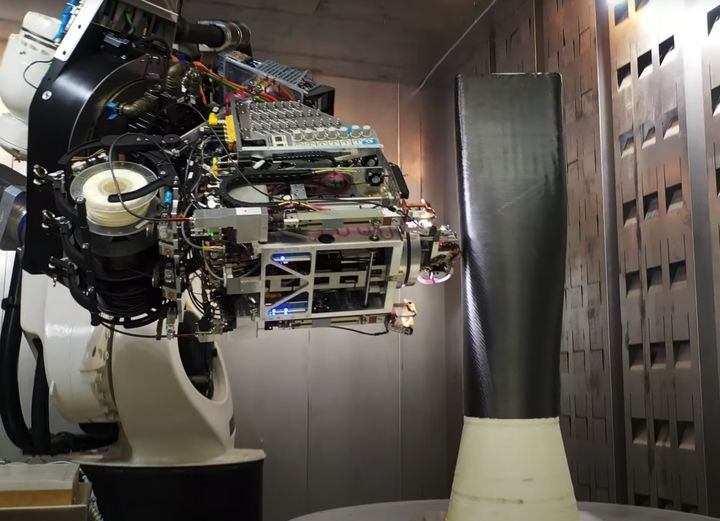
Electroimpact offers a continuous carbon fiber manufacturing solution that’s a bit different from other CCF 3D printers.
Continuous carbon fiber (CCF) is highly desirable as it combines incredible strength with light weight, making it ideal for aerospace applications. However, it’s been difficult to 3D print this material.
Many existing 3D printers offer the opportunity to 3D print “carbon fiber” filaments, but these are simply a polymer mixed with a ratio of chopped carbon fiber. Stronger results, yes, but nowhere near that of CCF.
A very few companies have developed 3D printers to insert strands of CCF into 3D prints, most notably Markforged and Anisoprint, but there are a few others also working on this capability. In some situations the parts produced are as strong as metal equivalents.
Washington-based Electroimpact takes a slightly different approach. They are a 35-year-old company located strategically near Boeing’s headquarters, with a mission to provide manufacturing automation to the aerospace industry. They offer a wide range of automation solutions, but now offer a 3D print solution for CCF applications.
Electroimpact’s SCRAM
Their process is called “SCRAM”. This stands for “Scalable Composite Robotic Additive Manufacturing”, which gives you a few clues about how it works.
SCRAM includes a six-axis robotic system that operates inside an enclosure. It can not only 3D print polymers, but also lay down CCF.
The SCRAM process involves 3D printing a polymer structure with a dissolvable material. This is done with the robotic arm moving about to create a structure layer-by-layer in the conventional manner — by robotic arm instead of a more typical Cartesian system.
Once the polymer structure is built, the six-axis system then begins to lay down CCF on the contours of the polymer structure’s surface. Essentially they are doing a CCF layup process, except that the mold is 3D printed immediately prior to CCF application. This video shows how this works:
Once the CCF step is complete, the polymer structure is dissolved, leaving the CCF object alone.
What’s interesting is that the six-axis robot can apply the CCF strands in arbitrary directions. This allows the operator to produce an object with maximum strength by ensuring the CCF strand paths align along required directions. The alignment can change as additional layers of CCF are laid down.
Electroimpact explains how this works:
“Each SCRAM cell is equipped with not only a continuous fiber-reinforced printing system, but also a rapid tool fabrication system based on an advanced FFF printing process. Conventional automated fiber layup always requires a substantial investment in hard tooling that is inflexible, expensive, and long-lead. Operators of a SCRAM cell, in contrast, can simply print their support tool on demand, starting from just a flat plate. Later, after the part has finished printing, the tool material is dissolved away. This enables rapid design iteration and allows any given SCRAM cell to be only limited by its size and the imagination of the designer. It also allows creation of part geometries such as internal channels that are difficult or impossible to produce otherwise.”
If that wasn’t enough, the system also includes the ability to 3D print chopped carbon fiber filament, just like many other 3D printers. However, the system includes a specialized laser heating system that produces “exceptionally strong bonds between layers”. This is quite interesting, and is an approach other 3D printer manufacturers should consider.
Electroimpact says the FFF component of the system can handle a wide variety of materials, including:
- PAEK family thermoplastics (PEEK, PEKK, etc.)
- Nylons and other low-temp thermoplastics (PA12, ABS, etc.)
- Water-soluble thermoplastics
- Carbon fiber
- Glass fiber
- Boron fiber
One question I have is regarding the high-temperature materials, as they often require incredibly hot chamber temperatures to prevent warping, sometimes well exceeding 100C. Typically systems with those interior temperatures isolate critical components lest they be damaged by repeated high heat exposure.
However, in the Electoimpact system it appears that the entire robot system and materials are held within the build chamber, and thus would be subjected to high heat. I’m not sure what’s happening here; perhaps the Electroimpact system does not hit particularly high chamber temperatures, unlike other dedicated high temperature 3D printers.
Electroimpact also offers a number of options, including a pellet extruder, and a CNC end-effector for surface quality machining.
Via Electroimpact (Hat tip to Benjamin)