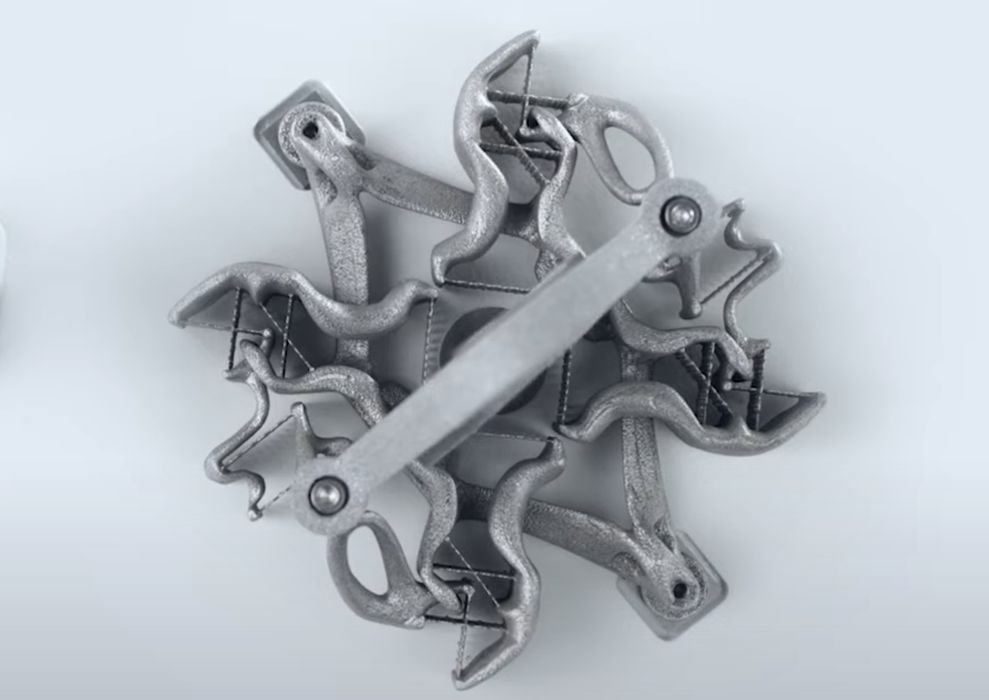
Do we have sufficient imagination to truly use 3D printing?
That might sound like a ridiculous statement, but hear me out.
Years ago when 3D printing was a new and exotic process for most companies and individuals, there was a big question: what should we make with this technology.
The answer, most often, was “we’ll make the same stuff we already make”. In other words, the parts produced were the same parts in the company’s CAD library. They were just made with a different process.
The results were bad, or at best mixed. Parts cost more to produce using AM, and sometimes took far longer to produce. Because of this “analysis”, 3D printing was largely relegated to rapid prototyping where those constraints didn’t exist. That and the fact that there were few production-capable engineering materials with which to make end-use parts.
This state existed for many years, and it was only when brave individuals within companies realized what was actually happening.
3D printer manufacturers understood this quite clearly, and realized that you shouldn’t make the same parts because they were designed for other making processes. Instead you should develop new part designs that leveraged the capabilities of the newer making technologies. This is where “Design for Additive” came from.
Those “old” parts were unconsciously designed to be made with conventional making processes. They were designed to be molded or milled, not 3D printed. Because those and a few others were the only show in town, generations of designers and engineers were brought up in that mindset. They couldn’t help themselves but conceive of designs in those styles. Anything else didn’t make sense.
Until it did make sense. Additive manufacturing equipment enabled far more design freedom over traditional techniques.
But freedom is only good if one uses it.
We then had generations of engineers who now understood that design freedom existed, but still had been trained to think otherwise. It’s asking a lot for people to fundamentally flip how they have thought about design for their entire lives.
This is, in my opinion, one of the factors that’s been holding back 3D print technology: we (the design community as a whole) didn’t know how to design for this technology.
That is changing, albeit slowly. Nowadays students learn additive technology early and the concepts are burned into their brains alongside other making processes. They don’t have the same constraints as some older designers might have.
As a result we increasingly see very unusual designs emerging from 3D printers.
One very good example is at top. It’s a “compliant rotation reducer mechanism”, made by CSEMtechnologies for the European Space Agency. This is a crazy-looking part that provides a rotational mechanical function but is a single object. You can see how it works in this video:
That’s the kind of design we should be seeing more of because today’s 3D printers are easily able to produce complex designs of this type. We just need the designs.
One more thing: the CSEMtechnologies design here was actually produced in 2019 — four years ago! This shows how slow and gradual the transformation to new design concepts can take. You will see some quite advanced designs, but many not-so-advanced designs. Over time the ratio will shift, particularly as AI-powered generative design tools become popular.
It also validates William Gibson’s famous remark:
“The future is already here; it’s just not evenly distributed”.
That’s our challenge: distribution.