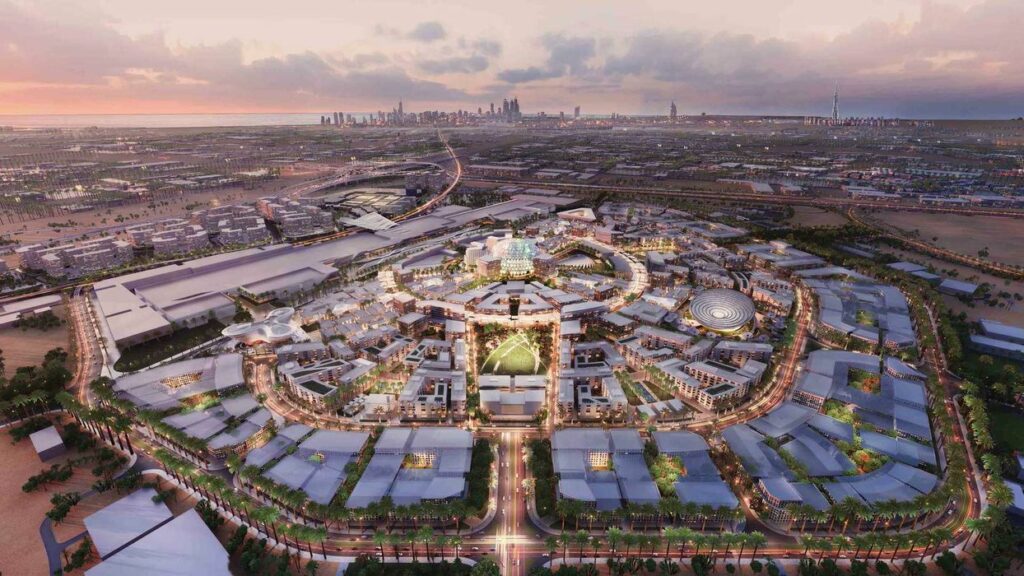
The Middle East’s first World Expo featured innovative technologies that ranged from phenotyping to 3D printing—to the Rimac Nevera.
On the outskirts of Dubai is a technological oasis that appears to have sprouted out of the desert itself. Its centerpiece, the Al Wasl Dome, catches your eye almost as if an alien spaceship has landed, bringing technology you’d think has come from the future.
Welcome to Dubai’s Expo 2020, the first World Expo to be held in the Middle East, Africa and South Asia (MEASA) region. Always happy to break a few records, Dubai put on a bombastic show as the expo took place a year late, from October 2021 to March 2022 (thanks, pandemic). With the theme ‘Connecting Minds and Creating the Future,’ Dubai’s Expo 2020 featured pavilions from 192 countries and stretched out over a massive 438 hectares—that’s more than twice the area of Monaco.
Engineering.com was at the scene to take in many of the awe-inspiring displays. For instance, the feeling of visiting distant worlds was made palpable by the presence of the moon rock, which visitors could touch at the aerospace-focused U.S. pavilion. The Italy pavilion—made primarily from orange peel and coffee grounds, and covered by ropes recycled from two million plastic bottles—featured a full-scale 3D printed Michelangelo’s David. At Czech Republic, Photon Systems Instruments claimed to “speak Plantish” by demonstrating how phenotyping technology could be used to understand the needs of plants. Singapore’s living pavilion showcased how 517 solar panels could power 170 plant types in the UAE desert while maintaining net-zero energy and water systems.
However, most of these engineering marvels were in the concept phase—unlikely to be seen in the real world anytime soon. There was one notable exception: the Rimac Nevera, which has accomplished several never-seen-before feats in the electric hypercar space.
Rimac Nevera
The Nevera is a next-generation hypercar designed and produced by Croatian automotive manufacturer Rimac Automobili (pronounced Ree-mahtz ). Named after a powerful lightning storm that strikes the Croatian coast in the summer, the all-electric Nevera aspires to cause a similar disruption in the world of hypercars.
Released in 2021, the Rimac Nevera has a whopping 1914 hp and delivers 2360 Nm of torque; that’s almost triple the output of a conventional hypercar. It can go from 0 to 62 mph (100 km/h) in under two seconds, and reaches a maximum speed of 258 mph (412 km/h)—making it the fastest-accelerating production car in the world. That it can surpass the speediest Formula 1 race cars—all while weighing a lumbering 4,740 lb (2,150 kg)—is testament to the next-level engineering within the Nevera.
Despite hailing from Croatia, a country with practically no automotive industry of its own, Rimac designed and manufactured the majority of the Nevera’s key components from scratch. The company was founded in 2009 with the approach that its engineers could become the experts in relatively new technologies, such as high-performance batteries and electric powertrains. Almost everything in the Nevera is developed in-house—from the chassis, suspension and battery pack, to the inverters, motors, pumps, fans and even buttons. Only 150 units of the Nevera will be custom-produced at a rate of one car per week, each with a price tag of $2.5 million (€2 million).
The Nevera is driven by four permanent-magnet electric motors, i.e. one motor for each wheel. Paired into a front and rear power system, these hub motors deliver different amounts of torque to each wheel independently. The front power system delivers a maximum torque of 280 Nm to each of the front motors, while the rear power system provides 900 Nm to the rear motors. ((280 Nm × 2) + (900 Nm × 2) = 2,360 Nm of torque throughout the car.)
Rimac’s software-controlled All-Wheel Torque Vectoring 2 (R-AWTV 2) system automatically adjusts each wheel’s torque up to 100 times per second. First, several sensors (i.e., accelerometers, gyroscopes, steering angle sensors and wheel speed sensors) paint a picture of what’s happening in the car. An algorithm uses this data along with pre-existing models to predict how the vehicle will behave, and calculates the optimal torques to be distributed across the four motors. According to Rimac, the system helps the car find grip levels that were previously not considered possible, adding to the car’s stability when cornering on the race track.
Read more at ENGINEERING.com