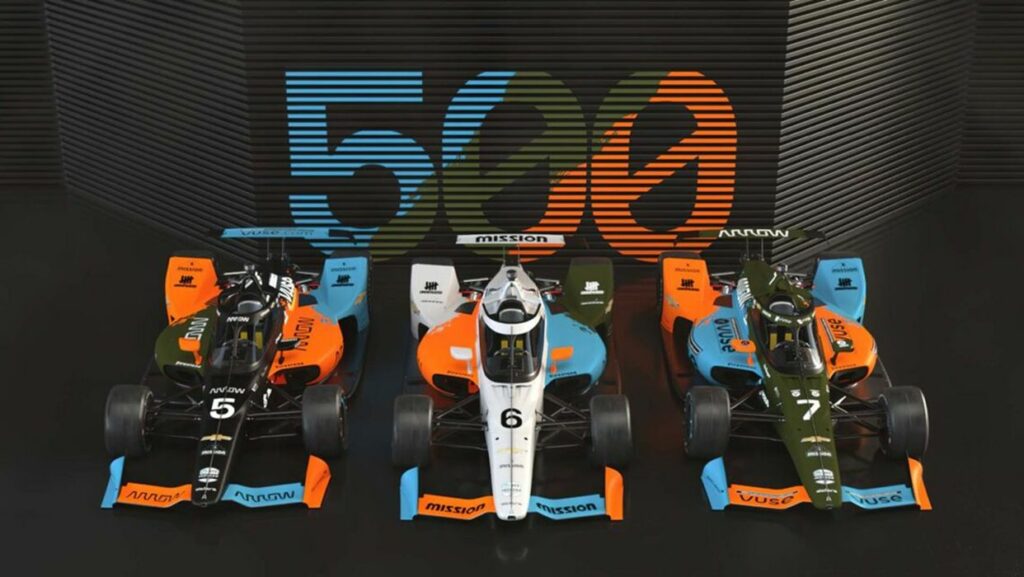
Charles R. Goulding and Warren Buzzell Jr. look at use of Stratasys equipment by racing teams.
Members from our firm recently had the opportunity to attend the Experience Stratasys: Manufacturing event. The event aimed to highlight Stratasys’ newly developed and improved 3D printing machines, technology, and materials, as well as areas where the technology has been integrated for commercial use.
For example, Formula One racing team Arrow McLaren SP showcased their use of Stratasys’ 3D printing technology and its applications–also illustrated in our article “Formula One Racing Teams and 3D Printing Activities: Driven To Be The Best”.
Stratasys showcased four 3D printers throughout the event: F370 CR & F190 CR, Origin One, Neo800, and H350. The design and development of these printers enable manufacturers and designers to bring cost-efficiency to manufacturing, sustainability to supply chains, and flexibility to the factory floor.
The Showcased 3D Printers
The F370 CR and F190 CR 3D printers are two of Stratasys’ new and improved fused deposition modeling (FDM) printers. These printers utilize production-grade thermoplastics to build durable, strong, and dimensionally stable parts. The integration of the new printers will enable manufacturers to produce accurate and reliable parts with a multitude of different materials, including nylon, glass deposits, ASA, and various ABS materials.
The F370 CR and F190 CR are similar in design, where the key differences are highlighted in the build tray size, material delivery, and material usability. With that being said, the F370 CR has slightly more capabilities and robustness than its smaller counterpart.
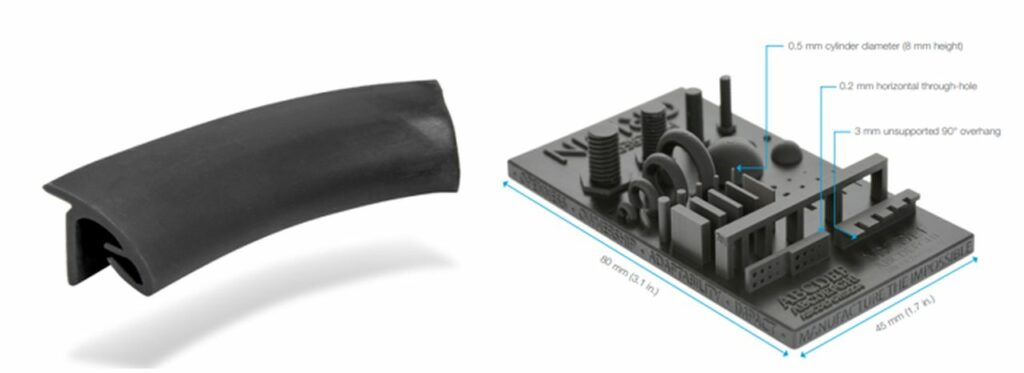
The Stratasys Origin One is a manufacturing-grade printer that will enable the mass production of complex end-use parts. The Origin One utilizes Programmable Photopolymerization technology to produce high-quality and detailed parts in no time. Photopolymerization is a form of Digital Light Processing (DLP), where a vat of photopolymer resin is cured layer-by-layer on the platform with a high-resolution projector.
