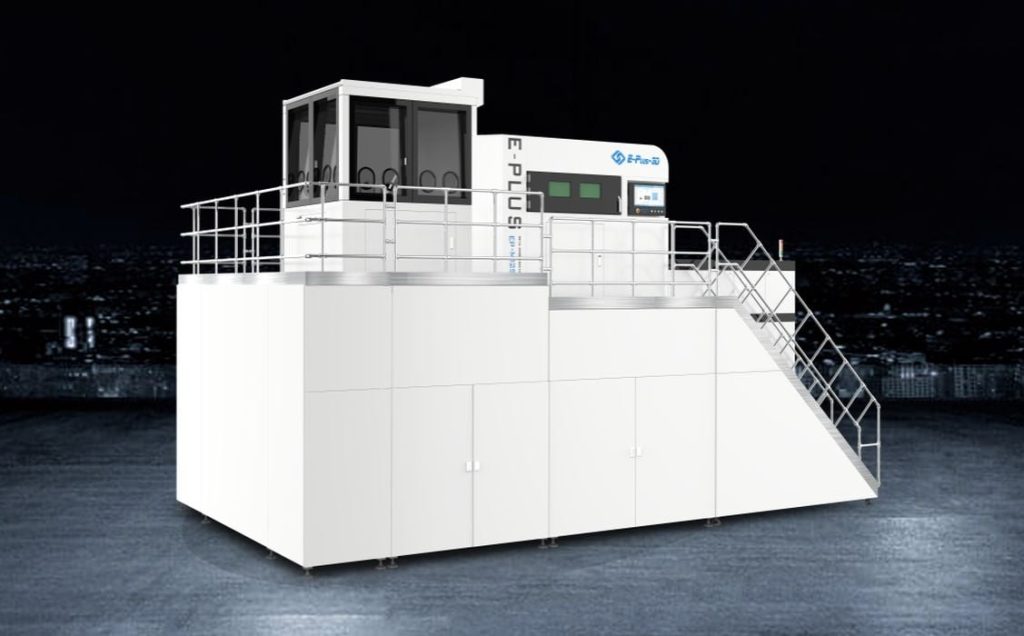
EPLUS 3D announced the availability of a massive metal 3D printer, the EP-M1250.
EPLUS 3D is a Chinese manufacturer of industrial 3D printers, and has been in operation since 2014. They offer a broad set of industrial 3D printers, including no less than ten different metal 3D printers, four SLS solutions printing in polymers & wax/sand, and three SLA models for precision resin 3D printing.
Their latest announcement is the truly enormous EP-M1250 device, a metal 3D printer with a huge build volume of 1258 x 1258 x 1450 mm. This is certainly one of the largest build volumes available today for metal LPBF equipment.
With such a large build volume, one might suspect that print durations could be extraordinarily long on the EP-M1250. However, EPLUS 3D has mitigated that by including multiple lasers in the system. Do they use a quad-laser configuration as is found in some other advanced equipment? No, they use NINE lasers!
The nine lasers are arranged in a 3 x 3 array, where each laser appears to work within its respective zone on the build plate. The lasers can operate simultaneously, and thus you can theoretically expect print times to decrease by up to 9X.
The result of this multi-laser configuration is that the EP-M1250 is able to fuse up to 240 cubic centimeters of metal powder per hour. EPLUS 3D said the density achieved is up to 99.9% with only a “<5% deviation in mechanical properties”.
Apparently their proprietary software allows operators to independently tune each of the nine print zones with unique parameters. This may be quite useful if the EP-M1250 is used to print multiple objects in the same job: each object could have different print parameters.
While the huge build volume on this machine can indeed permit printing of very large objects well in excess of 1m, there is also the possibility of printing huge volumes of smaller objects at reasonable throughput levels.
One issue that could arise in a nine-laser configuration is an abundance of smoke and splatters. With all that energy flowing into the build chamber, something is going to happen. To counteract this, EPLUS 3D has redesigned the gas flow systems in the machine to ensure proper removal of smoke. EPLUS 3D said:
“To achieve homogeneous part properties all over the building platform, the gas flow has been optimized and redesigned to ensure efficient removal of smoke and splashes as well as achievement of uniform and consistent full size printing.”
As you might suspect, the EP-M1250 is a rather large device. In the image at top, note the presence of stairs for scale. The machine includes not only the printer itself, but also an attached filtration system and a post processing station.
The integrated post processing system seems correct to me because the weight of a completed build job would be truly enormous, and be quite difficult to move around. Imagine a cube of metal 1.25 meters on a side and you’ll quickly understand the problem.
The EP-M1250 will inevitably be compared with another popular multi-laser large-format metal 3D printer, the SLM Solutions NXG XII 600. That machine has twelve 1kW lasers, even more than the EP-M1250, but it has a substantially smaller build volume at “only” 600 x 600 x 600 mm.
Could SLM Solutions compete with the size of the EP-M1250? Certainly they could build a machine similar to the NXG XII 600, but with a larger build volume. However, these machines are special and not many are sold each year. There would have to be a consistent and sufficient demand from customers for such a machine before SLM Solutions would commit resources to building one.
On the other hand, EPLUS 3D seems to have a large build volume metal 3D printer ready to go already. It may be that customers seeking the ability to build very large metal parts may start with EPLUS 3D simply because of the build volume availability.
Via EPLUS 3D