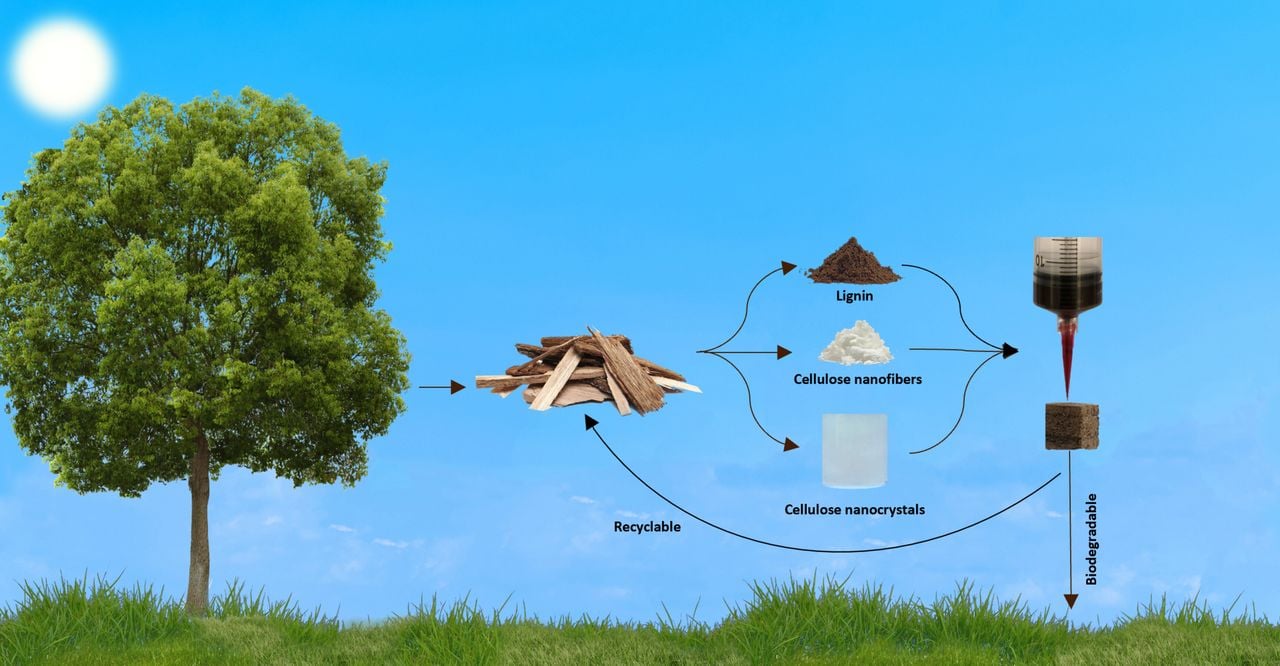
Researchers have made a 3D printing material that is entirely made from recycled wood, but there are some significant issues.
When you hear “wood material”, there are two currently used approaches in the 3D print world.
One is as a composite filament. Wood flour is mixed with a polymer, perhaps PETG or PLA, and then extruded in the usual manner. Aside from the occasional nozzle clog when larger wood fibers get caught, 3D printing this material is straightforward. The results are somewhat wood-like.
The other current approach for 3D printing wood is to use it as a powder. Binder jet systems will apply binder selectively over the powder bed, gradually building up an object layer by layer. This also produces somewhat wood-like objects.
But that’s the problem: these are not wood, they are a combination of polymers and wood. Because of that the resulting parts are not really biodegradable and have very poor recycling characteristics.
If only there was a 3D printing material made ONLY from wood.
Now, it seems there is one. Researchers in the US have made a breakthrough by developing a unique direct ink writing 3D printable material that’s entirely made from wood — no polymers, no binders are involved.
Their innovation was to extract cellulose nanofibers, cellulose nanocrystals, and lignin from recycled wood . These were combined with water in a very specific ratio to create a material similar to clay that could be extruded.
As you might expect, the resulting print would be quite wet. This leads to a complex post processing sequence.
The first step is to eliminate the water. If this was done by simple evaporation, the print would distort. Instead, the researchers used a freeze-drying technique, which involves placing the print in -85C at 0.1mBar for 48 hours. This removes the moisture entirely, and still retains the object’s geometry.
At this point the wood part is still pretty fragile, comparable to balsa wood. To toughen it up, the next step was to expose the part to +180C temperatures for a period. This melts and reforms the lignin, which strengthens the part.
Finally, the part is then pressed mechanically, which densifies the part and adds further strength.
The resulting parts are basically identical to wood — because it IS wood. The parts have all the properties of normal wood, and even smell like wood.
This is quite a breakthrough, but I fear the significant post processing steps will greatly constrain the possible applications for this new material. The steps effectively mean only smaller parts can be produced; I can’t imagine a construction 3D printer being developed to use this technology. It seems more suitable for factory production of pre-designed construction parts.
That may be its future, as there is a fantastic amount of wood construction waste. Sawdust, cutoffs, torn down walls and many other sources generate tonnes of wood waste. Typically wood waste is recycled only in simple ways: garden surfacing, particle boards (which include binder), compost, farm animal bedding, etc. This technology could allow the large scale production of complex wood parts that could take on more interesting uses.
The best part: all these prints are completely recyclable and fully biodegradable. They are quite literally wood.
Via Science Advances