The Origin One has a simple and fast post-processing workflow that emphasizes minimal facility requirements and makes scaled production feasible. The Origin One expands upon flexible production capabilities by enabling the manufacturing of robust and complex products with short lead times.
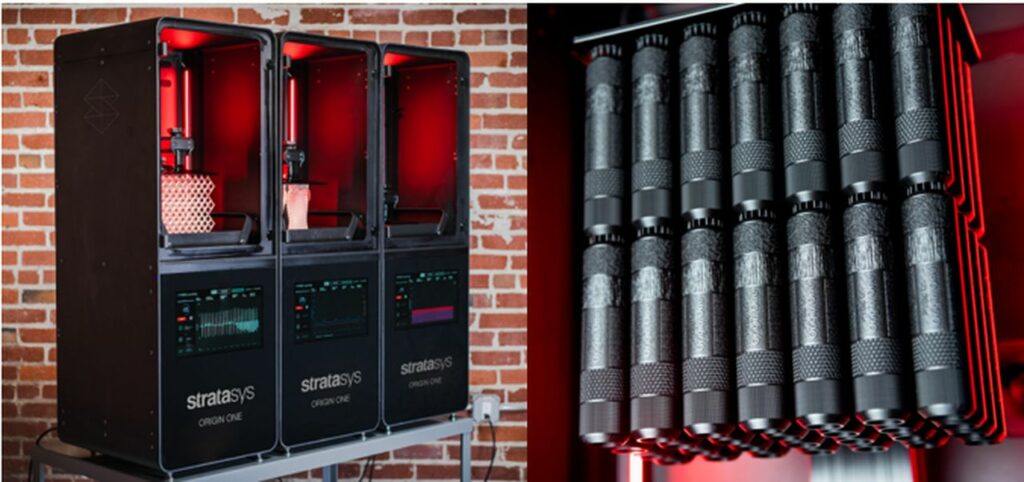
The Neo800 stereolithography 3D printer was also showcased at the event. The printer utilizes an open resin system to develop detailed end-use production parts. The printer was designed for manufacturing specialized tooling and investment casting. The Neo800 is capable of producing large parts with its 53.2 x 64.2 x 90.6 build platform. Furthermore, it is renowned for its reliability, rapid tooling, and master patterns.
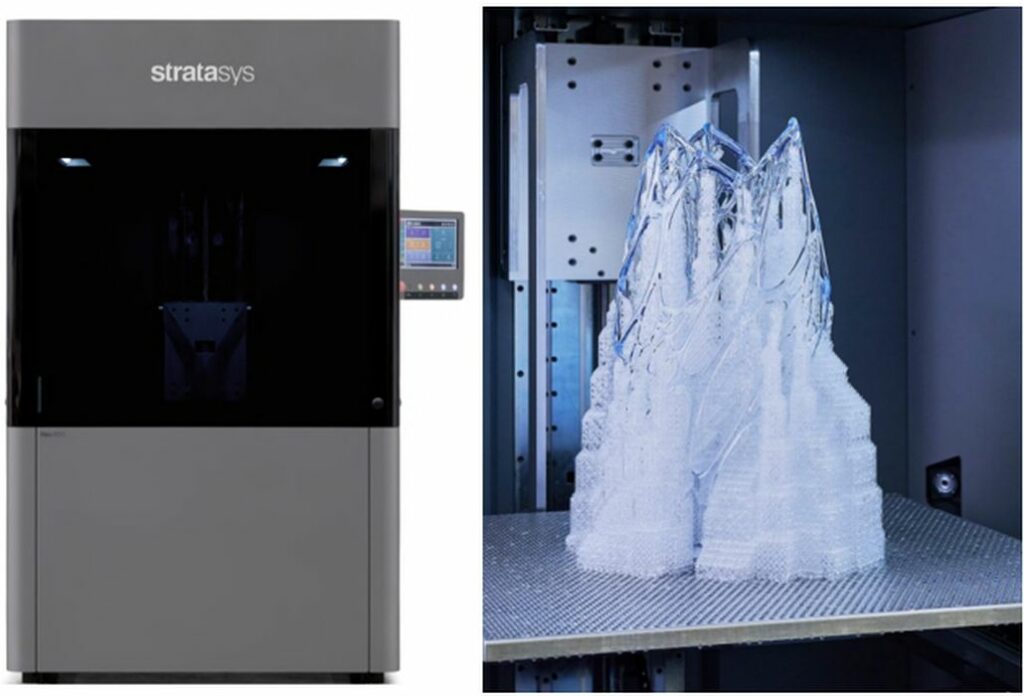
The last printer shown at the event was the H350, powered by selection absorption fusion (SAF) technology. The printer uses powder-based material and requires half the fluid as competitor printers to develop high-volume parts with accuracy and repeatability. The H350 utilizes this technology to create inexpensive and reliable products with consistent performance.
