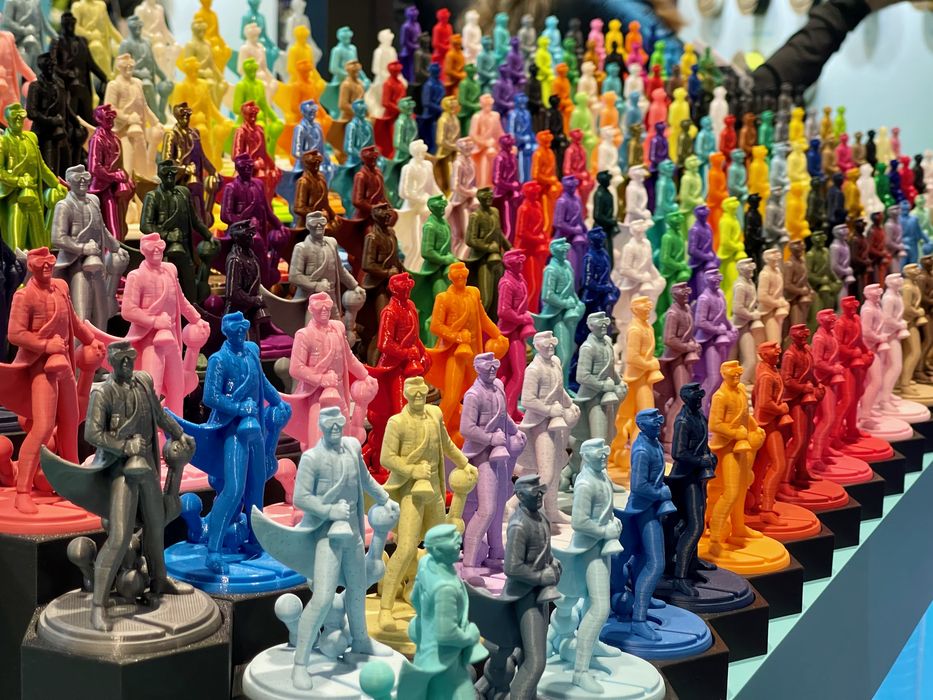
We had a chat with Polymaker to learn more about their latest developments.
This materials provider has long held the reins as a frontrunner in the 3D printing universe, offering a cornucopia of unique, functional products for both industrial and personal use.
Just take a peek at the mini rainbow of PLA colors they’ve got on offer at top. With a mind-blowing 173 variants under their belt, they’re likely to have the most diverse palette of any provider.
A Symphony of Colors and More
Sure, colors might be a secondary concern for industrial 3D printer operators, but for others, it’s a pivotal feature. Polymaker reveals these color options are selling very well, spurring them to develop even more variants. They’re not just playing around with colors. They’ve introduced a couple of color-changing materials that switch hues based on the ambient temperature.
Polymaker’s secret weapon? Their Discord site. That’s where users can pitch in with suggestions for potential new products.
While PLA maintains its throne as their best-selling material, the runner-up might come as a surprise: it’s ASA, not ABS. Essentially a more robust version of ABS, ASA’s resistance to ultraviolet light makes it a winner for outdoor applications.
Here’s hoping this sparks a shift away from ABS.
A Glimpse into Production Efficiency and Sustainability
Polymaker has taken a leap towards efficiency, transitioning to a fully automated production line for filament manufacturing.
One intriguing facet of their production process is their spool design. In a nod to sustainability, they long ago ditched plastic spools for cardboard equivalents. Recently, they’ve slimmed down the thickness while ensuring they’re still sturdy enough for use. A lighter spool equals lower shipping costs and a smaller carbon footprint.
The company has also devoted time to perfecting how the filament attaches to the spool.
Rethinking Filament Attachment
Most filament providers simply hook the end into a hole on the hub and then wind up the rest. This works just fine until you’re printing to the end of the filament. That’s when the “hook” gets pulled into the 3D printer, causing a snag and halting the print. Worse still, this usually happens before the filament-out detector kicks in, resulting in a print failure.
Polymaker’s solution? They’ve revamped their attachment method. Instead of a hook, they insert a long straight segment of filament into the hub via a small hole. This simple tweak eliminates the dreaded “hook problem”.
It’s high time more filament producers adopt this approach. It would solve a major issue for many.
Polymaker certainly seems to be forging ahead in their filament innovation journey. And that’s music to our ears.
Via Polymaker