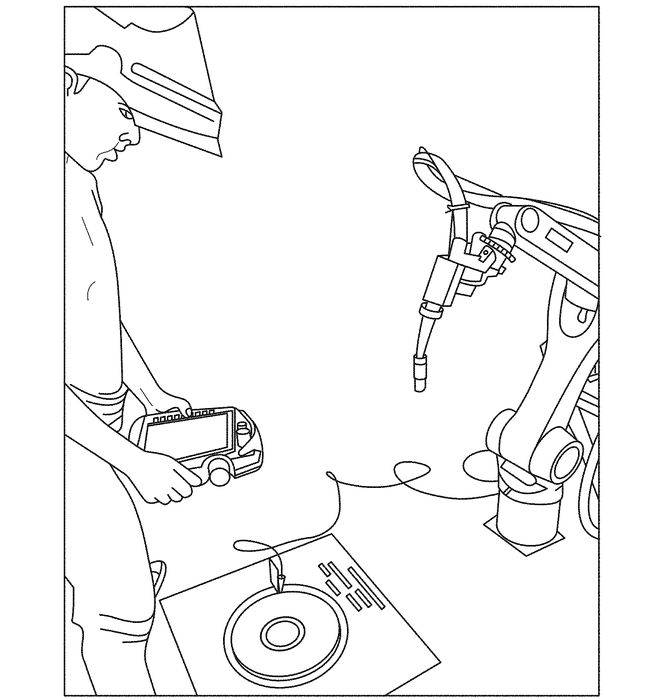
Relativity Space owns what could become a key patent for additive manufacturing.
The California startup is well-known for their progress in developing a fully 3D printed orbital rocket. Instead of merely 3D printing the engines as their competitors do, they’re literally 3D printing the entire rocket, from top to bottom.
They can do so with the assistance of their proprietary in-house robotic DED 3D printer, Stargate. This device sports a welding-style deposition head on the end of a robotic arm, which swings around to gradually build up the metal spaceship.
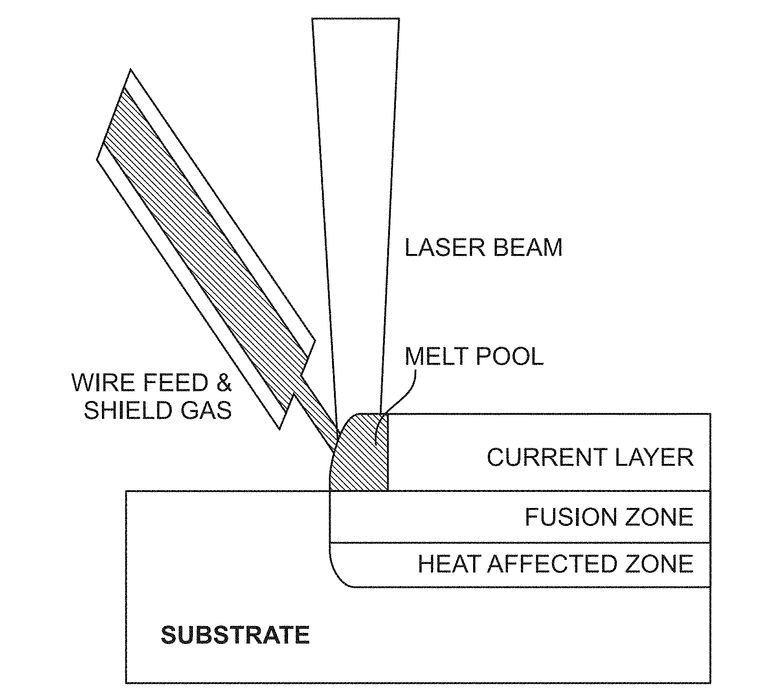
The company has been in the news lately, not because they are nearing the first launch of their initial rocket, the Terra-1, but because they announced a much larger version, the Terra-R. This vehicle is about the same size as market leader SpaceX’s Falcon 9, and should be cheaper to operate as Terra-R is entirely reusable.
Fabbaloo reader Tiago tipped us to one of the company’s patents, and it is quite interesting.
