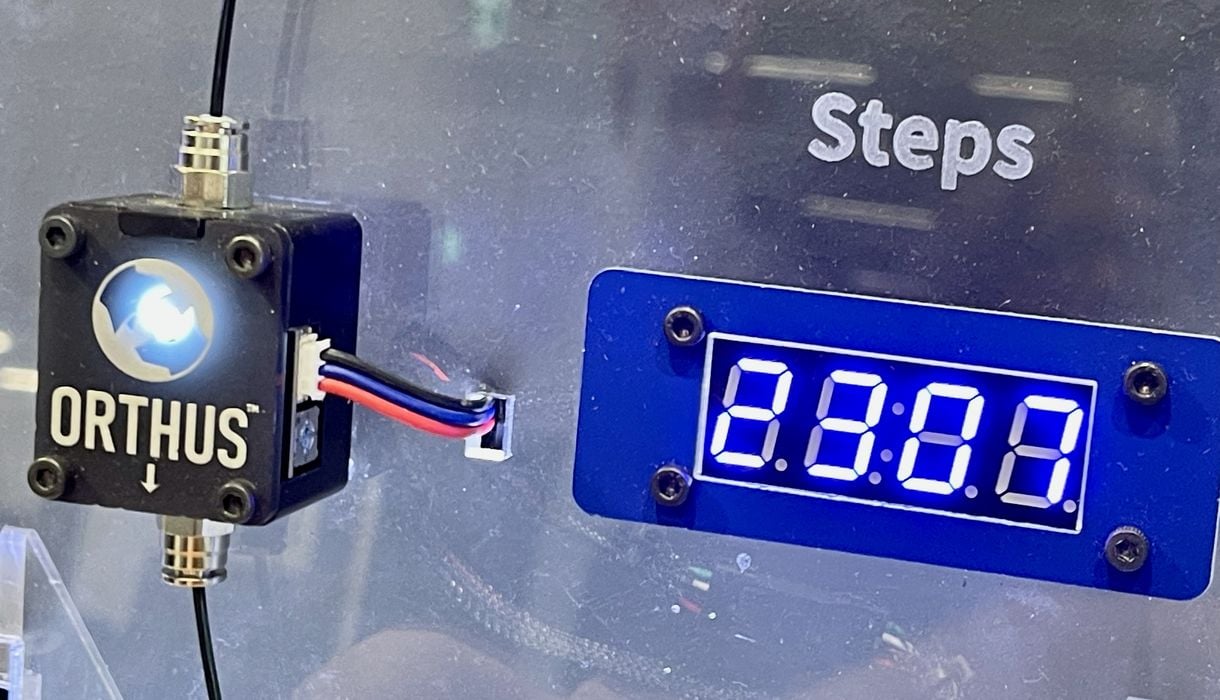
I had a look at two interesting 3D print sensors from Dyze Design.
Montreal-based Dyze Design has been making high-end 3D printer components for at least ten years. Their equipment is frequently installed on commercial gear, as well as specialized equipment.
Their primary products are high-flow extrusion systems for both pellet and filament formats. However, today we’re going to talk about a couple of their lesser-known products, two interesting sensors.
The first is the Orthus Filament Monitor, image at top.
Many 3D printers today include what’s often called a “filament run-out sensor”. These are simple devices that basically detect whether a filament is present or not. If it isn’t, then the assumption is that the spool has been emptied and it’s time for more material. Printing is paused and the operator is notified.
That’s all good, but there’s another common scenario: the filament has jammed. This could be a tangle in the spool, or perhaps some issue with the extruder or hot end. Either way, the job is in jeopardy, but the filament still sits in the run-out sensor. Those devices cannot detect this scenario.
The Orthus sensor actually does detect this situation.
It not only detects the presence of a filament, but also tracks its movement. Incredibly, it has a motion resolution of only 0.09mm, far smaller than you can actually see.
This means that while printing the motion of the filament is also monitored. If there’s a jamming issue, then the filament can stop moving, or even slow down. Both of these can be instantly detected by the Orthus sensor.
The result is that the operator will potentially be able to rescue the job before it fails completely. After a couple of big job rescues, it’s likely the Orthus has paid for itself.
The Orthus works with both 2.85 and 1.75 mm filaments, and has a blinking red LED to visually indicate motion.
I don’t understand why every FFF 3D printer doesn’t have this functionality. If your 3D printer doesn’t, then consider the Orthus as an accessory.