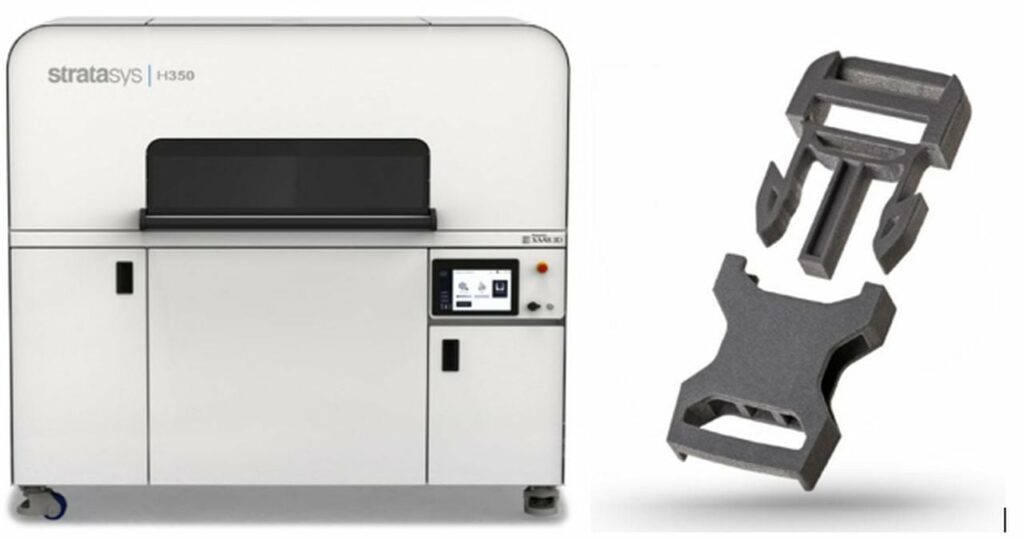
Arrow McLaren SP: 3D Printing in Formula One Racing
3D printing technology has advanced from prototype testing to validate the feasibility of designs to end-use part customization and rapid manufacturing. At the Stratasys event, developers from Arrow McLaren SP emphasized how 3D printing enables them to print composite materials efficiently and effectively–drastically reducing manufacturing lead time. They also discussed how they utilize FDM printers and nylon 12 CF material to develop end-use car accessories and parts for electronic boxes, sensors, etc.
