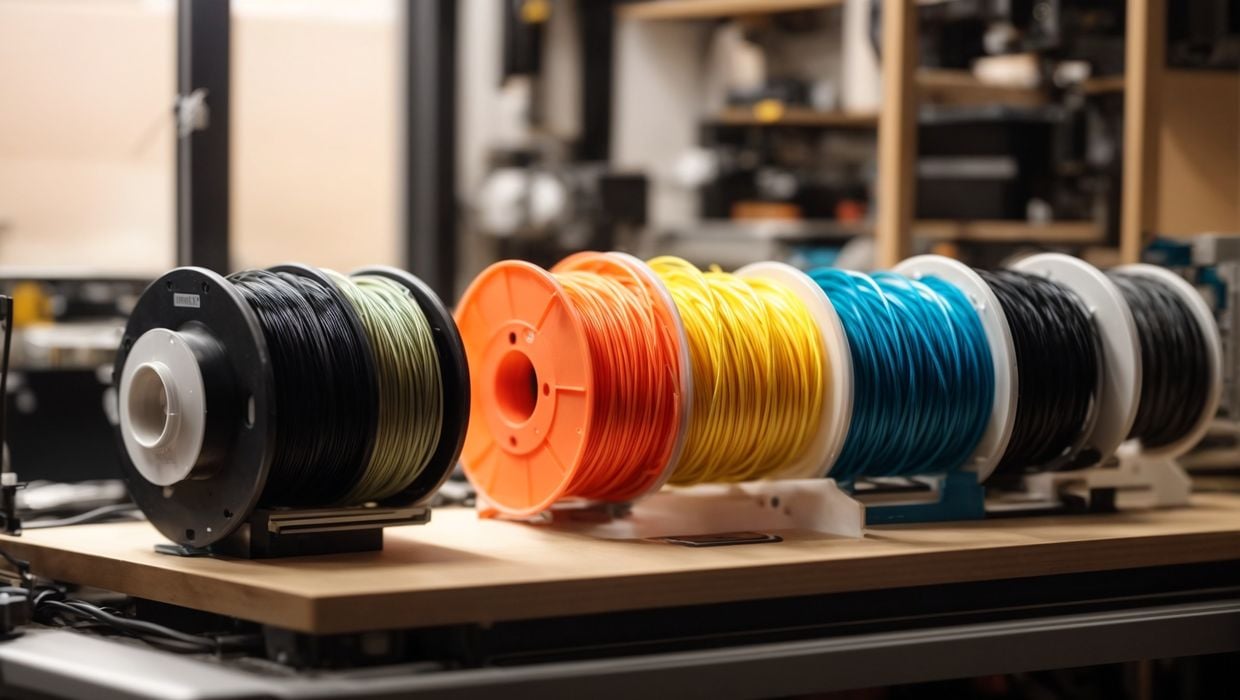
It’s 2024, and many people are making predictions.
I’m not going to make predictions, they can be wrong. Instead, I’m going to list some “hopes” for desktop 3D printing in 2024, things that I would really like to get sorted before the end of the year.
Some will be easy and obvious, but others will be ambitious.
Standard Profiles
Every FFF device needs a print profile to use with specific materials. In the past these would be developed by the operator by trial and error. Later, some 3D printer manufacturers set up sharing sites where profiles could be obtained. However, it’s really the “Wild West” out there, and profiles are found in way too many places.
My hope is that somehow a standard way to find and access profiles is developed, and a way to more easily have machines use them directly.