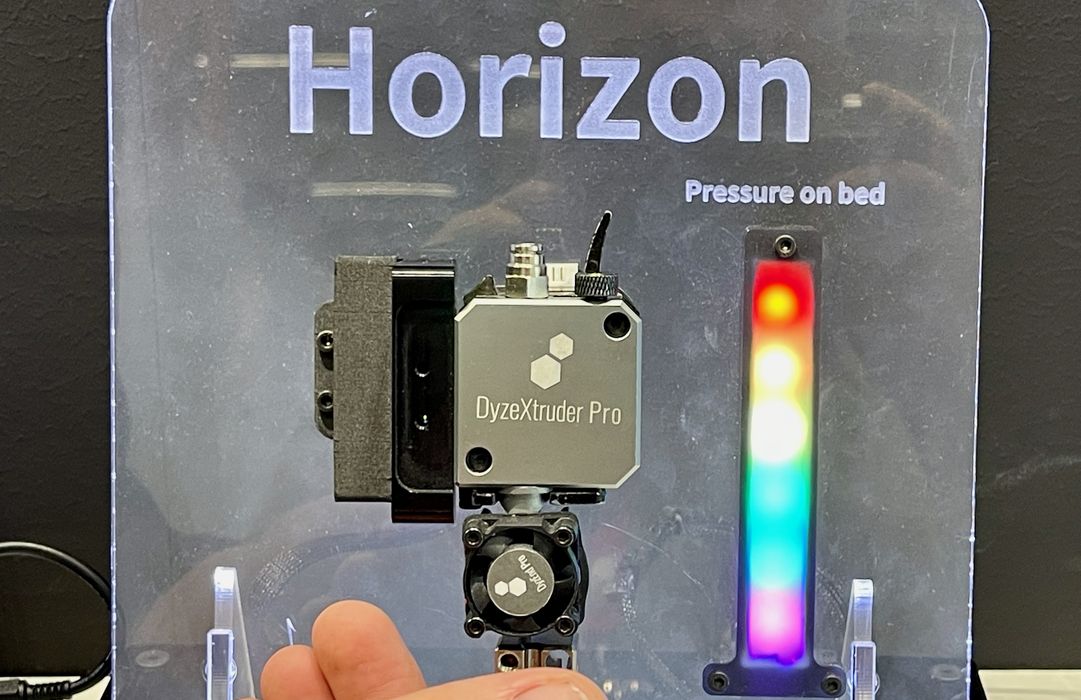
The second accessory is the Horizon, a bed sensor. The idea is that during leveling operations the 3D printer needs to know precisely where the tip of the nozzle touches the print surface. There are several different approaches to do this, including a mechanical sensor (like the BLTouch), or metal proximity sensors.
However, the Horizon works via pressure. It’s attached to the hot end and uses the actual nozzle tip as the end of the sensor. When the tip just barely touches the surface, the Horizon triggers.
Dyze Design lists the precision at less than 0.05mm. In fact, they also say:
“With an extremely stable printer, we are able to achieve a repeatability of 0.4μm.”
That’s quite impressive, and would be an easy add to many 3D printers that include less capable sensors — or some that don’t offer any at all.
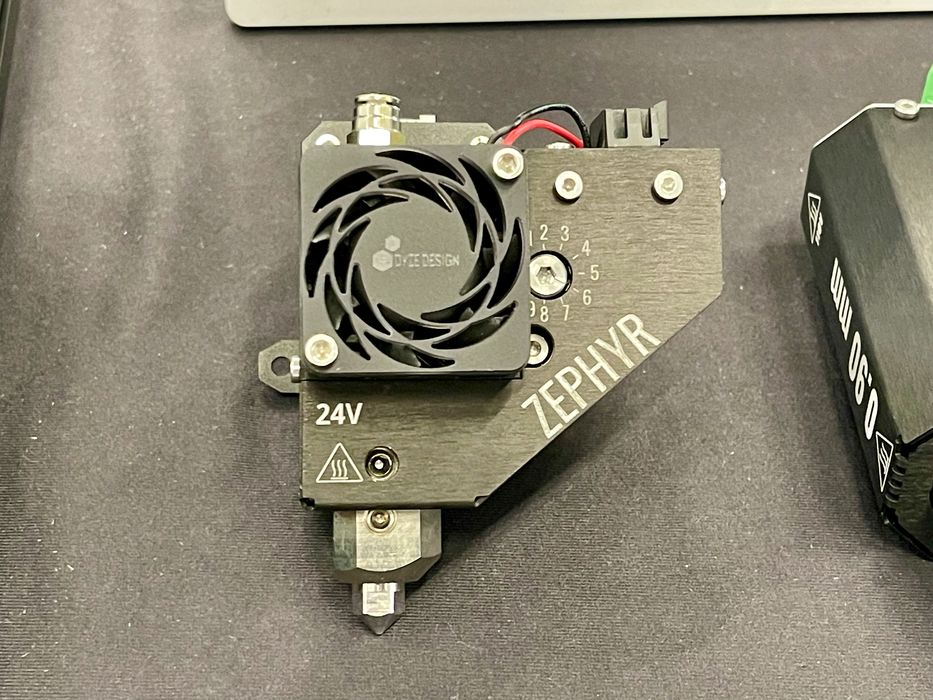
Bonus: We also got a quick look at a new extruder the company is developing, the Zephyr. This is a high flow extruder intended to deliver up to 500g of material per hour, making it very suitable for high speed 3D printing. However, as of this writing it hasn’t yet hit their product pages.
Via Dyze Design