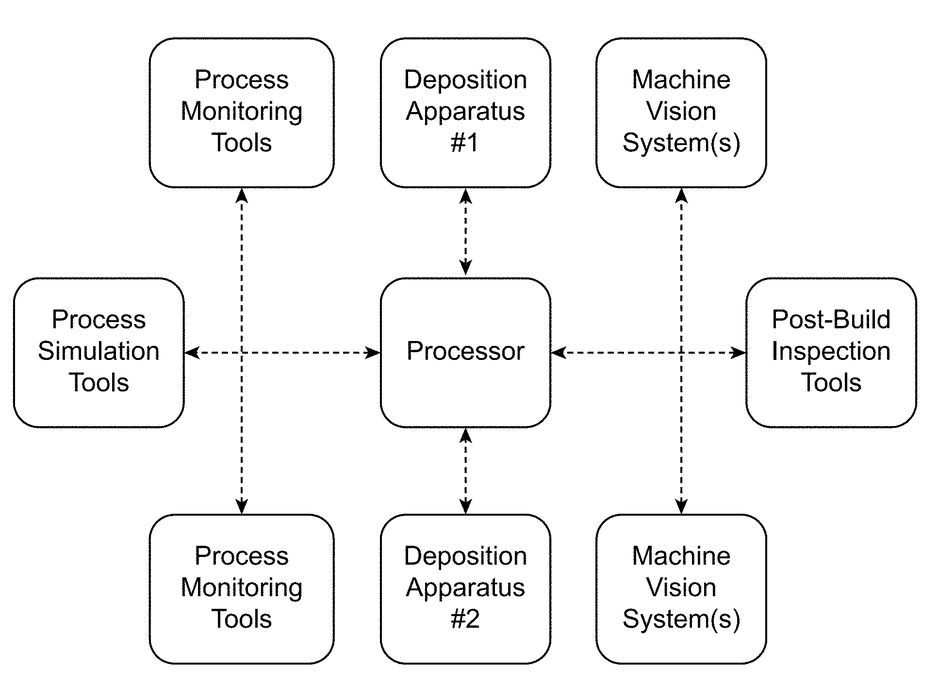
Patent US20180341248A1 is titled, “Real-time adaptive control of additive manufacturing processes using machine learning”, and it was awarded to Relativity Space in March of 2019, after being filed in May 2017.
Here is the background for this patent:
“Despite recent advances in the methods and apparatus used for various types of additive manufacturing, a need exists for methods that allow rapid optimization and adjustment of the process control parameters used in response to changes in process or environmental parameters, as well as for improving the quality of the parts that are produced. Methods and systems are disclosed for performing automated classification of object defects using machine learning algorithms. Also disclosed are methods and systems for performing real-time adaptive control of free form deposition or joining processes, including additive manufacturing or welding processes, to improve process yield, throughput, and quality.”
This makes a great deal of sense: 3D printing quality is always a concern, and Relativity Space has developed a method of achieving higher quality.
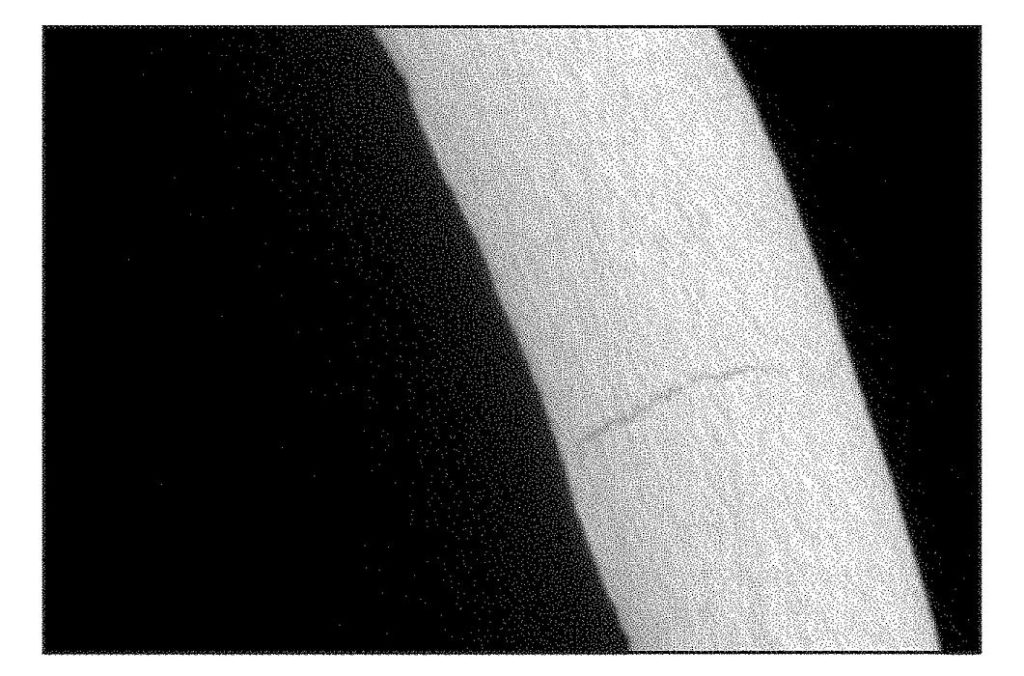
But I suspect there’s another reason behind this specific patent.
