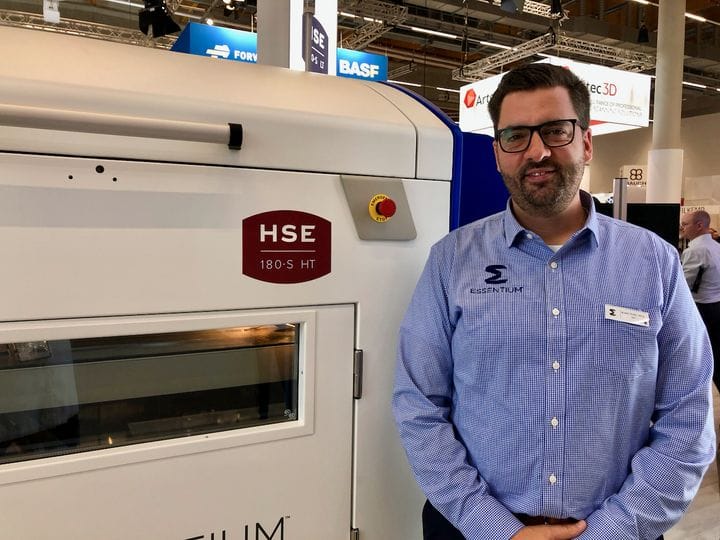
Essentium surprised with the announcement that they are developing a metal 3D printing system.
The Texas-based company has thus far been successful producing advanced polymer-based 3D printing systems for industry. Their HSE series, which inherited technology from the PCB manufacturing industry, is perhaps the fastest FFF extrusion system I’ve yet seen.
The new metal process has been developed by the company’s EssentiumX team, a project development team that focuses on special projects. This team was announced last March, and it appears the new metal process must have been their prime focus over that period.
Essentium Chief Development Officer Elisa Teipel said:
“By leveraging our materials-first heritage, we are creating a unique manufacturing method. Our metal AM platform will deliver improved throughput for high part quality, and it will have the potential for broad-scale use in major industrial markets, including automotive, aerospace and defense. We expect our metal AM platform to empower manufacturers to innovate faster and stay ahead despite unprecedented challenges in today’s markets.”
What exactly is this new process? We don’t know much at all at this stage, and we even don’t know the name of the process. There are some clues in the Essentium announcement, however:
- The process “will be integrated with the Essentium High Speed Extrusion (HSE) technology”
- The technology is “supported by five patents to date with three additional patents pending”
- The process will “provide energy-efficient deposition, decrease porosity, and minimize warpage during a build”
- It will produce parts comparable to castings and forgings with minimal post-processing required
The claim that the new metal process will be integrated into their existing HSE process suggests that the metal process will be filament-based. This style of metal 3D printing has been done previously, where specialized filaments containing a high ratio of metal powder are extruded, and the final object is sintered. This burns off the polymer binder and leaves only a metal object. A popular material for this approach has been BASF’s Ultrafuse.
“Minimize warpage” could also suggest the FFF approach, as that style does not involve high heat that often generates warping in laser-based metal 3D printers.
Since Essentium mentioned that several patents cover the new process, I undertook a short search of the patent databases to see if there was any patents that might describe this new process or elements of it.
Unfortunately, there does not seem to be any, as Essentium’s publicly available patents as of this writing don’t describe anything other than their FFF systems. This also suggests that either the new metal process is indeed a variation of their existing HSE approach, or is something so new that the patents have not been made public yet.
There is really very little information about this mysterious new process available at this time, and thus the question of the announcement’s timing comes up. Why announce this at this stage?
One reason could be that metal 3D printing is, at the moment, one of the most profitable areas of 3D printing. Many different manufacturers have now “discovered” metal 3D printing and are using it competitively against each other. It is a very good idea for a 3D printer manufacturer to offer a metal option.
But another reason might have something to do with another recent announcement from Essentium: they are using a SPAC process to get on the NASDAQ exchange early next year. It may be that by announcing their intent to get into the metal business, they enhance the value of their company at an opportune moment: investors are now determining the company valuation in anticipation of the NASDAQ entry. Metal printing capability certainly won’t hurt that value.
Via Essentium