Spool Dimensions
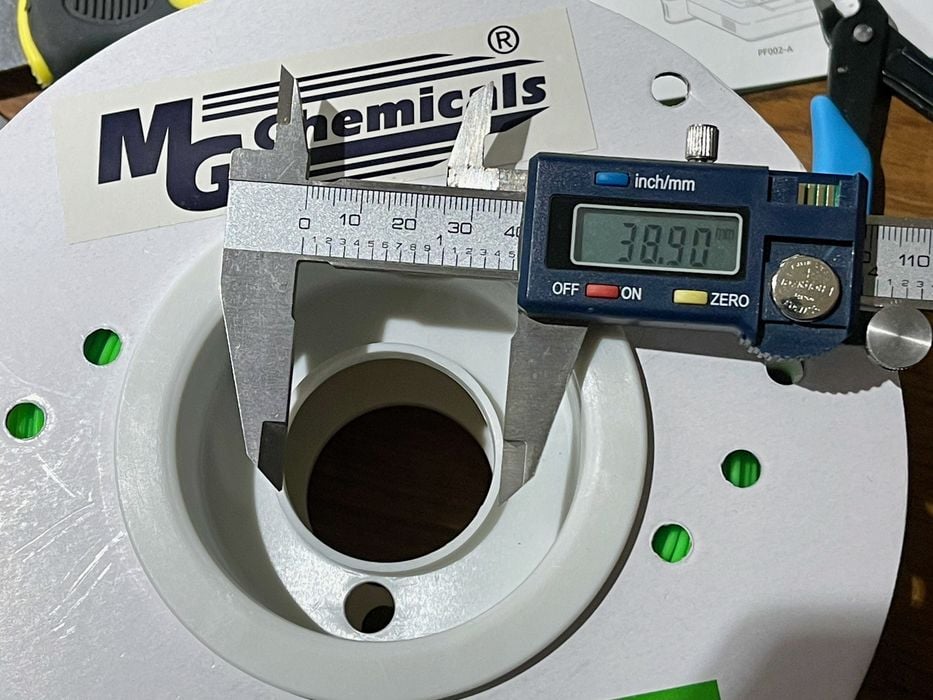
Having tested several Bambu Lab systems with their AMS, I have learned that filament spool dimensions matter. A lot.
It turns out that the AMS, a highly useful accessory to swap filaments in mid print, can only accommodate spools with a specific and small range of inner diameters. In other words, I’ve been re-spooling my collection of filaments. This is tedious and should be unnecessary.
My hope is that the 3D printer filament industry comes up with a standard spool dimension that is used by everyone, filament makers and 3D printer manufacturers.
Gentle Failures
There’s a mad scramble to catch up to Bambu Lab by all the desktop 3D printer manufacturers. Some seem to be succeeding, at least in some aspects, but many others are not. Or at least they haven’t yet announced any plans to do so.
These companies are at risk of losing a huge chunk of their client base unless they can compete. My suspicion is that some, perhaps many, will simply fail this year.
My hope is that the failures will cause as little disruption as possible, for both customers and staff of the affected companies.
Elimination of “High Speed”
Regarding “high speed”, that’s the goal of most desktop 3D printer companies. When one company (Bambu Lab) introduced their very high speed equipment, everyone else had to follow.
Unfortunately, some are doing so in name only, labeling their products as “high speed”, when in fact the devices are not nearly as “high speed” as touted.
Most of this is caused by not using the proper metric for higher speed 3D printing: the volumetric capacity of the extrusion system. No matter how fast the toolhead can move, the extruder must be able to deliver a lot of material to match that speed.
My hope is that desktop FFF 3D printer manufacturers stop using the words “high speed” and instead quote extruder volumetric capacity in their spec sheets.