If we look at the specifications for their new Terra-R rocket, we find a vehicle that is 66m tall. That height is actually divided between two stages, so the maximum 3D print size for each segment would be around 30-40m. The lower stage is a bit larger than the orbital stage in their imagery.
Hold on, a 3D print that’s FORTY METERS TALL?
This suggests their Stargate system would have to reliably 3D print a 40m object. Imagine if, when completed, there was a flaw in the print at the 16m level.
Oh well, just print it again.
No, you cannot do that. These prints would take many days to complete and with the size the risk of failure increases proportionately. The larger the print, the bigger the potential fail. The delays and wastage of material would be immense, and so it’s clear Relativity Space has to take every possible step to minimize the possibility of print error.
Their approach seems to be at least partly with the technology described in this patent.
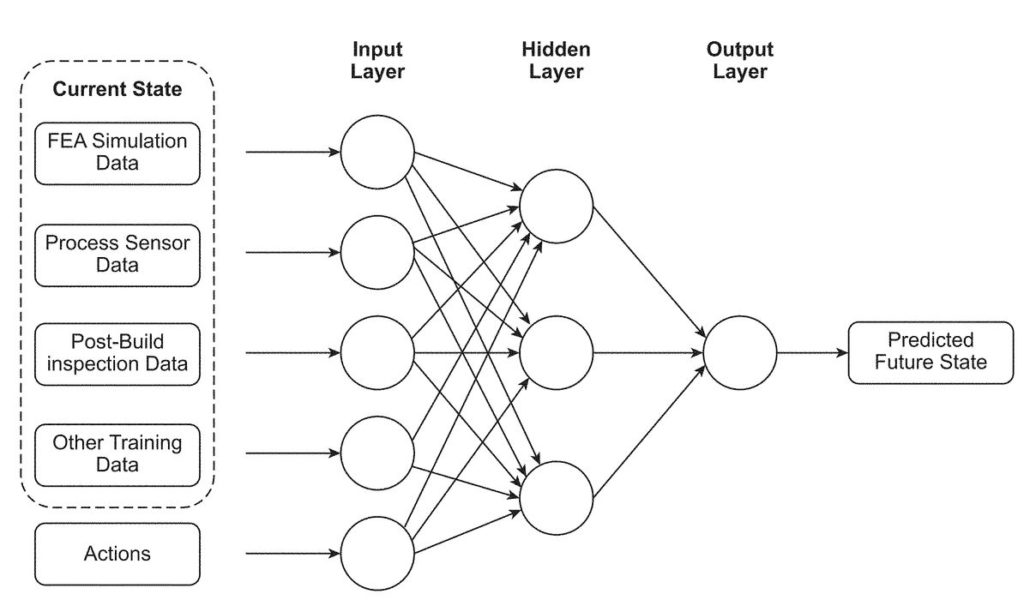
Their process seems to involve a database of simulation data that can identify deviations from the expected set of outcomes. This data is used in real time by a machine learning algorithm to detect issues and immediately tweak machine operational parameters to compensate.
This process should indeed reduce errors during 3D printing, hopefully to the point where any minimal deviations could be manually fixed up later with welding processes.
While Relativity Space’s Stargate system is a DED device, the patent mentions other 3D printing processes:
“In some embodiments, the free form deposition process or joining process is a stereolithography (SLA), digital light processing (DLP), fused deposition modeling (FDM), selective laser sintering (SLS), selective laser melting (SLM), or electronic beam melting (EBM), or welding process. In some embodiments, the free form deposition process is a liquid-to-solid free form deposition process. In some embodiments, the liquid-to-solid free form deposition process is a laser metal-wire deposition process. In some embodiments, the process simulation data is provided by performing finite element analysis (FEA), finite volume analysis (FVA), finite difference analysis (FDA), computational fluid dynamics (CFD) calculations, or any combination thereof.”
In other words, this machine learning patent for 3D printing covers off all of the major 3D printing processes and related techniques. It would appear that if a 3D printer manufacturer intends on using real time machine learning to increase print quality and reliability, they may have to speak with Relativity Space first.
Via Google Patents (Hat tip to Tiago)