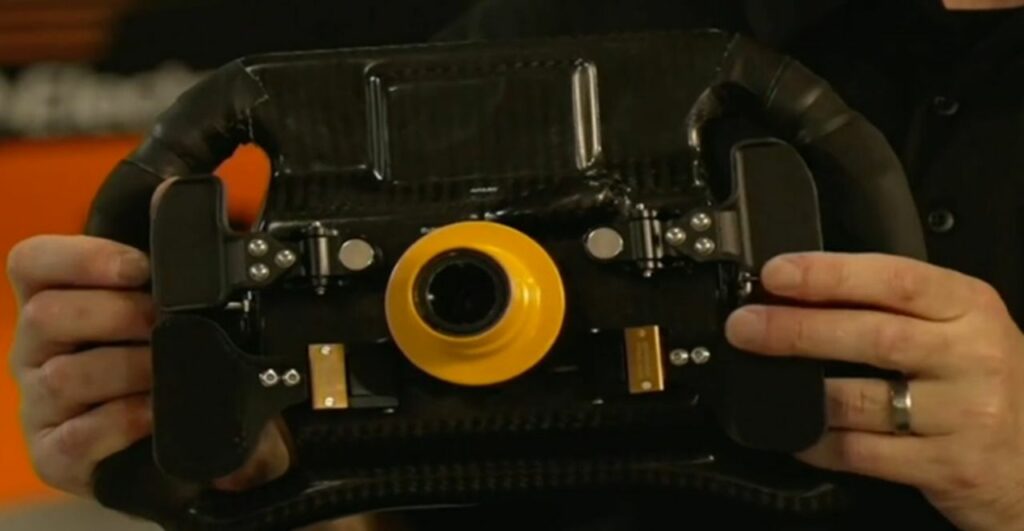
3D printing enables them to quickly develop custom racer-specific parts that are both ergonomic and durable. The team at Arrow McLaren showcased their 3D printing applications for creating steering wheel clutches, brake duct fans, and driver cooling fans. 3D printing enables rapid prototyping, testing, and the appropriate redesign and rapid development of parts to meet the team’s needs, even if those needs are required with little lead time.
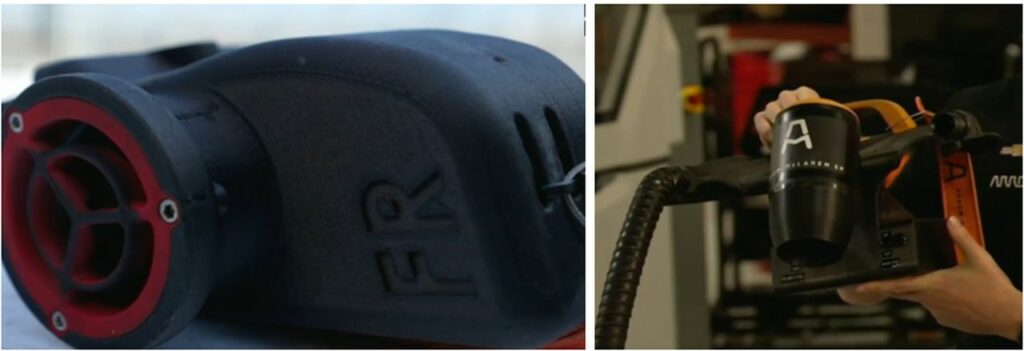
Arrow McLaren has been using 3D printing technology over the past few years to gain a competitive advantage against its competitors. Jon FlackPresident of Arrow SPMstated in an article, “Stratasys is an elite partner, allowing us to transform typical manufacturing processes with 3D printing by learning on race day and implementing by the following weekend.” I believe it is safe to assume that the company plans to utilize 3D printing in more innovative ways as the technology continues to improve in the near future. Arrow McLaren intends to purchase and integrate the new F190 CR and F370 CR printers into their workshops to continue manufacturing custom end-use parts for their vehicles and drivers.
The Research & Development Tax Credit
The now permanent Research and Development (R&D) Tax Credit is available for companies developing new or improved products, processes and/or software.
3D printing can help boost a company’s R&D Tax Credits. For example, wages for technical employees creating, testing, and revising 3D printed prototypes can be included as a percentage of eligible time spent for the R&D Tax Credit. Similarly, when used as a method of improving a process, time spent integrating 3D printing hardware and software counts as an eligible activity. Lastly, when used for modeling and preproduction, the costs of filaments consumed during the development process may also be recovered.
Whether it is used for creating and testing prototypes or for final production, 3D printing is a great indicator that R&D Credit eligible activities are taking place. Therefore, companies implementing this technology at any point should consider taking advantage of R&D Tax Credits.
The Race to 3D Printing End-Use Integration
Time has shown that as 3D printing technologies improve and their capabilities expand, so has their application. This direct relationship between ameliorating 3D printing inconsistencies has led to a more robust use of the technology. The technology that was initially developed for rapid prototyping and the testing of small-scale models is now being used to create large-scale and end-use parts with production-grade durability and performance.
Over the past few years 3D printing technology has made its way into Formula One racing, where teams (such as Arrow McLaren SP) have used the technology to produce durable and driver-specific custom parts. The future of 3D printing and Formula One racing is bright, and we may begin seeing more use of the technology for end-use applications as it improves over time.