Focus on Safety
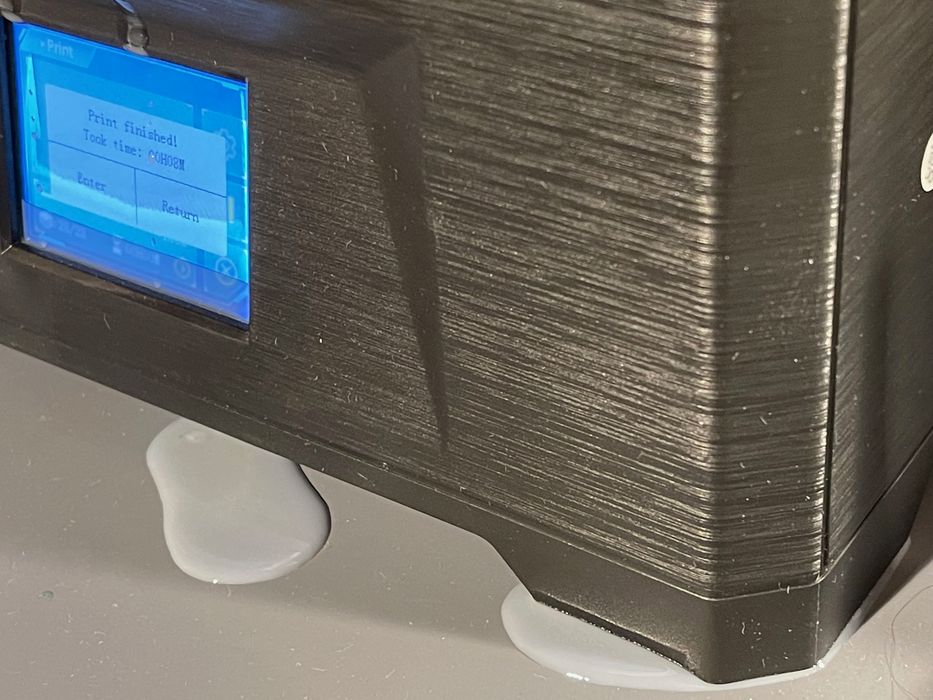
Safety seems to be an afterthought for many 3D printer manufacturers, particularly those producing resin equipment. Machines seem to be designed to just print, without regard to how messy the work area becomes. This is quite literally dangerous, as 3D printer resins are typically quite toxic, and many operators are still unaware of this fact.
My hope is that new resin 3D printer designs account for the toxicity and reduce or eliminate the possibility of operator exposure.
The End of Slow
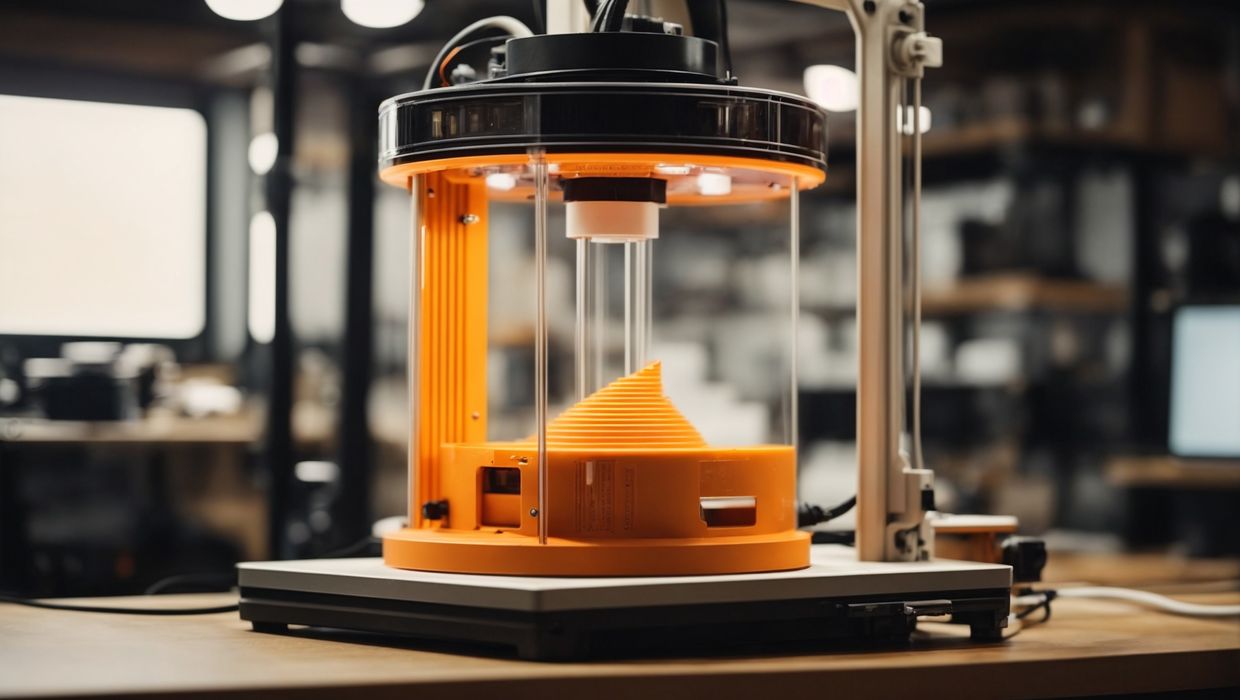
We’ve talked about high speed FFF 3D printers already, but you’ll still find many “slow” 3D printers for sale everywhere.
