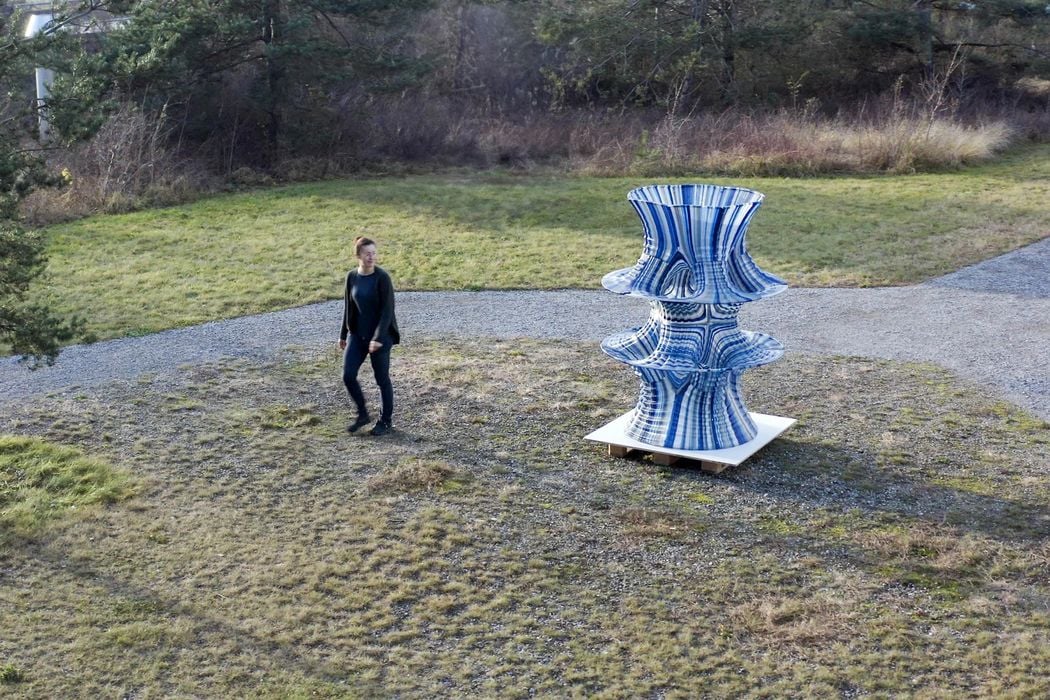
Researchers at ETH Zurich have developed a unique way to 3D print large structures using mathematics and robotics.
3D printing large structures in polymer has long been a thing, but here there’s something different at play. The researchers sought a way to 3D print these structures in a more efficient manner.
Their solution first used mathematics, where they were inspired by something called the “Costa Minimal Surface”. This is a curved surface described by a specific family of equations. Wikipedia explains:
“The Costa surface evolves from a torus, which is deformed until the planar end becomes catenoidal. Defining these surfaces on rectangular tori of arbitrary dimensions yields the Costa surface. Its discovery triggered research and discovery into several new surfaces and open conjectures in topology.”
The researchers leveraged this surface equation to generate unique 3D models for printing. They say that the resulting models have “remarkable structural properties”, which is not fully explained.
However, I suspect that it has to do with the strength to weight ratio for the structure, which would be advantageous for larger structural objects. For example, they tweaked the curve by introducing repeating undulations that would create additional strength.
The second part of their project was to print these models.
Their approach was to use a non-planar 3D printing method using a robotic arm equipped with a pellet extrusion toolhead. In this video you can see how this works:
You’ll notice that the robot is not laying down flat layers, but instead is varying its Z-position throughout the job. This enables more efficient 3D printing, in that the need for support structures can be significantly reduced, or even eliminated in some cases.
The other benefit of this approach is that they could orient the non-planar layer lines in a way that provided greater part strength. This is a benefit that cannot easily be achieved with planar 3D printing methods.
To prove out the concept, the researchers produced a sample structure using these approaches. They printed 40 separate parts, which were assembled using screws. This allowed them to disassemble and relocate the structure when necessary.
In all, 120kg of PETG pellets were used to produce the 2m structure. Printing wasn’t fast, however, as the project consumed three weeks of robotic 3D printing, followed by 140 hours of machining to smooth out required surfaces.
Andrei Jipa]
While this work is research at this point, it suggests we may see important developments in the future for free-form structures. These designs do not just look unusual; they are functionally better due to improved engineering properties.
That could be of significant importance for those building large structures using robotic 3D printing systems: construction 3D printing companies.
Currently these companies build more or less square or slightly curved buildings, but what if they could leverage the knowledge from this research and make their buildings more efficient? What might buildings look like if that happened?
Via ETH Zurich and ScienceDirect