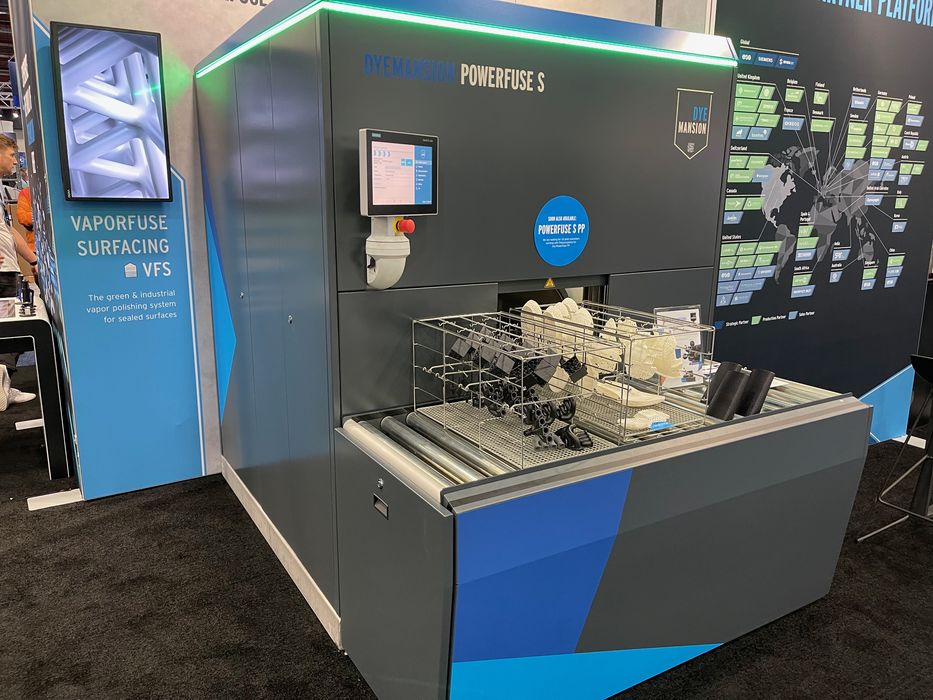
I had a chat with DyeMansion and learned they can now post process polypropylene parts.
DyeMansion, which by the way has one of the coolest company names in the industry, is all about post processing. That’s often a forgotten step in the 3D print world: virtually all 3D prints must be post processed in some way. It could be de-powdering, sintering, color dyeing, support removal, surface smoothing or more. DyeMansion makes equipment to handle most of those important tasks.
It’s important to realize there is quite a bit of science to post processing. While it’s easy to, say, color dye some nylon prints in tubs as seen here, the issue today is that manufacturing requires consistent quality for each and every part.
The approach used by DyeMansion and a very few others in the space is to have automated intelligent post processing that can consistently repeat the process time after time. That’s why companies such as DyeMansion continue to grow.
One of the services provided by DyeMansion equipment is surface smoothing. Their Powerfuse S unit uses a vapor smoothing approach: parts are exposed to a vapor that lands on the surface and softens the material. This relaxes the material and smooths it, typically erasing layer lines or other print artifacts. The Powerfuse S is able to do so consistently through its smart control systems.
An interesting aspect of this system is that the solvent used, VaporFuse Eco Fluid, is a green substance. DyeMansion explains:
“Our eco-friendly VaporFuse Eco Fluid solvent is non CMR and approved for the processing of plastics with food contact according to regulation (EU) 10/2011. The solvent is circulated continuously in a closed loop and automatically recovered by the system. This enables a sustainable contact-free process without chemical waste. Operating the Powerfuse S does not require protective clothing against chemical hazards.”
The news is that DyeMansion has adapted the Powerfuse S to now handle polypropylene parts with the new Powerfuse S PP machine. I’m not aware of other automated post processing systems that process PP, so this could be a unique capability.
Like the original Powerfuse S, the Powerfuse S PP also uses a green solvent for processing. DyeMansion also indicated they can process TPU parts from certain materials suppliers.
PP is a very popular material, particularly for commonly used tools, kitchen items and much more. The ability to reliably smooth 3D printed PP parts at production scale could open up many more possible applications for 3D printing.
The Powerfuse S PP is not quite available, but DyeMansion is seeking pilot customers to test out the equipment. If you’re a manufacturer of 3D printed PP parts, you might want to contact DyeMansion and test the Powerfuse S PP.
Via DyeMansion