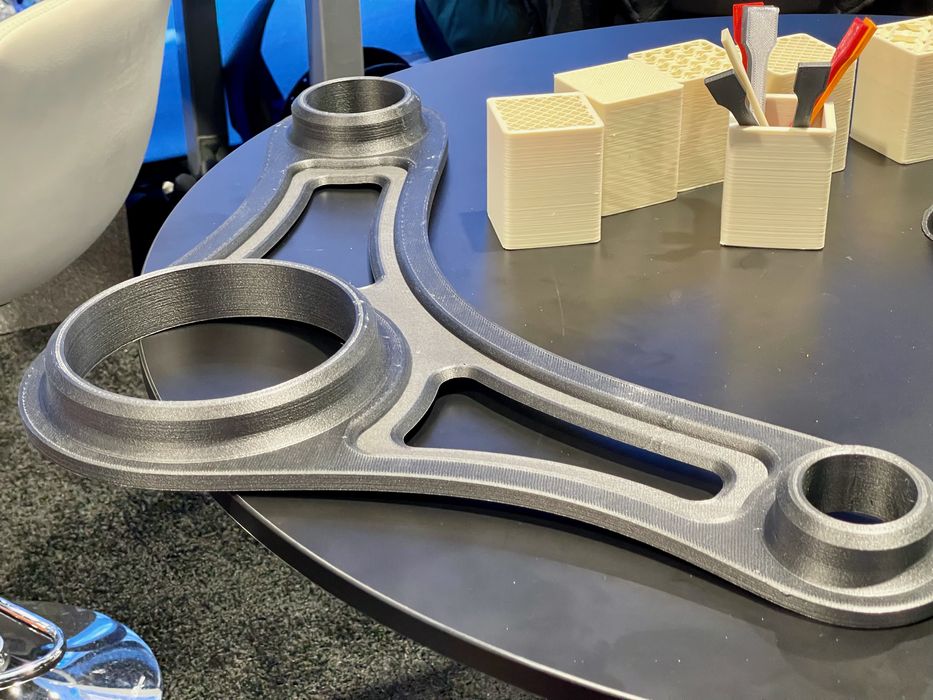
I learned about BigRep’s fleet management solution.
The Berlin-based company is well-known for its rather large 3D printers. They were among the first to market with a FFF device with a build volume exceeding on meter.
Along the way they pioneered their way through many of the problems that emerge when printing extremely large objects.
For example, larger objects tend to warp more due to the amplification of forces over longer lengths. This is of course problematic for large prints, and BigRep’s approach was initially to develop a unique material that did not warp as much.
Print times are also a problem on larger devices, with early BigRep machines taking literally weeks to complete jobs. To overcome this they developed advanced extrusion systems that could efficiently push more material through the hot ends to speed up printing.
They were one of the first to introduce larger-format filament spools, up to 8kg, which significantly reduced operator time on lengthy print jobs.
Now they’re facing another interesting challenge: fleet management.
It turns out that several of their clients actually have “fleets” of these very large 3D printers. What they’re making with them is not known to me, but it’s likely large objects such as marine or furniture prototypes.
Operating a single machine is one thing, but operating a fleet of machines is quite another. Operators must run between machines removing prints, swapping spools, starting jobs, etc. It gets even more complex when there are print failures or differing materials between machines in the fleet.
BigRep recognized this and introduced “BigRep Connect”, a software service that is able to simplify much of this effort.
BigRep Connect uses standard networking to bring together the status of all machines in the fleet to a single management point. From there the operator can see at a glance the current state of the printers, and can take appropriate actions.
Even better, BigRep Connect works remotely: it’s possible to upload and start jobs away from the machine — assuming the print plate is cleared. Monitoring is also possible offsite, meaning an operator can keep in touch 24 hours a day with the fleet.
As print jobs are dispatched to the fleet and completed, BigRep Connect collects data on everything happening. These are then presented in analytics form for the operator to review.
It’s possible to examine the analytics to, for example, see if there are issues with a particular machine, or develop a more efficient workflow, or identify issues with a specific material brand. Material usage patterns can be generated, allowing more efficient buying strategies to take place in the future.
To make use of BigRep Connect, a “compatible” set of machines must be present. From the look of their list, it would seem that most of their current product line will work with the software, including PRO, ONE and STUDIO models.
Fleet management is a complex issue that requires solutions that address human workflows found when using additive manufacturing. There are an increasing number of 3D printer manufacturers that are integrating this type of management solution into their equipment, and BigRep is one of them.
Via BigRep