My hope is that these slow 3D printers actually disappear in 2024. The only FFF 3D printers we should see for sale should be high speed devices.
An Affordable Volumetric 3D Printer
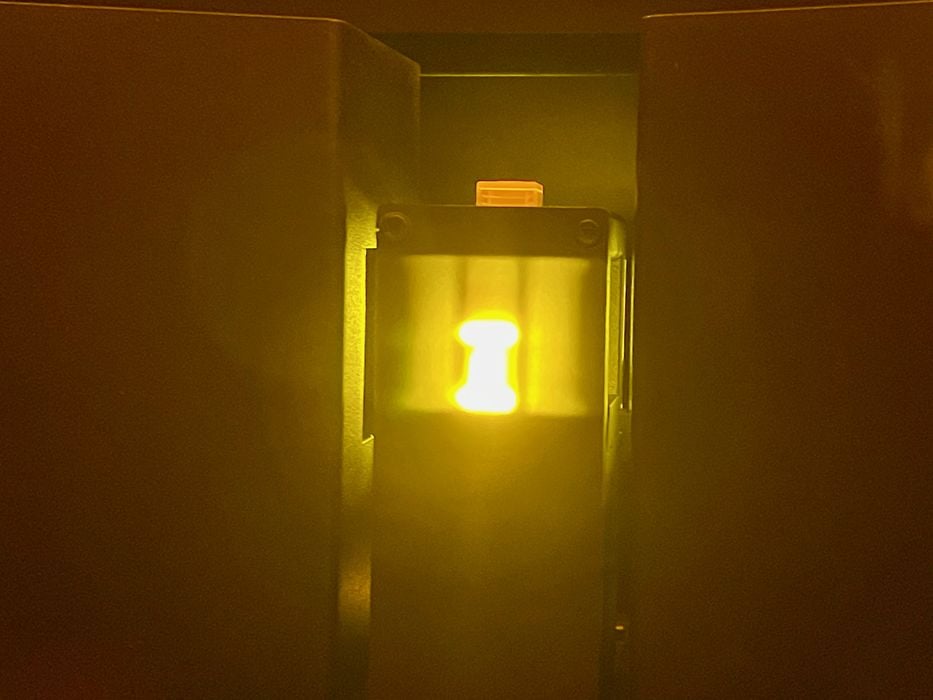
This might be wishing for too much, but I am very hopeful for volumetric 3D printing. This technique is quite different from standard MSLA or SLA resin 3D printing: instead of printing layer by layer, volumetric approaches involve solidifying the entire object all at once. This process takes only seconds or minutes, and is quite startling to watch.
My ambitious hope is that someone announces an inexpensive desktop volumetric 3D printer in 2024. This is unlikely to happen, but one can have hope. Or wait until 2025.
Color Standards
There’s vastly increased interest in color selection for 3D printer filament. Some companies, like PolyMaker, offer well over 100 (maybe even over 200?) different colors. Some other providers offer similar large varieties.
The problem is that it’s hard to tell which color is which. How is that green different from the other company’s green? If only they all used Pantone or an equivalent color identification scheme!
My hope is that filament providers adopt a standard color scheme to use when presenting their products so that we can know exactly the color being provided. Sure, this is unlikely to happen because providers want to keep buyers coming back for “that same color”, and other providers don’t even have consistent color batches. But again, let’s have some hope here.